Adopting a risk-based approach to reduce risk and unlock hidden potential
In the current resource-constrained business environment, organisations need to ensure financial resilience through cost discipline and cash preservation while maintaining a strong awareness of the day-to-day risks inherent to their operations and facilities. A cost-effective risk-based approach is now more important than ever to ensure safe, reliable, and profitable operations by guiding the organisation’s decision-making and resource allocation, especially in light of the COVID-19 global outbreak which is posing additional disruptions. A risk-based maintenance strategy helps ensure the integrity of critical assets, while a structured approach to defect elimination will unlock plant hidden potential, with a significant contribution to unit cost reduction. It is imperative that an organisation, aligned to business and operational priorities, acts fast and efficiently. For this purpose, a Management Operating System should be utilised as a platform to drive focus on key risks and value drivers, from leadership down to the frontline.
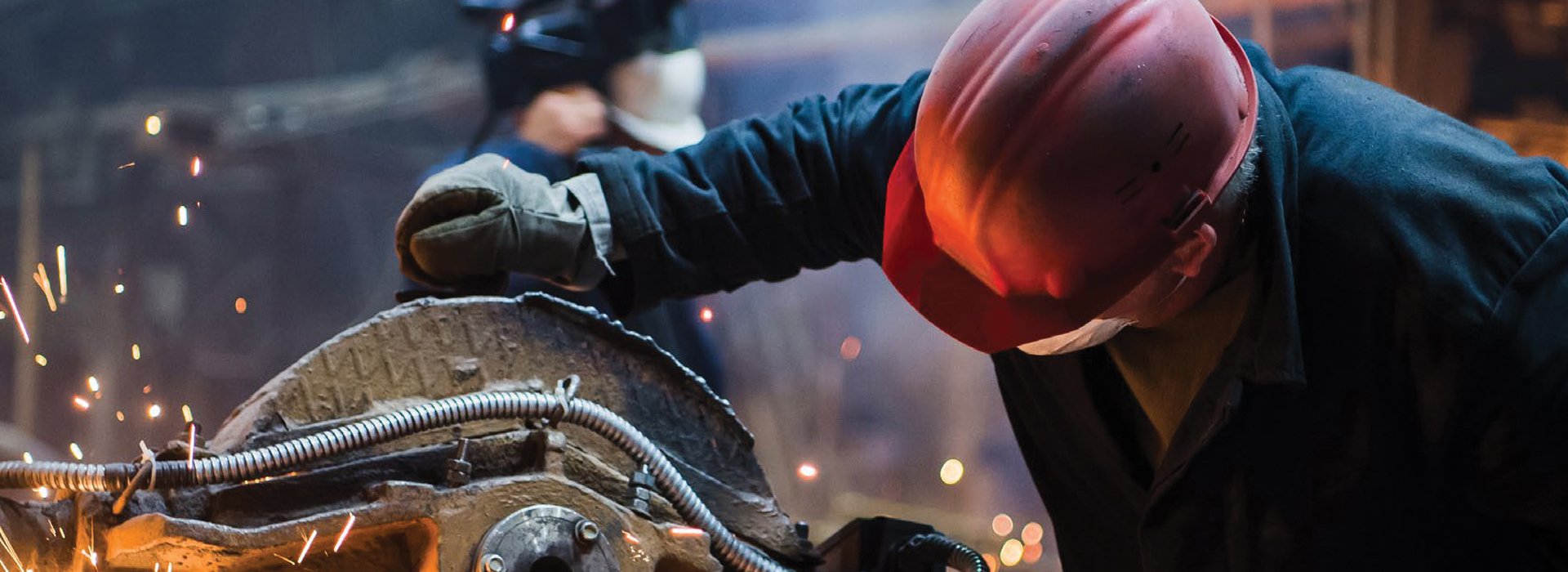
The metals industry continues to suffer significant impacts from their operational risks.
The metals processing industry such as steel, aluminum, base, and precious metals, is inherently exposed to operational risks with the potential for serious injuries, fatalities and significant impact on the environment, production and business performance (Fig. 1).
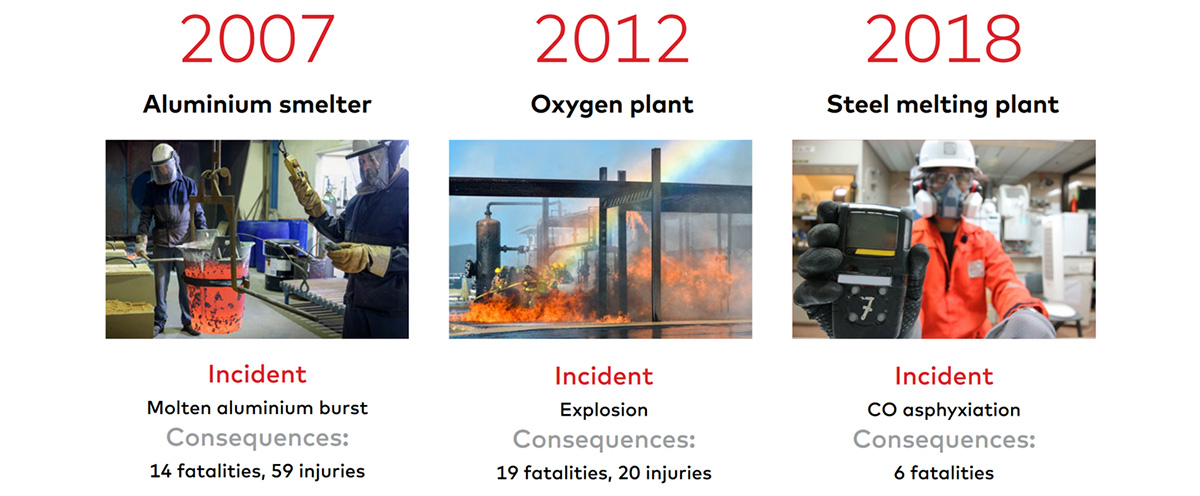
Figure 1: Examples of major process safety incidents in the metals industry
The negative impact of operational incidents arising from hazardous processes and facilities is experienced much more frequently than general perception would suggest. In fact, 42% of participants of a recent dss+ Metals Series webinar confirmed their organisations have had more than one process safety incident in the last 3 years, with an additional 15% experiencing one material event during that time (Fig. 2).
In situations where less severe events occur with no consequence on people, the business impact can still be significant, materially affecting the company’s balance sheet and absorbing considerable senior management attention to mitigate the possible impact on the supply chain and company reputation (Fig. 3).
The occurrence of process safety incidents in the metals industry is a visible manifestation of underlying operational, capability and cultural challenges often found in organisations.
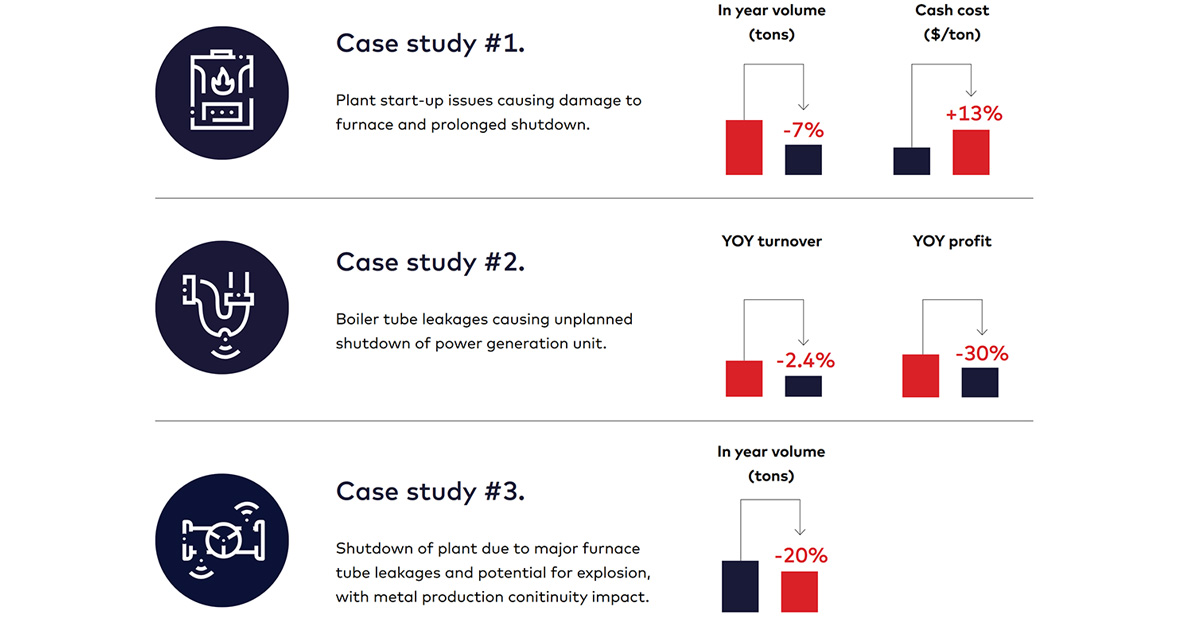
In fact, participants of the dss+ Metals Series webinar acknowledged the limited identification and understanding of risks associated with assets and operations within their organisations, as well as the inadequate operational discipline in the implementation of systems and execution of day-to-day tasks, were the two main contributing factors leading to increased operational risk and poor asset performance (Fig. 4).
The webinars' participants also recognised that the two above factors clearly affect the organisations' ability and effectiveness to adequately preserve the integrity of critical assets and proactively identify and eliminate bad actors to unlock hidden plant capacity and drive continuous improvement in plant performance.
Inadequate risk-based maintenance strategy and defect elimination, as well as inaccurate maintenance planning & scheduling – and its execution thereof, were also recognised as priority themes by webinar participants, preventing the achievement of the full potential within the organisation (Fig. 5).
A risk & value-based approach is imperative to cost-effective resource allocation
In the current challenging business environment, it is critical that organisations allocate required resources in a cost-effective manner to support safe, reliable and productive operations. A risk & value-based approach provides organisations with the basis for effective prioritisation of efforts, resources and finances by focusing on what matters most, as not all equipment or processes have the same impact on safety, business continuity and operational performance. This approach starts with proper identification of key risks associated with assets, processes, activities and changes, as well as gaining a strong understanding of the organisation's risk profile and key value drivers of operational and business performance. Subsequently, companies can drive cost effectiveness through focused and targeted investments, both in terms of financial and human resources, that are proportional to the level of risk and the opportunities.
For example, a maintenance strategy for critical equipment should be different from that for non-critical equipment given the varying levels of risk and potential impact of failure on people and the business. As a result, a high level of discipline and effectiveness should be applied to the planning and execution of maintenance tests and inspections concerning critical equipment. This will ensure adequate preparation to reduce the potential of unwanted inefficiencies or deviations from procedures in managing such critical equipment (e.g. availability of spare parts, necessary competency, etc.).
Overall, companies adopting a risk & value-based approach to manage their assets, operations and people are more effective in aligning the organisation and executing on the right priorities, therefore allocating available resources cost-effectively (Fig. 6). Asset integrity management provides a solid foundation to asset performance.
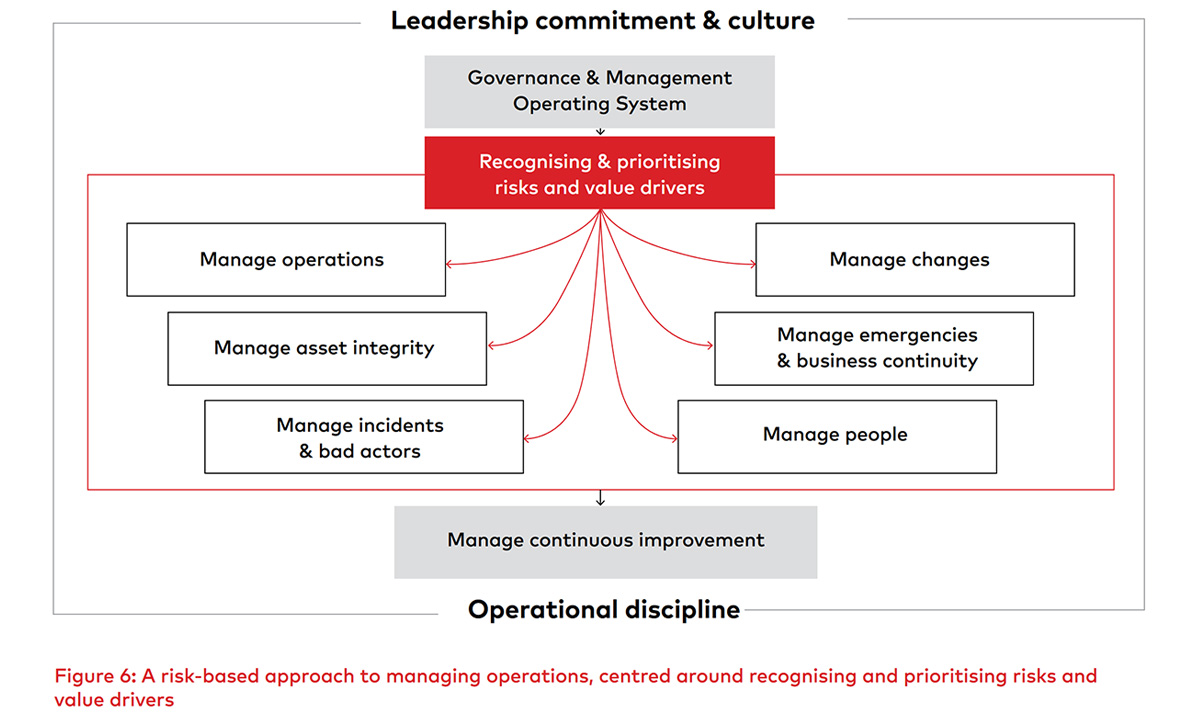
Effective asset integrity management was identified by webinar participants among the top priorities for organisations to mitigate risk and provide a solid foundation to enhance performance through higher reliability and utilisation of assets. About one-third of the participants felt the assets in their organisation were either in need of immediate attention or needed to be addressed as a high priority, while 51% felt that applying continuous improvement practices on all core Asset Integrity Management (AIM) related practices was required (Fig. 7)
This further demonstrates the need for a strong and focused approach to asset integrity in the metals industry. In fact, inadequate asset integrity has been a key factor behind numerous incidents (e.g. catastrophic molten metal releases, explosions, fires, etc.) in the metals industry with a significant impact on people, the environment, company assets, production and company reputation. But catastrophic incidents are not the only consequences that can result.
For example, an organisation reported a 30% decrease in their year-on-year profits mainly due to an unscheduled plant shutdown following leaks in two of their four boilers. The organisation incurred higher maintenance expenditure to rehabilitate the two boilers and repair associated equipment. This caused production loss for a period of time, clearly demonstrating the direct and opportunity cost associated with not adequately maintaining critical assets.
It is imperative to adopt a risk-based approach when designing and deploying Asset Integrity Management programs. Typically 80% of risk originates from just 20% of assets. Being aware of the organisation’s highest risk assets is an important filter to identify where to apply resources and effective asset management strategies and methodologies, which is particularly important in the resource-constrained metals industry.
Once an organisation has understood the risks in its facility, identified critical assets and established critical controls, it can then focus on driving the highest level of operational discipline to ensure proper integrity, reliability and functionality of those critical controls and assets.
Maintenance function: From a cost center to creating value by releasing hidden capacity
The maintenance function plays a strategic role that goes far beyond merely preserving asset integrity and functionality. A structured approach to defect elimination in maintenance can drive real and sustainable improvements in asset and operational performance, which ultimately reduce unit cost of production. In low maturity organisations, maintenance is often treated as a cost that organisations have to bear and minimise, but instead, it should be viewed as a value generator. Through a cost-effective risk & value-based approach, asset breakdowns are minimised, defects can be eliminated and increased reliability and asset performance can be realised.
For example, during a recent diagnostic at a metals processing facility, 11% of production losses were attributed to unscheduled downtime and a 5% rate loss was due to equipment failure.
Building a defect elimination mindset and capabilities, as a collaborative effort across all levels and functions of the organisation and not only as the maintenance responsibility, is essential to moving from protecting assets to improving asset performance and unlocking hidden potential.
A high level of Operational Discipline is critical to reducing risk and enhancing performance. Improving operational discipline is one of the key challenges faced by many organisations in the metals industry and is an element that greatly influences the execution and effectiveness of all controls and processes. Best practice procedures and processes designed to mitigate risk, protect assets and run efficient operations are indeed not sufficient to achieve and sustain safe operations. Operational discipline is critical to translating procedures into effective actions. Our definition of operational discipline is “everyone ... do it right ... every time”, from leadership to frontline.
At the individual level, the necessary knowledge to safely and efficiently perform a job, and the right mindset of “doing the right thing every time,” are both critical. At the organisational level, operational discipline is really the collective “way of working” across various organisational levels and departments. Two-way lines of communication, clear ownership and accountability, a fit-for-purpose Management Operating System (MOS), identification and tracking of meaningful KPIs and metrics, and – most importantly – effective visible felt leadership strongly influence the overall way of working and the organisation's effectiveness.
The Operating Model provides the platform to drive a seamless focus on risk and performance
Managing operational risk is really about managing the operations and business with "risk in mind" to achieve set goals and objectives. It is not about adding layers of management systems. Key to successful and sustainable risk management is therefore the integration of risk awareness in all key business and operational processes and decision-making.
For this purpose, an Operating Model or a Management Operating System (MOS) is the ideal platform to ensure seamless and effective integration of key risk and value drivers into planning, scheduling and performance reviews which take place across all levels of the organisation on a routine basis (e.g. yearly, monthly, weekly, daily, etc.).
For example, shift handovers and shift starts are typical MOS routines used to align the frontline crews on daily execution priorities. These are key routines in which operational risk and performance can be reviewed and discussed to ensure focus on the right priorities, align on the high-risk jobs scheduled for the shift and ensure critical controls are understood and implemented to mitigate risk and drive performance.
Similarly, leaders must be fully aware of the top risks in their facility and on the health of key controls and underlying systems and processes which ensure the risks are under control. Ultimately, leaders need to drive resolution of the systemic root causes that impact the risk profile and performance of the organisation.
By integrating risk into MOS routines, the level of risk awareness and the ability to spot early signs of degradation of risk controls and assets is greatly enhanced over time. The benefit is to gradually shift the organisation's maturity from a "find and fix" mindset to a "predict and prevent" approach and culture.