Australian Agri-Food Safety: Culture Change
Australian agri-food businesses face mounting safety challenges. This article explores how to cultivate an independent safety culture, moving beyond compliance to achieve zero injuries. By leveraging the dss+ Bradley Curve™, organisations can empower leaders, enhance risk awareness, and drive sustainable safety improvements, leading to greater operational efficiency and employee engagement.
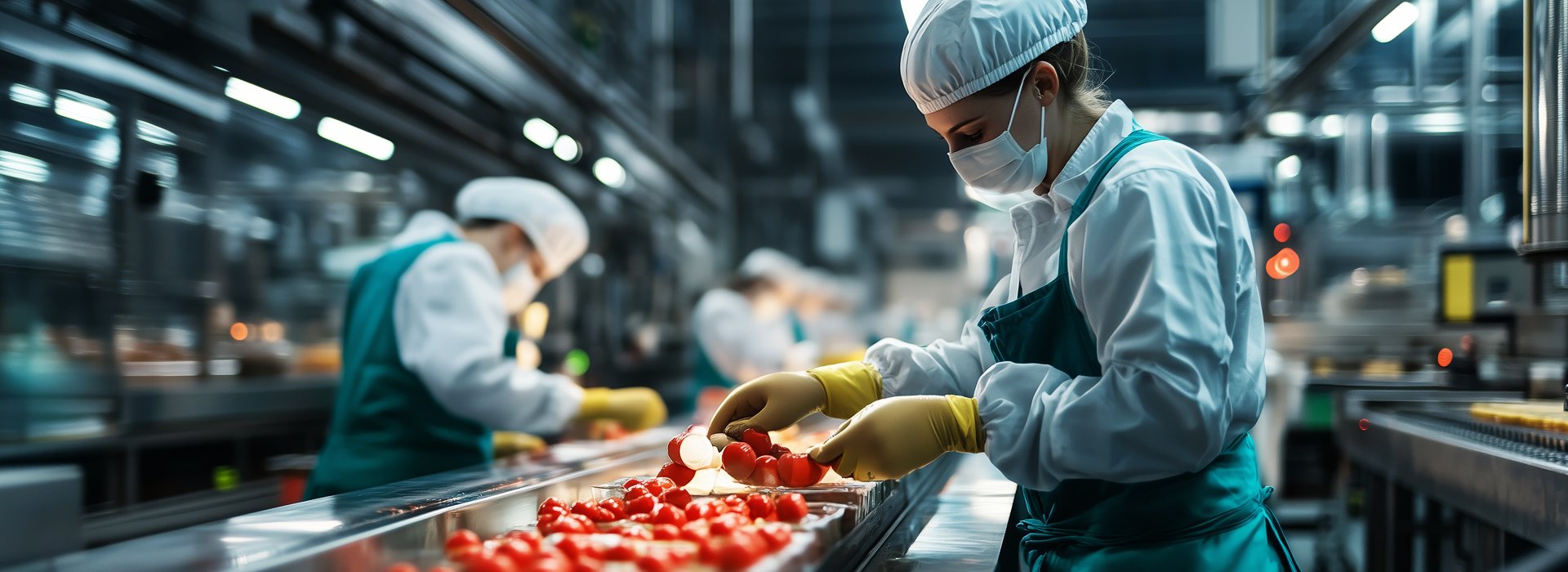
Cultivating a Safer Workplace: Transforming Culture in Australia's Agriculture, Food and Beverage Sector
Australian food, beverage, and agriculture businesses want to do better—less waste, produce at higher rates, enhance quality and keep everyone safe. One powerful way to make this happen is by changing the way people think and act at work.
But how does an organisation move from a 'just follow the rules' mindset to one where everyone truly cares about safety?
Why Culture Matters
Extreme climate events are affecting workers and supply chains. Workforce shortages are commonplace. New regulations rightly require protection for employees' mental health. Companies across Australia are grappling with new and bigger challenges every year. At dss+, we have seen that those with strong safety cultures are in a much better position to weather these issues and quickly seize opportunities as they arise. What's more, a positive shift in culture can deliver greater employee engagement and operational efficiency coupled with higher awareness of risks.
For example, one of Australia's largest food manufacturers saw a 50% drop in incidents after completing a program to change how everyone—from executives to the frontline—thinks about safety. For the first time, employees believe that 'zero injuries' are possible.
One of Australia's largest food manufacturers saw a 50% drop in incidents after completing a program to change how everyone...thought about safety. For the first time, employees believed that 'zero injuries' is possible.
A Way of Looking at Culture
The dss+ Bradley Curve™ was created to help understand, benchmark, and guide conversations around performance cultures.
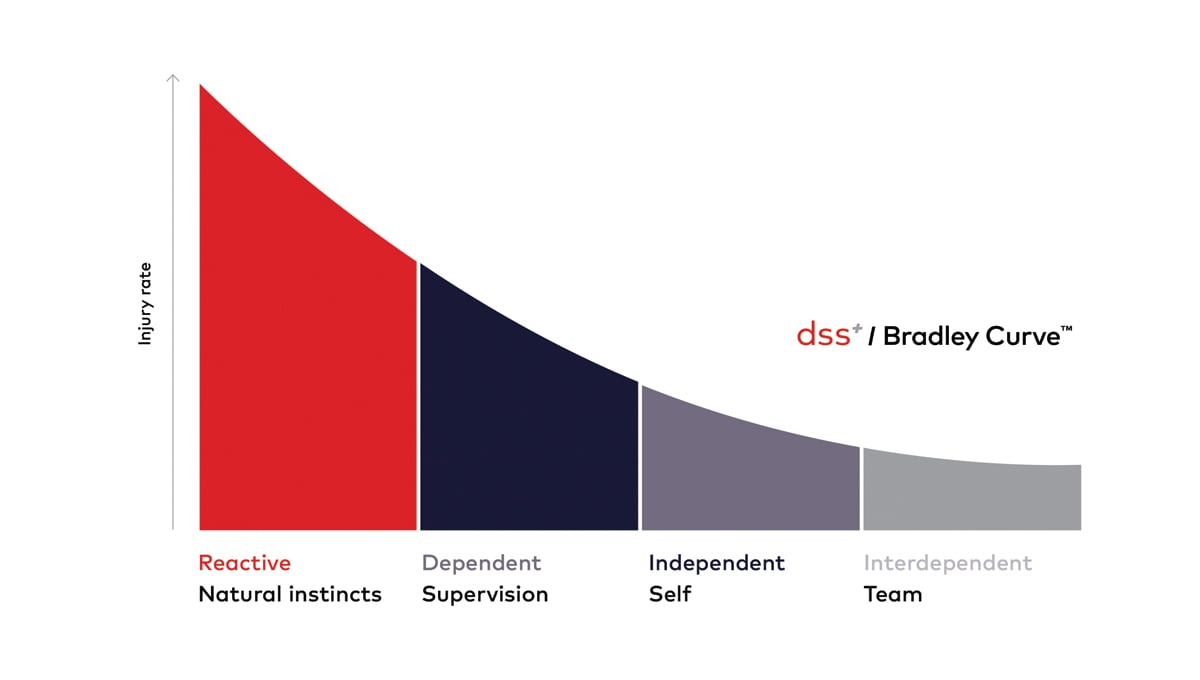
The model lays out four stages of cultural maturity as it relates to safety:
- Reactive: People don't take responsibility and believe incidents will happen.
- Dependent: People view safety as following the rules. In a Dependent culture, incident rates decrease, then plateau.
- Independent: People take responsibility and believe their actions make a difference, helping further reduce incidents.
- Interdependent: Teams across the organisation work together and feel ownership for safety performance. They believe zero injuries is possible when everyone contributes to that goal.
When an organisation's efforts have helped them progress to the right-hand side of the Bradley Curve, employees are engaged, empowered, and recognised for their contributions.
One dss+ food manufacturing client cut shutdown times by 25% and raised completion rates by 23% when they taught leaders how to 'walk the talk' around safety
Progressing through these stages unlocks tremendous value in safety and operational excellence, as well as reducing risk. In fact, moving forward one step—from a Dependent to an Independent culture—delivers real benefits. One dss+ food manufacturing client cut shutdown times by 25% and raised their work completion rate by 23% when they coached leaders in how to 'walk the talk' around safety and created new reporting structures as part of a larger engagement.
For a leader in the dairy industry, building a culture of care and developing line manager skills led to a more engaged, trusting workforce and a continuous safety improvement mindset. The result? Fewer serious injuries and no fatalities, and projections of fewer incidents going forward.
Achieving Compliance, Plus
Many Australian food, beverage, and agriculture businesses are mired in a Dependent safety culture marked by:
- A policing-style approach to upholding rules
- Blaming individuals in response to incidents
- Overreliance on supervision and directives
- Limited employee ownership of risks
Certainly, compliance is critical to a safe, effective operation. However, a solely compliance-driven mindset can limit workers' sense of accountability and initiative.
Many clients who find themselves in a Dependent culture engage dss+ when their safety performance invariably plateaus. As these organisations aim even higher and make safety a strategic priority, they advance further towards zero incidents, driving growth in innovation and value.
Keys to an Independent Safety Culture
Progression to an Independent culture is essential for moving safety performance forward and achieving an organisation's full potential. Here are four ways you can start the journey now:
- Know your current state. The first step is to identify where your cultural maturity sits on the Bradley Curve. This will allow you to see gaps and opportunities, and understand how it aligns with your strategic plans and risk appetite.
- Empower leaders at all levels to think for themselves. dss+ have had tremendous success with leader-led initiatives that coach those at every level of the business to champion safety, consistently model desired behaviours, and seek with curiosity employee feedback about processes, risk, and incidents.
- Enhance risk awareness and risk reduction skills across the organisation. Offer continuous learning programs and provide visibility into safety data and analytics to help everyone visualise the change and make better informed decisions. Integrate incident review meetings into your governance structure—invite teams to review incidents including near misses, identify root causes, share feedback, and discuss and act on risk mitigation interventions.
- Embed safety as a core value, not a box to tick. Encourage employees to internalise high safety standards by building their capabilities, recognising and rewarding proactive behaviours, and allowing them to take accountability for their roles. Rather than being seen as a priority that is traded off against production, this will create a more resilient workforce that feels that they have a part to play in meeting the organisation's goals.
A strategic investment in advancing your safety culture will generate returns in sustainable safety improvements, greater trust and loyalty, and operational excellence. dss+ have worked with many food, beverage, and agriculture companies in Australia and New Zealand and globally, to identify gaps, capture opportunities, and position them on a path towards a self-motivated, resilient culture.
Author
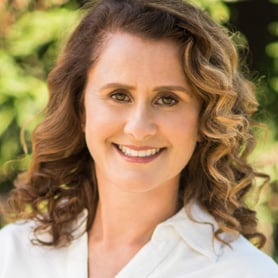
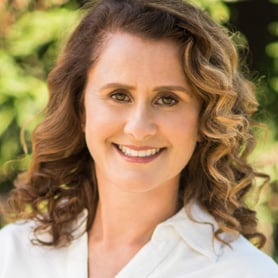