Bolstering steel industry profits
Across the steel industry, production losses caused by inefficiency and poor quality are equally significant, if not greater than losses from downtime. Yet the effects of process and production slowdowns and in-process product defects are rarely quantified and analyzed. To equip steel manufacturers with the skills to recognize these losses and optimize capacity, costs and revenues, dss+ has developed a comprehensive production loss accounting (PLA) program. This approach guides steel producers in allocating, measuring and addressing the full range of potential production losses, driving larger profit margins and significant business value.
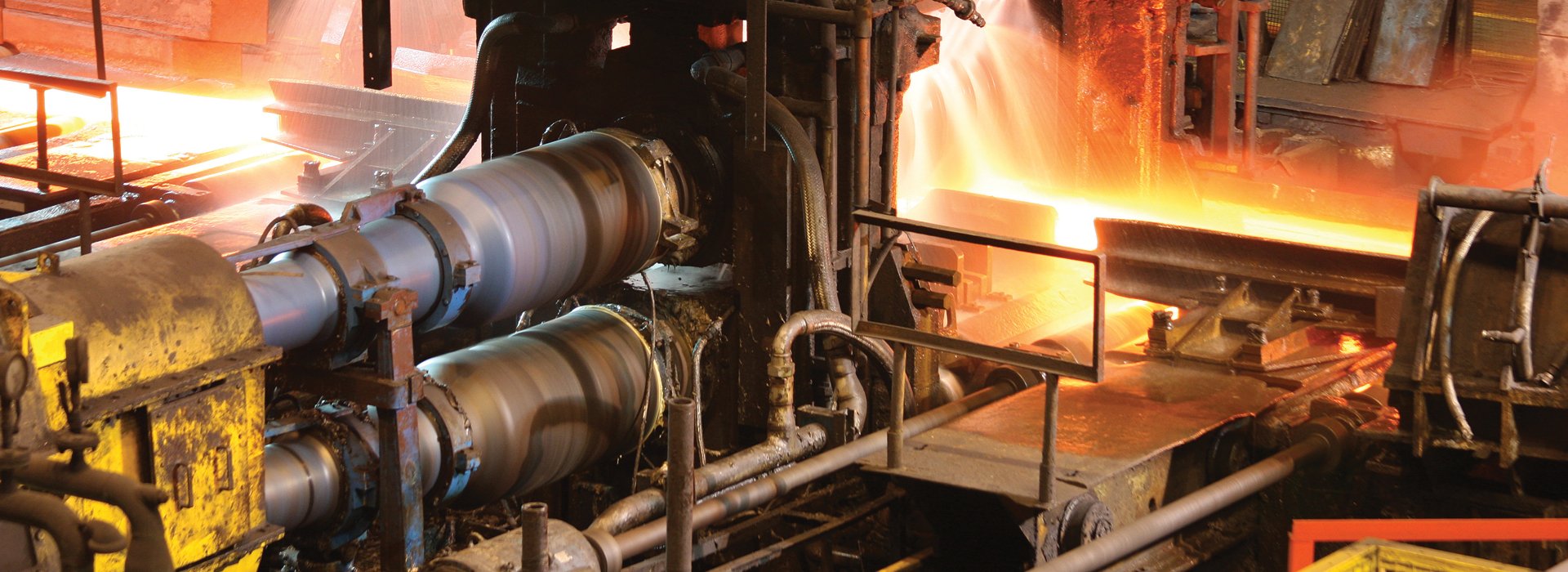
Profit margins in the steel industry are heavily dependent upon input costs and market conditions. New challenges in the market, shifts in value chains and companies' own balance sheets continually arise, spurring manufacturers to identify levers that can mitigate these issues by reining in costs or increasing revenues. Steel manufacturers have a long list of levers to pull on both sides of the cost-revenue equation, from strategic partnerships and new product development to lean manufacturing and strategic sourcing.
As they investigate new opportunities for efficiency, producers may not be able to influence the high fixed costs associated with raw materials or labour, but there is likely to be untapped potential within the roughly 21% of the revenue breakdown, that comes from plant operations. This is where production loss accounting (PLA) presents tremendous opportunity.
In order to increase throughput and revenues, PLA focuses on loss accounting at various stages of production, thereby maximizing capacity utilization and minimizing losses and waste in the system. After all, if a company can increase volume without adding costs above a marginal increase in raw materials, profits will rise. Conversely, if a company is able to recognize and minimize various systemic losses, margins will also rise.
There's no question that today's producers have room to improve throughput and increase production efficiency by decreasing loss and waste. A dss+ analysis of eight leading Indian steel producers' data found that some were utilizing as little as 66% of their available capacity.
PLA brings clarity and action to hidden losses.
Steel manufacturers are accustomed to tracking mechanical and operational availability losses caused by planned overhauls, standby time or line shutdowns. When a furnace is offline, it is immediately reported and the impact measured. However, rate and quality losses—which in many plants can account for nearly double the value of downtime losses—are generally not dynamically tracked. These issues may be addressed in quarterly P&L reports and balance sheets, but not in a manner that allows immediate remedial action.
PLA gives producers the means to track these harder-to-gauge losses at the shift level, as well as identify the most advantageous opportunities for improvement. If equipment is ever operating at a reduced rate—due to idling, minor stoppages, ramp up or even process inefficiencies—lost opportunity is tracked and quantified. Similarly, whenever defects lead to rework or waste, issues are logged for analysis. By allocating losses into appropriate categories and attaching dollar values to the impact, PLA provides visibility into precisely where and how much potential revenue is being lost.
Beyond traditional root cause analysis.
While introducing the PLA concept, dss+ teams have been asked why this approach is necessary, given that steel operations are already applying root cause analysis (RCA), the Five Whys or similar techniques. It's important to note that PLA is not intended to replace, but to supplement and build upon these tools with a comprehensive program based on improvement, not just individual problem-solving.
Analyzing the causes contributing to loss are, in fact, an important part of PLA. However, while most companies apply these tools only to work stoppages, PLA utilizes RCA to determine the source of slowdowns and quality problems. Through PLA, a majority of losses are identified and categorized, providing visibility and minimizing the "if you can't track it, you can't fix it" effect.
Production loss accounting in action.
PLA is based on dynamic, floor-level reporting of any challenges that arise throughout the day. At the close of every shift, field reports and operational issues are logged into the PLA system. A dashboard allows slowdowns and reprocessing to be coded and grouped into predetermined buckets, which compiles production and loss data, then integrates metrics and reports into the management operating system. Root cause analysis is performed, the financial benefit of remediation is calculated, and potential costs and benefits are reviewed against business needs. For any bad actors in which corrective action or preventive measures are deemed appropriate, solutions are developed and actions are logged as modifications proceed. Ongoing impact analysis supported by advanced analytics is carried out to ensure continuous improvement. As PLA progresses and the manufacturer systematically finds and eliminates losses, solutions can be replicated across units, plants, sites and the whole company, enhancing production levels across the organization.Embedding PLA throughout the organization.
Increasing volume in steel manufacturing requires near-universal input and effort. From shift team leaders and shift supervisors to operations engineers and front-line workers, everyone has a role to play.
Production Loss Accounting touches every function, including:
- Operations
- Maintenance
- Reliability
- Production accounting
- Business optimization
- Supply chain and operations planning
dss+ has defined clear change and communication processes to drive alignment and engagement at every level.
This three-phase program begins with leadership buy-in and efforts to "push" the idea through PLA team leaders and area champions. Ultimately, as shift leaders and front-line workers learn to value the process, they amplify the effort by helping to "pull" initiatives through the organization, leading to sustainable benefits.
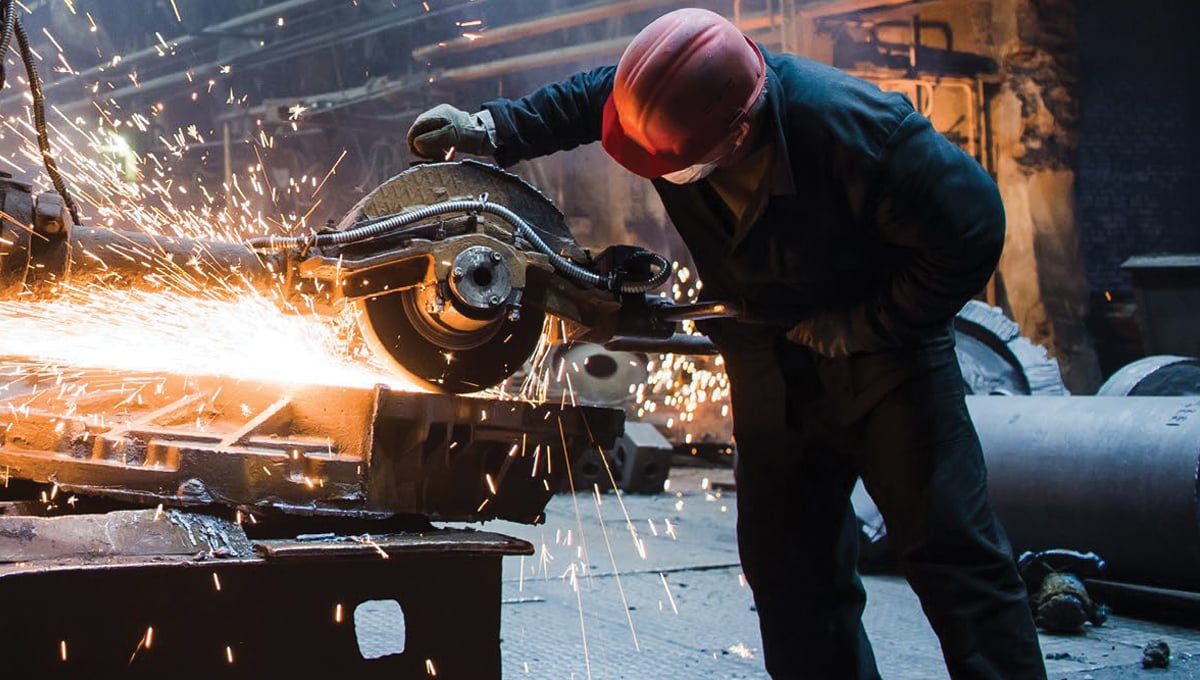
Phase 1: Align Leadership
Create a shared vision of the future.
- Create a vision for change, including fiscal year targets and priority initiatives
- Form a coalition of powerful, top-tier members and align on targets, priorities and executional responsibilities
- Create a roadmap of key milestones and governance processes that integrate priorities with performance management
Phase 2: Mobilize Champions
Create an environment for change.
- Communicate the vision and create excitement among business units and specific functions
- Energize the organization and empower action through change teams charged with distinct initiatives
- Create quick wins by focusing on high-impact efforts
Create and sustain change across the company.
- Build on change by rolling initiatives out across all units
- Make the transformation sustainable by embedding PLA reporting into the organization's management operating system, tracking KPIs, meetings, systems, processes, etc. - for example, by including PLA variances in cascaded reviews
- Train people in how to use PLA to ensure sustainability
Benefits across critical KPIs.
When we look at the wide range of business case levers that can impact value, dss+ clients have seen PLA have a positive impact on many of the components of the value driver tree.
Because a robust PLA program provides actionable visibility into all forms of production loss, this approach helps pinpoint and close the gaps between what steel manufacturers are ideally capable of producing and what is actually being sold. Fine-tuning this important supplyside lever to maximize capacity utilization can significantly improve cash flow and profits—an especially important consideration in times of business or market uncertainty.