Cascade Engineering
Engineering a Path to Workplace Safety Excellence Through Employee Engagement
Cascade Engineering and dss+ utilized several tactics - including employee recognition, incentives and dss+ STOP® programs - to transform culture, develop skills, reduce incidents and ultimately improve operational performance.
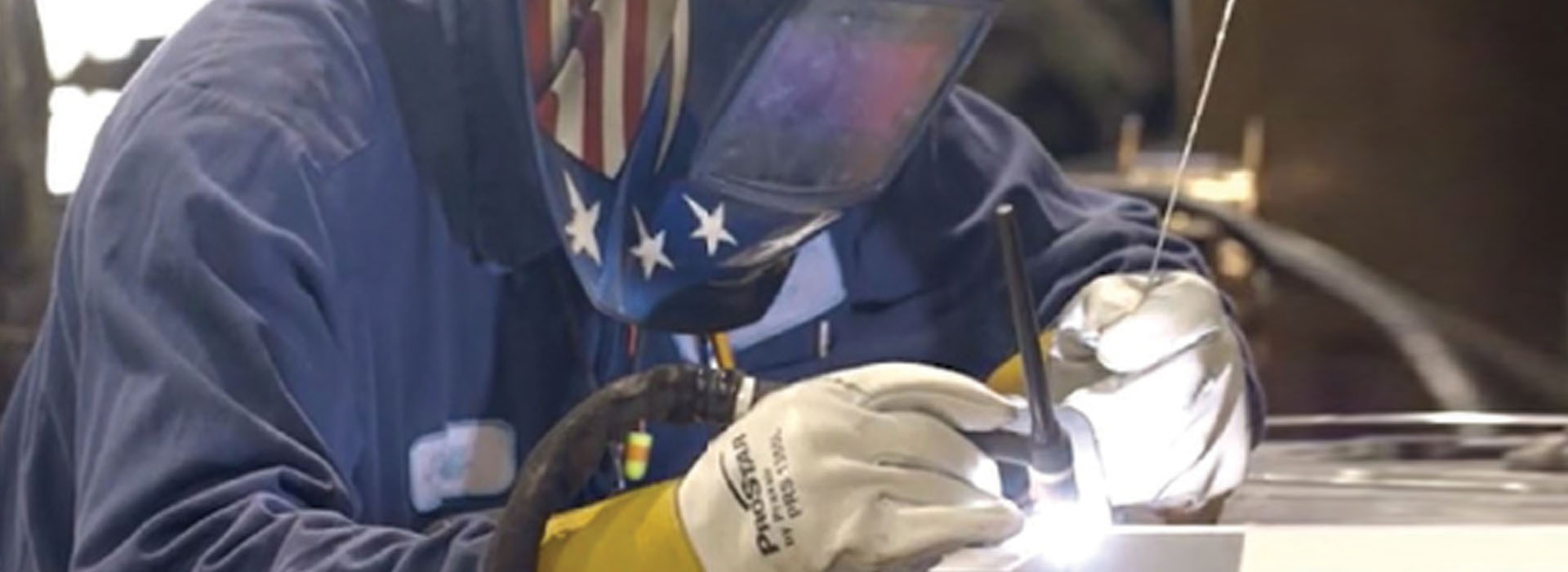
Creating a business with a different mindset
Launched in 1973 as a plastic injection molder with six employees, Cascade Engineering was founded and head quartered in Grand Rapids, MI by Fred Keller. It has blossomed into a diversified global manufacturing company comprised of ten strategic business units serving a wide variety of markets including automotive, commercial truck and bus, solid waste and recycling, furniture and material handling. Today, Cascade supports a product line that includes waste containers, auto parts, office seating, polymer compounding, RFID asset management and large truck components.Cascade Engineering is also a nationally recognized proponent of sustainable business practices that emphasize the key role business can play in building financial, social and ecological capital. With more than 1,700 employees in 14 United States locations with additional operations in Budapest, Hungary, it is one of the largest Certified B Corps in the world.
The company’s technical innovations, sustainability efforts, and programs for employees have earned it multiple awards, including Chrysler’s Technology Role Model Award, the White House’s Ron Brown Award for Corporate Leadership and the National Governors Association’s Distinguished Service Award. Cascade is not what many would consider to be a typical manufacturing company. Since its inception, it has believed that sustainability drives innovation and growth across the three principles that comprise the Triple Bottom Line (TBL) – People, Planet and Profit. The company has worked diligently over the past decade to create a strategy focused on sustainability that propels innovation and sets forth its future direction.
Today this sustainability focus resonates throughout the many facets of the organization. It has become a permanent and palpable part of its culture and drives the strategy for new products and business pursuits. This socially conscious approach to business has endeared Cascade to partners and customers alike, and demonstrates the importance of thinking beyond the bottom line to find success.
A culture where everything, and everyone, matters
Cascade Engineering is also committed to its people by continuously improving safety, morale and learning through employee involvement. Since its beginning, Cascade has operated on the belief that it could be a successful business and be good to its employees at the same time.
That’s one reason why safety is an integral part of the company’s operations. Cascade believes a strong safety program will protect its employees, visitors, clients, suppliers, contractors, company property and the environment. Through its corporate, personal commitment, and active participation, Cascade is committed to achieving the goal of a healthy, injury-free workplace.
According to Sharon Darby, Cascade’s Senior Manager of Environmental, Safety & Sustainability, culture isn’t just one thing—it’s the coming together of everything and everyone at Cascade. “Workplace safety is a core value at Cascade. Being a manufacturing company, we take safety seriously,” Darby shared. “Our founder and Chair, Fred Keller says it best: “No job is so important, no order so urgent, that we cannot take the time to work safely.” Cascade believes every new employee should not only be educated on what the company does, but for what it stands. To achieve this, new associates attend New Employee Orientation, a 16-hour course on achieving cultural expectations, appreciating diversity and working safely.
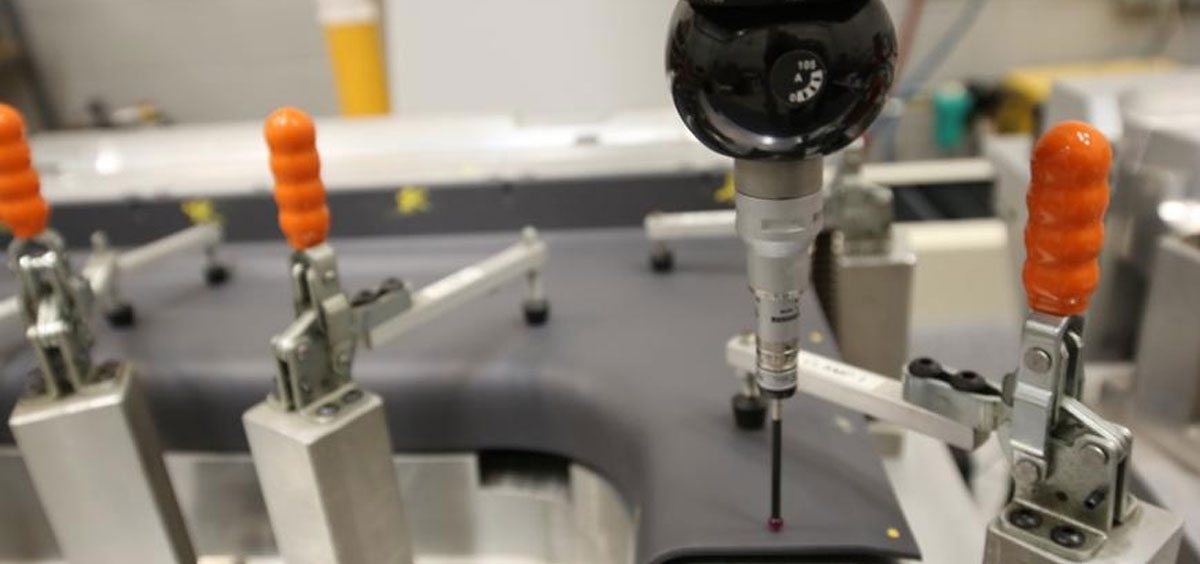
Company Goal: A healthy, injury-free workplace
Recently recognized as one of “The Best and Brightest Companies to Work for in the Nation”, Cascade began several years ago focusing its safety journey on the concept of behavior-based thinking, which emphasizes the prevention of accidents and injuries before they occur. Over the years, Cascade had tackled the challenge to continually reduce injury rates at their facilities by implementing a plan of action which included the following tactics:
- Awareness
- A safety team
- Job hazard assessments
- Safety incentives
- Accident investigation
- Case Management
- Effective communication
- Wellness and safety programs
Cascade repeatedly came in below the national recordable incident rate average of 4.4% and strove to decrease this rate year over year. Even though its incident rate was well below the industry average, top management set aggressive reduction goals and accountability was tracked through monthly reporting on progress.
Cascade realized a more structured program would yield better results as it set a new goal of Zero Injuries in 2013. Cascade turned to dss⁺ to implement several award- winning dss⁺ STOP® training programs to give employees the knowledge and skills to transform their safety culture.
Cascade Engineering compared to National Average
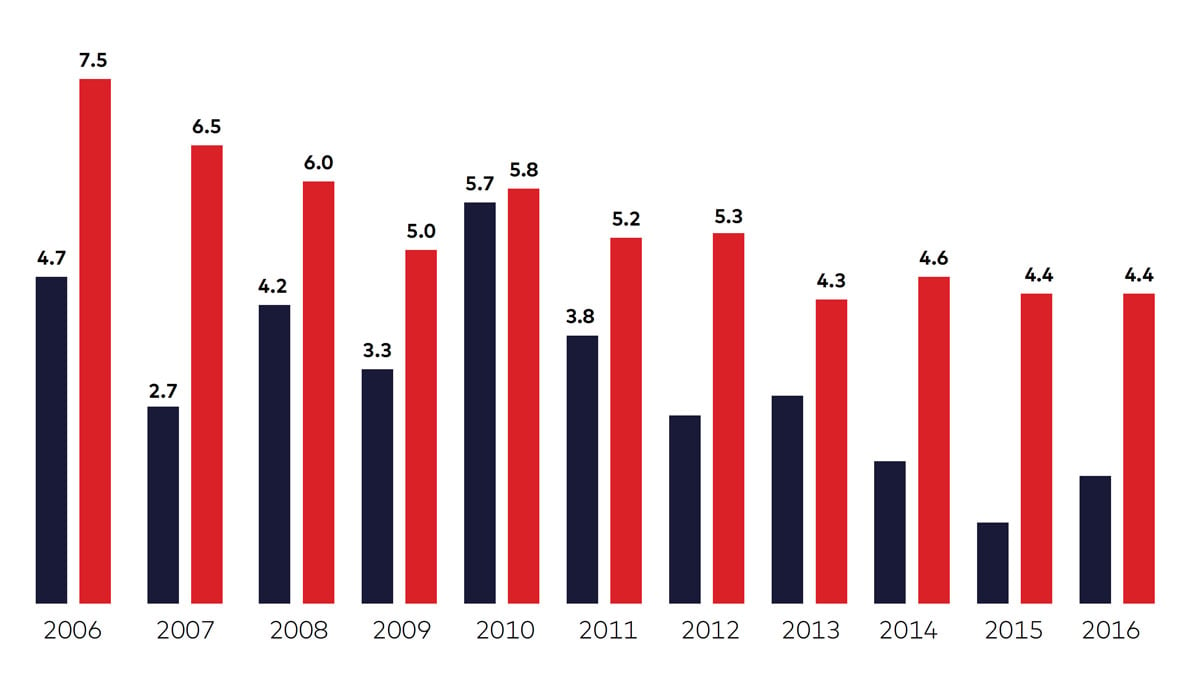
The initial phase of dss⁺ involvement with Cascade included training those who would be training company management through the STOP® for Supervision program. In the first year, 90 leaders were trained. The second-year goal was to train over 500 employees through STOP® For Each Other.
Cascade also used the dss⁺ Safety Perception Survey™ to help uncover employee perception gaps, understand the strength of the organizational culture and benchmark results against companies in its industry. Results indicated that the company is evolving from an independent to a more interdependent culture which is critical to not only attaining but maintaining an injury-free workplace.
Rewarding result in further injury reduction
STOP® for Each Other is based on the idea that safety is everyone’s responsibility. dss⁺ designed the program to help participants look at safety in a new way, so they can help themselves and their co-workers work safely.
As Sharon Darby has observed, the program has helped Cascade employees develop their safety awareness and comfort level to enable them to talk with others about all aspects of safety. The STOP® for Each Other job-focused observation and application activities make safety real, not theoretical. As a result, Cascade participants have gained better understanding of safety concepts and skills, with wider application and use of the knowledge learned, including holding one another accountable.
Job hazard assessments and safety observations are just two of the techniques Cascade has used to evaluate working conditions for potential improvements. Another benefit of using STOP® for Each Other is that it is helping foster a culture of caring and concern that focuses on prevention, working safely, and communication, which is aligned with Cascade’s objectives for its workplace safety program.
According to Darby, Cascade has seen a reduction in its significant injury rate from 3.4 to 3.01. She shared, “In Grand Rapids alone the rate decreased to 1.5, while our Ohio location saw a decrease to 2.97. And in 2017, only 10 injuries and 0 lost days were reported. This year, at mid-point only 2 injuries have been recorded.
In addition, near misses are tapering off due to the practice of observations versus merely filling out near miss reports. Employees are becoming more aware and talking more with one another about how more safely they can work.
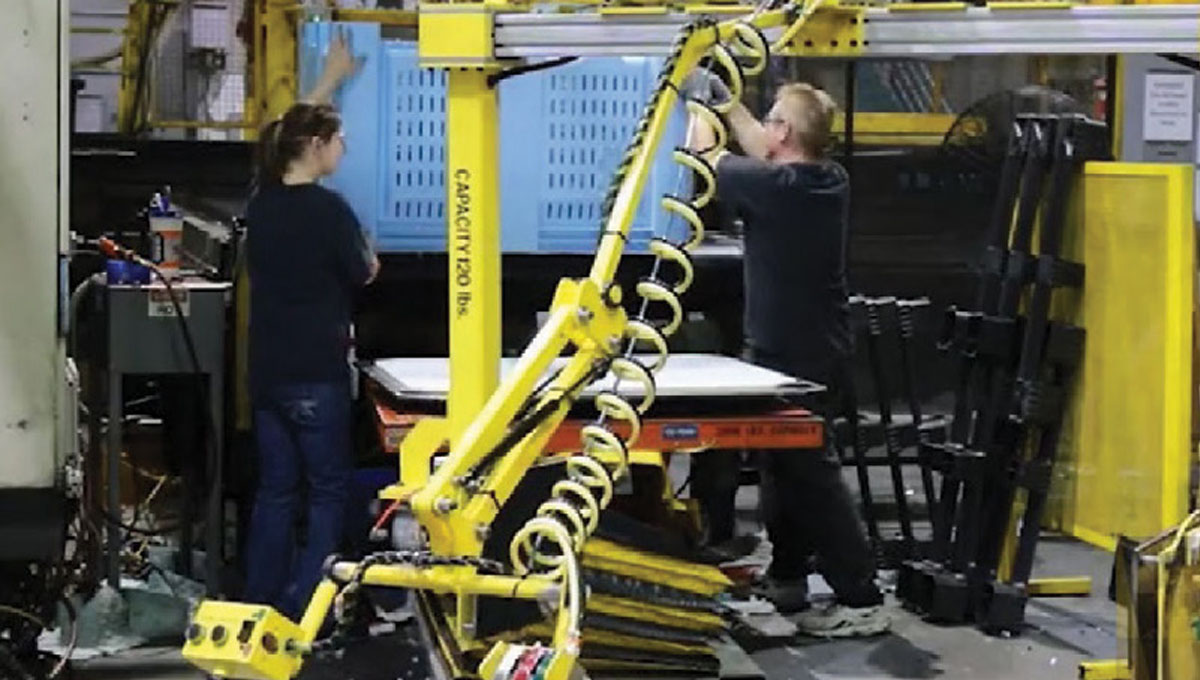
Keeping employees engaged for accountability
One of the keys to the success of the workplace safety program at Cascade is not just the increase of one-to-one interactions and conversations, but proactive and focused corporate communication efforts. Posters, meetings, intranet-based information, contests, and training sessions continually keep the objectives in front of employees.
Safety incentives are another innovative way Cascade has encouraged employee participation. Safety training for off-site sales staff includes classes available on the corporate website, the completion of which is tied to bonus structures. The safety activities, rewards and recognition, cook outs and bonus plans are just a few of the programs Cascade uses to motivate employees. Incentives have also been used to help reward trainers for their commitment and to provide added recognition.
According to Sharon Darby, “dss⁺ offers us great resources in terms of the training and materials. They provide us with the materials and a structured program that helps our employees feel comfortable learning new ways to work more safely. We needed the outside expertise of dss⁺ to help this happen... to achieve our goal of further injury reduction.”
Darby adds, “We are incorporating our learnings and results into everyday operations...which means it is here to stay. Continuous improvement is a way of life for us at Cascade.”
Cascade Engineering is known for handling the tough projects – like reducing injury – with innovation, operational excellence and by creating an enterprise where employees know they are valued as individuals and because they do valuable work. Working with dss⁺, Cascade is transforming culture, developing skills, reducing incidents and ultimately improving operational performance.
As Sharon Darby shared, “We’re seeing really good observations. And we review our observations now with the STOP® DataPro® tool... in fact, we’ve added a highlight of an observation each month as another training tool to increase awareness. People are really holding one another accountable. It works!”
Nothing is more important than helping your employees come home safe
dss⁺ can help your organization reduce risk and build a sustainable, effective safety culture. For 50 years, we have been advising leading industrial companies around the world on operations improvements and workplace safety. The independent research company.