Addressing Immediate Risks: Challenges and Countermeasures in Corporate Occupational Health and Safety Culture Professionals
This interview was first published in Japanese on Risk-taisaku.com
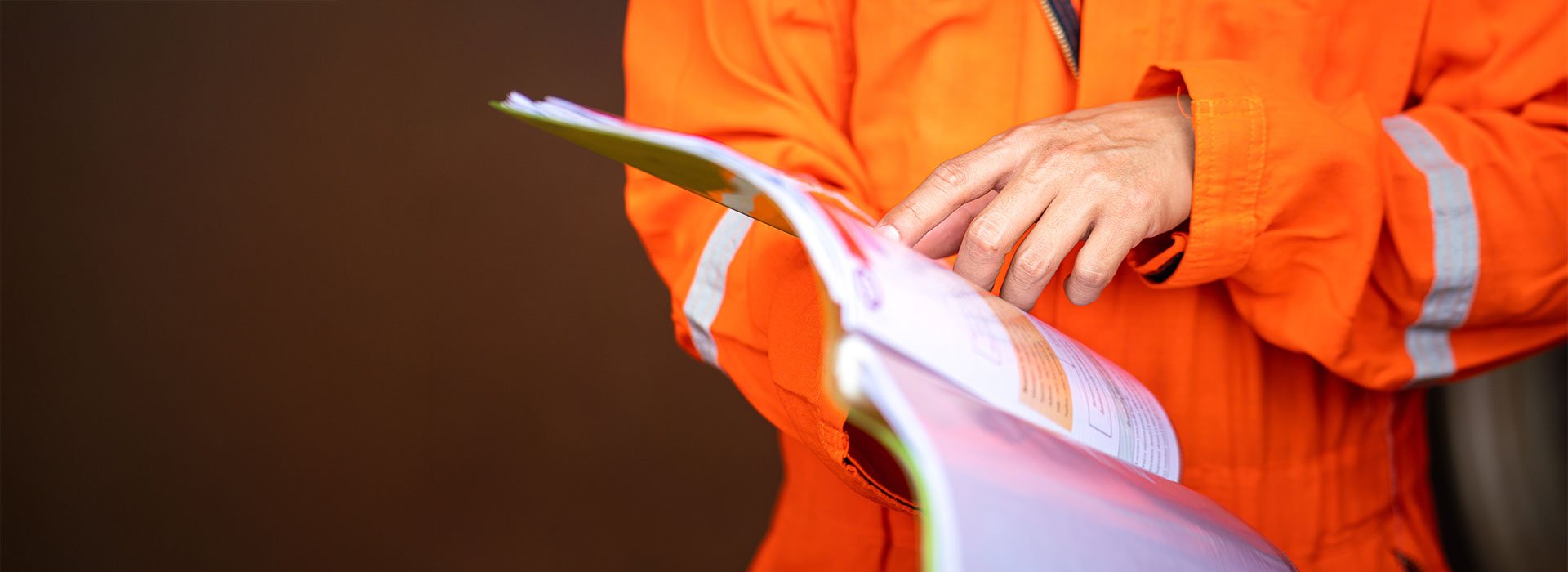
In these turbulent times, it's crucial to reassess our immediate risks. Experts in corporate occupational health and safety culture discuss challenges and countermeasures.
The risk to business continuity for companies worldwide has risen dramatically due to the unexpected pandemic and the onset of geopolitical war. However, ensuring the fundamental safety of employees must never be overlooked. dss+, a global consultancy which provides organizational safety assessments and tailored safety improvement programs based on customer needs and situations, discussed the importance of recognizing and ensuring safety against unseen risks in today’s era with Dr. Tomohisa Nagata, an associate professor at the University of Occupational and Environmental Health, Japan, who researches health management.
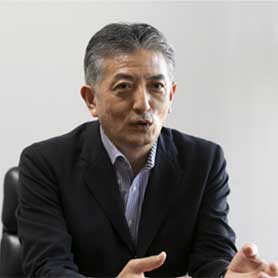
Mr. Hiroyuki Kurokawa
Representative, dss+, Japan
Former Operations Manager, Performance Polymers Division, DuPont Japan

Dr. Tomohisa Nagata
Associate Professor, Department of Occupational Health Management, Institute of Industrial Ecological Sciences University of Occupational and Environmental Health, Japan
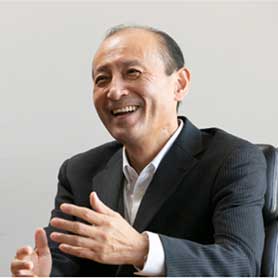
Mr. Yoshiyuki Tanaka
Special Advisor and Consultant, dss+, Japan
Former CEO, DuPont Japan
Top-level Risk Awareness: A C-suite Imperative
In Japan, over 800 people still die each year due to work-related accidents. The number of fatalities and injuries from accidents causing more than four days of absence has been increasing since 2018. What are the current challenges regarding health and safety - the two pillars which are essential for protecting employees?
Nagata: "For us, industrial physicians, the most important role is preventing work-related health disorders. We focus on reducing invisible, future disease risks, a priority within 'occupational health' that requires proactive measures. Top-level understanding is crucial for companies to mitigate risks. For example, when the CEO spoke about smoking cessation, employees who had ignored previous calls quit smoking immediately. This highlights the importance and the need for us to help top management understand risks to implement effective measures."
Kurokawa: "As an operations leader at DuPont, I prioritized factory safety management. Health and safety mindsets are critical throughout the process from hiring to daily operations. However, it's often taken for granted, with potential dangers going unnoticed. Failures in safety management become evident only when accidents occur; otherwise, risks remain hidden. Like occupational health, safety management involves dealing with hidden risks, presenting its own challenges."
Tanaka: "In Japanese companies, there's a consistent pattern of failing to address hidden safety risks. After an accident, efforts are made to address it, but after a few years, it's often forgotten, leading to a recurrence of similar accidents. The root cause is the failure to recognize hidden risks and institutionalize risk awareness, even among top management."
Nagata: "We've found that more communication opportunities between industrial physicians and top management, along with a better understanding of top management's concerns, enable more effective corporate health initiatives. Based on research, we've created a checklist to help industrial physicians communicate with top management to reduce health risks and provide support."
Kurokawa: "In Japanese companies, safety management is often detached from top management, which should be central to leadership. Safety and occupational health departments are responsible for corporate safety, but their policies may not delve deeply into actual risks or secure necessary budgets for implementation. Business units may be reluctant to undertake labour-intensive safety measures, and top management often feels reassured by accident-free records without considering hidden risks. Support for top management's risk awareness is necessary in safety management, similar to occupational health."
Tanaka: "To enhance top management's risk awareness, we offer the 'Safety Perception Survey' to understand the company's current situation. Developed by DuPont based on data from over 7,000 global companies and more than one million individuals, this survey reveals the company's weaknesses and its safety culture level on the Bradley Curve™. For example, while many Japanese companies score high on safety at the management level, operational level scores are often lower, indicating a lack of emphasis on safety at the operational level and a disconnect in top management's grasp of frontline conditions. This survey is useful for identifying potential risk areas, visualizing safety culture, and measuring overall organizational risk."
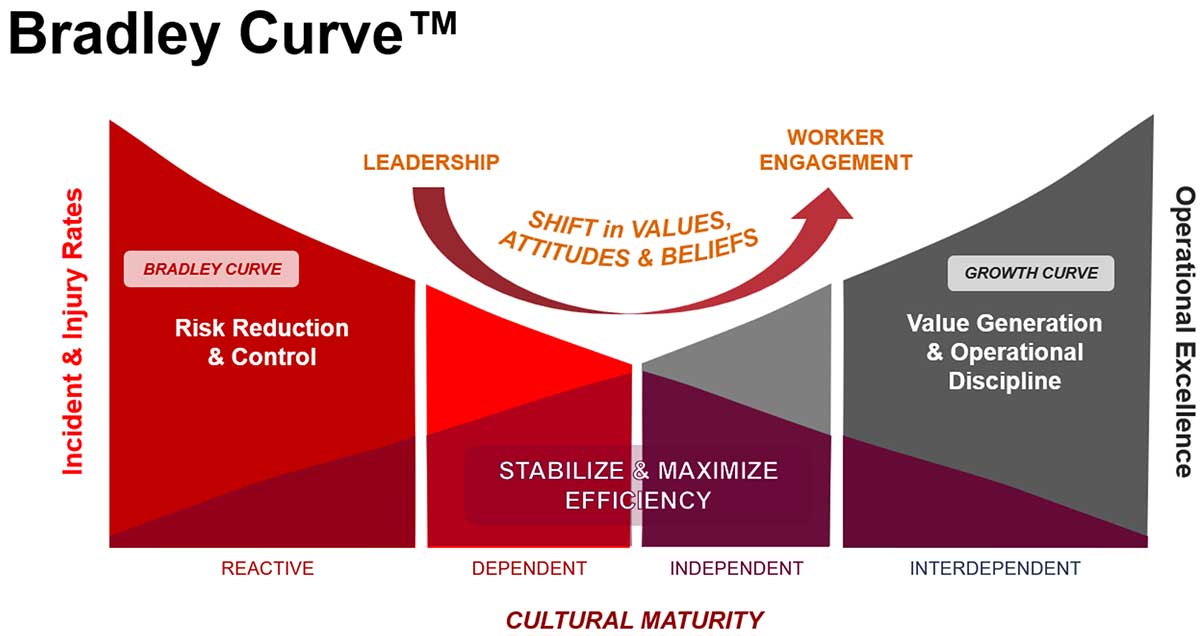
Compliance with regulations is an initiative aimed at achieving the minimum standard. Investing in health and safety contributes to enhancing corporate value.
Is society demanding a dedicated focus on labour health and safety?
Nagata: "Recently, I've focused on the accumulation of 'intangible resources.' My specialty is health management, which involves strategically managing employee health under executive leadership. Health management initiatives provide short-term benefits like improving lifestyle habits and promoting exercise, but they also contribute to the accumulation of intangible resources."
"One intangible resource that has gained global attention is Perceived Organizational Support (POS), where employees feel their company supports their health. Additionally, social capital, such as indirect connections between individuals, is also considered important.
Through health management initiatives, the accumulation of intangible resources increases participation rates in health initiatives and enhances their effectiveness. Companies with high levels of intangible resources experience lower turnover rates and higher levels of work engagement, characterized by vitality and enthusiasm. As a result, there is an increase in awareness on the importance of health and safety awareness among top executives and management towards frontline workers."
Kurokawa: "There's a concern that only the person in charge is prosecuted, while corporate responsibility is left unquestioned. Rather than pursuing legal accountability against top executives, it's important to understand the gravity of their responsibility.
However, this differs from mere compliance with laws. At DuPont, we believe 'laws represent the minimum standard of common sense.' While we talk about compliance with laws, our actions often aim only to meet the minimum standard, which doesn't adequately protect employees from accidents. We must aim higher than the minimum standard.
Article 3 of the Labor Safety and Health Law states that 'employers must not only comply with the minimum standards prescribed by this law for preventing occupational accidents but also...' This clarifies that the purpose is not merely to comply with minimum standards."
Nagata: "The Labor Safety and Health Law, which established provisions for worker safety and health, was enacted in 1972. Its legislative purpose is to ensure worker safety and health. Compliance with laws is often thought of as adhering to written rules. However, as Kurokawa-san mentioned, true compliance with laws involves achieving the overarching goal in its original sense."
Kurokawa: "In this era of unexpected pandemics and unforeseen conflicts, where uncertainty is heightened, it's more crucial than ever for companies to pursue sustainability and business continuity. Aiming for mere compliance with regulations, which represents the minimum standard, offers no prospect of positive gains akin to investments. Instead, it resembles moving towards negative gains while taking on high risks. It could be said to be going against the tide of the times."
Fostering a safety culture that pursues safety. How can leaders take proactive steps to shift the mindset and behaviours?
So, what is necessary to overcome compliance with laws and regulations without just paying lip service to them?
Tanaka: "I believe the key lies in fostering a safety culture. In recent years, incidents of data tampering and fabrication have been rampant, particularly in manufacturing. The reasons for data tampering vary, including profit-seeking and concealment. Often, when data tampering occurs, top management issues statements claiming 'there is no quality issue' and attempts to settle the matter with apologies. However, from DuPont’s perspective, this approach feels unsettling. One of DuPont’s four core values is 'highest ethical behavior,' where we uphold corporate ethics. Data tampering or fabrication, which involves false reporting, is not just a quality issue but a violation of corporate ethics. By setting higher ethical standards, we can truly ensure quality. Similarly, to ensure safety, it's essential to foster a safety culture that fundamentally pursues safety, even if it doesn’t extend to corporate ethics."
Kurokawa: "We organize workshops with our management where they have the opportunity to objectively reassess our company’s operations. In these sessions, we deliberately revisit and learn about the 'importance of safety,' encouraging participants to think deeply about it and share their perspectives. We empower them to recognize, assess, and improve risks themselves, and support them in implementing the PDCA cycle. It’s crucial that management acknowledges the current situation and demonstrates proactive actions towards improvement. This is the first step in creating a safety culture."
Nagata: "Support, including PDCA, is indeed crucial. At the beginning of 2022, we conducted interviews with institutional investors and surveyed disclosure practices related to occupational safety and health among listed companies in Japan. While Japanese companies have made progress in information disclosure, there was a common sentiment that it’s unclear whether the PDCA cycle is being effectively implemented. For instance, when there is a sudden increase in the frequency rate of occupational accidents in a particular year, stakeholders noted the lack of detailed analysis of the change and descriptions of implemented measures. This makes it difficult to assess whether occupational safety and health practices are functioning properly.
To enhance corporate value, it is important to consistently provide clear explanations that outline challenges and corresponding improvement measures. As mentioned earlier, if top executives and management teams recognize risks thoroughly and initiate improvement efforts, it contributes to the accumulation of 'intangible resources'. This concept applies not only to health but also to occupational safety, where efforts to manage safety risks serve as a catalyst for fostering a safety culture."
Kurokawa: "At dss+ Japan, we have implemented end-to-end labour safety mechanisms, refined through 200 years of trial and error, rooted from our heritage at DuPont. With our proven practices and deployment, we have helped enhance corporate sustainability and ensure business continuity. We look forward to journey with you to achieve these goals."