Circular economy in mining
In 2024, dss+ explored the game-changing potential of Circular Economy (CE) principles in the mining sector. The focus? Revolutionising sustainability and resource efficiency through innovative practices like recycling, urban mining, and alternative fuels.
At the core of this transformation is collaboration—across industries, across value chains. By extending the lifecycle of materials and integrating cutting-edge technologies, the mining industry can not only reduce its environmental impact but also pave the way for a cleaner, more resilient future.
The road ahead is clear: embracing circularity is the key to reshaping the future of mining. But real change requires action. The question now is: how will we drive this evolution?
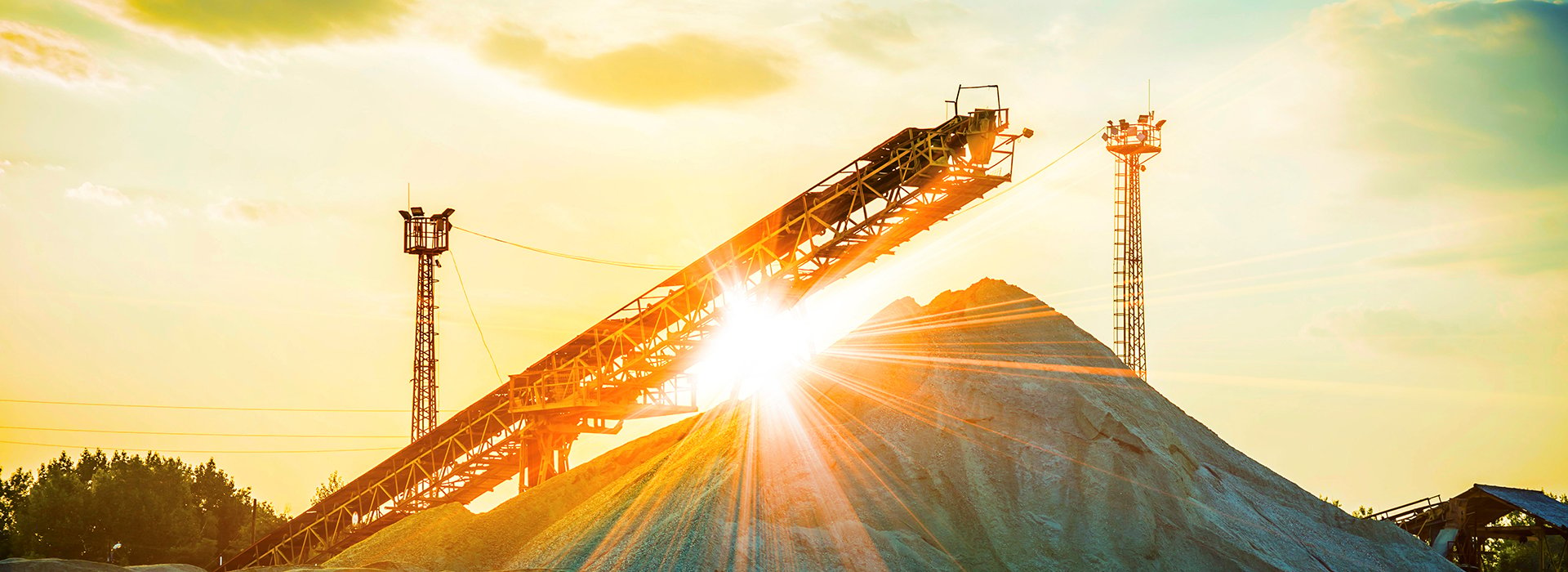
Unearthing the Circular Approach to Mining:
Reimagining Learning and Innovation Across Industries
Circularity represents a meaningful direction for the future of mining, offering innovative ways to enhance sustainability and resource efficiency. In 2024, dss+ engaged with thought leaders and industry practitioners to explore how adopting Circular Economy (CE) principles can revolutionise the mining and metals sector. Our mission was to uncover how companies are embedding responsible extraction, reuse technologies, and sustainable practices throughout their operations and value chains.
As we discovered, achieving real impact requires cross-industry collaboration. The integration of sustainable principles, along with mixed energy solutions such as alternative fuels and digital innovations, is key to reducing carbon emissions and ensuring a cleaner future for mining. This vision was brought to life during a thought-provoking panel discussion moderated by dss+, where experts from leading organisations like Anglo American, Extreme E, Antofagasta, and Fortescue Zero shared their insights on the role of CE in fostering a sustainable and resilient industry.
At the heart of this transformation is the need for collaboration and innovation - across sectors and throughout the value chain. From extending the life cycle of materials through recycling to embracing new technologies like urban mining, the opportunities to reduce environmental impact are vast. But this shift won’t happen overnight. It requires a united approach, innovative strategies, and a commitment to change. The question now is how we can leverage the circular economy to reshape the mining industry and build a sustainable future.
Circular economy and the mining sector
The global transition to clean energy is set to have profound and lasting impacts on the demand for minerals, metals, and rare earth elements over the next two decades. Renewable energy technologies, such as solar photovoltaic (PV) systems, wind farms, and electric vehicles (EVs), require significantly more minerals than their fossil fuel-based counterparts. This shift will inevitably drive a substantial increase in the need for mining and extraction, highlighting both challenges and opportunities for the sector. According to the International Energy Agency (IEA), between 2017 and 2022, demand from the energy sector was the primary driver behind a threefold increase in overall demand for lithium, a 70% surge in cobalt demand, and a 40% rise in nickel demand. This rapid growth trajectory is expected to persist. In fact, for cobalt and lithium, existing mines will only be able to produce half the required amount by 2030, while copper production capacity is expected to meet around 80% of future demand. Mineral demand for clean energy technologies could rise by at least four times by 2040 to meet climate goals, with particularly high growth for EV-related minerals. Mining companies engaged in the extraction and processing of these commodities must urgently expand their capacity to facilitate the future generation, transmission, and storage of renewable energy. To address the rising demand, companies must substantially expand exploration efforts across diverse geographical regions while simultaneously enhancing the efficiency of their existing assets.
Mining companies, such as Antofagasta and Anglo American, are already exploring responsible extraction methods, waste repurposing, and adopting closed-loop systems to ensure minimal resource loss. This evolution includes a deeper integration of recycling, upcycling, and the repurposing of materials, such as using waste rock for construction or repurposing on-site equipment. The broader aim is to create a circular supply chain that reduces reliance on virgin materials while reducing carbon emissions and conserving resources.
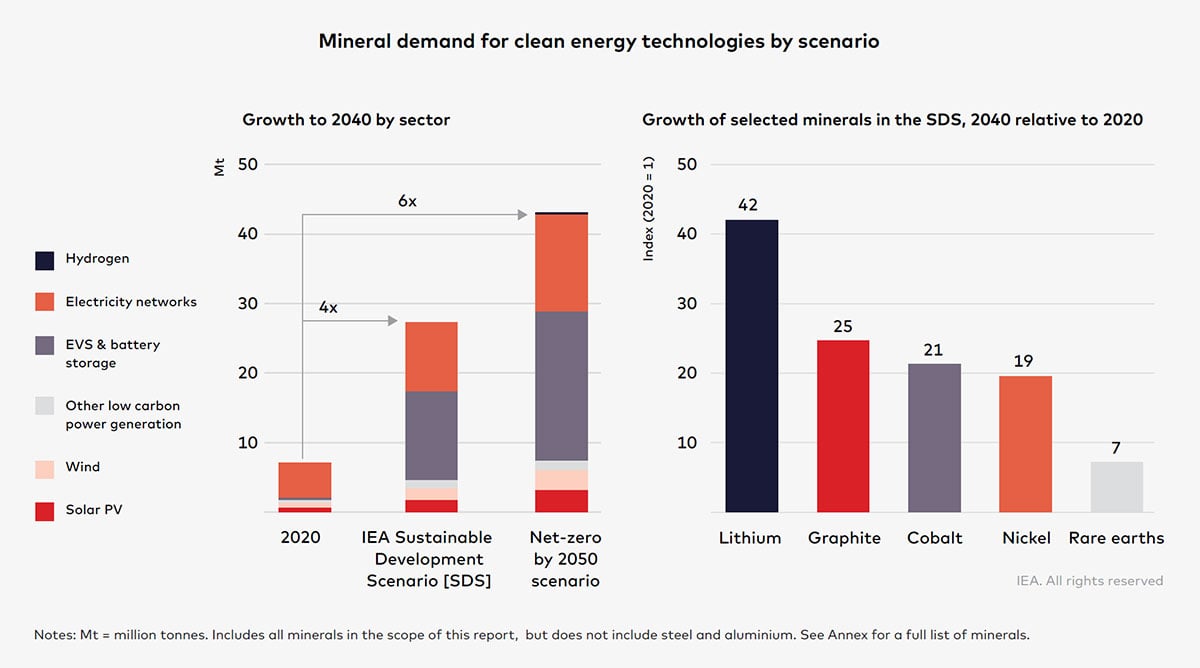
1.
The surge in mineral demand: a growing challenge for the industry
As the world transitions to cleaner energy, the demand for minerals is set to escalate dramatically. Renewable energy technologies, such as solar and wind, require significantly more materials than traditional fossil fuel systems. In parallel, the electrification of transport, driven by the growth of electric vehicles (EVs), will increase demand for critical materials such as lithium, cobalt, and nickel. By 2040, the demand for these minerals is expected to multiply, with some elements, including nickel and cobalt, potentially experiencing a 20-fold increase.
The International Energy Agency (IEA) suggests that to achieve the climate stabilisation goals outlined in the Paris Agreement, mineral requirements for clean energy technologies could quadruple by 2040. This means that EVs and battery storage are expected to become the largest consumers of lithium and nickel, significantly outpacing other traditional uses such as stainless steel.1

1. ICMM, Tools for Circularity, October 2024
2.
Circularity and recycling: key to a sustainable future
Circular economy (CE) principles are critical to ensuring a sustainable mining ecosystem. By prioritising resource optimisation, reprocessing waste materials, and implementing closed-loop systems, mining companies can reduce environmental impact while improving operational efficiency. The mining industry acknowledges the need to embrace circular practices like repurposing waste rock, reusing materials and equipment on-site, and extending the lifecycle of critical materials through recycling.
The IEA has noted that scaling up recycling could reduce new mining capacity needs by 25-40% for critical minerals by 2050, with copper and cobalt being prime candidates for this approach. Specifically, recycling for copper and cobalt could reduce new mining requirements by up to 40%, while lithium and nickel recycling could decrease new mining needs by 25%.2 However, recycling alone will not be sufficient to meet the rising demand for critical materials, making primary extraction still necessary in parallel.
There is a clear need to increase volumes of primary extracted metals and ensuring increased circularity of materials keeping them retained in the system for as long as possible. It is estimated that to meet the supply gap, more than 300 new mines may be required to build a suitable stock of materials for the energy transition.3
“Scaling up recycling could reduce new mining capacity needs by 25-40% for critical minerals by 2050.” IEA”
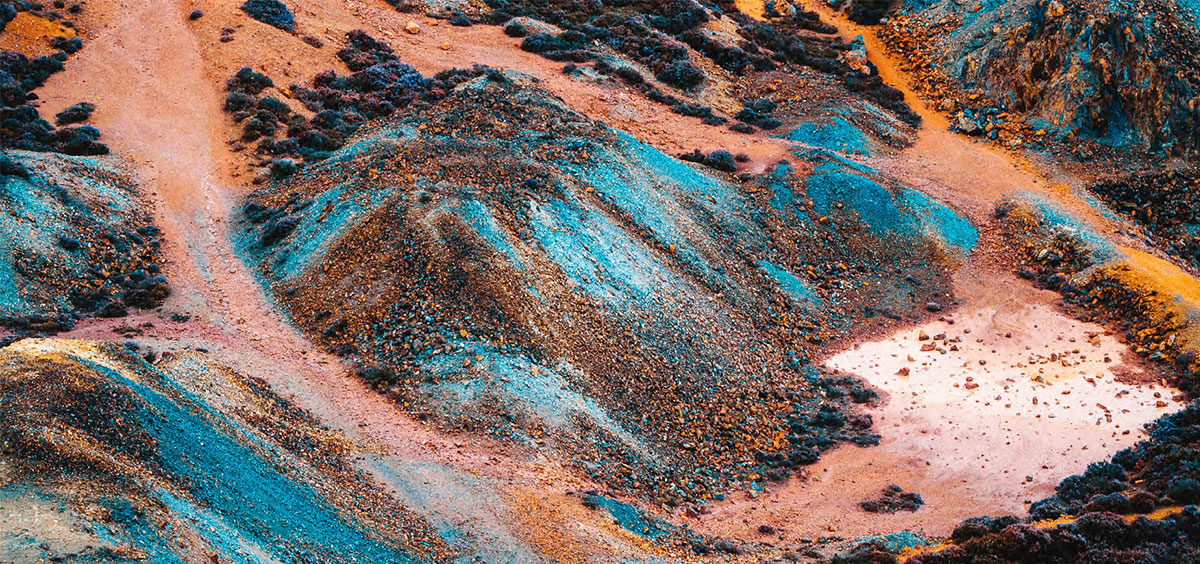
2. The Role of Critical Minerals in Clean Energy Transitions, IEA, 2021 (revised march 2022).
3. Benchmark Source, 2022, More than 300 new mines required to meet battery demand by 2035
3.
Hydrogen technology: paving the way for decarbonisation
Hydrogen technology emerged as a pivotal topic, particularly in the context of decarbonising mining operations. Hydrogen has the potential to replace fossil fuels like diesel in mining machinery, significantly reducing carbon emissions and contributing to a greener mining process.
Drawing from innovations in motorsport, where hydrogen technology has been tested and refined, mining companies are now exploring similar applications. For example, Anglo American trialled a hydrogen-powered mine haulage truck at its Mogalakwena platinum group metals mine in South Africa. This marks a significant step forward in reducing the carbon footprint of mining operations. Additionally, the upcoming launch of Extreme H, the world’s first hydrogen-powered racing series, in 2025 further highlights the scalability of this technology and its potential benefits for the mining industry.
“Hydrogen has the potential to replace fossil fuels like diesel in mining machinery, significantly reducing carbon emissions and contributing to a greener mining process.”
4.
Collaboration across sectors: a cornerstone of innovation
Collaboration across sectors is key to advancing the circular economy. The mining, technology, and manufacturing sectors must collaborate to develop innovative solutions that reduce waste, optimise resource use, and extend the lifecycle of critical materials. The experience of McLaren and Extreme E in developing high-performance technologies in motorsport provides valuable insights into how innovation can fuel sustainability across industries.
Such collaborations are key to scaling up the development and deployment of technologies that can optimise resource efficiency, minimise waste, and enhance the sustainability of mining operations. The synergies between these sectors can lead to breakthrough solutions that meet both environmental and economic goals.
5.
Geopolitical and security implications: ensuring material supply
The growing demand for critical minerals also brings with it increasing geopolitical challenges. As countries accelerate their efforts to reduce emissions, they must ensure secure and uninterrupted access to minerals such as lithium, cobalt, and nickel. The European Union, for instance, requires stable access to critical raw materials to meet its ambitious green transition and digitalisation targets. Governments and companies must ensure resilient supply chains to secure access to these vital minerals, while balancing the need for sustainability with geopolitical considerations. This highlights the strategic importance of material security in the context of the global energy transition.
“It is estimated that by 2030, recycling could only meet less than 10% of the demand for the energy transition.”
6.
Recycling: a vital but limited solution
While recycling plays a crucial role in addressing the demand for critical materials, it cannot fully meet the growing needs of the energy transition. Despite advances in recycling technologies, the current recycling rates for materials such as cobalt, lithium, and graphite remain low. As the IEA highlights, scaling up recycling will be essential but is unlikely to meet the total demand. It is estimated by the Energy Transitions Commission that by 2030, recycling could only meet less than 10% of the demand for the energy transition.4 This is due to the fact that existing end-of-life recycling rates are currently low and will take a number of years to increase. Furthermore, secondary supply can only be scaled up as clean energy products reach their end of life and materials such as lithium and copper may not become available for decades. Therefore, the mining sector must continue to focus on primary extraction, alongside efforts to enhance recycling systems and processes.
7.
Mining’s shift from linear to circular
Transitioning to a circular mining model requires a fundamental rethinking of industry practices. The mining sector must innovate to reduce waste and maximise the reuse of materials. While some elements of circularity have been present in mining for decades, there is now an urgent need to scale these practices across the sector. Achieving this will require close collaboration within the mining industry and with external stakeholders to make circularity the standard operating model. This shift also includes addressing how mining companies manage waste, optimise resource use, and ensure that extraction processes are as sustainable and efficient as possible. A circular economy approach will enable the sector to meet the rising demand for minerals while minimising environmental impacts.
4. Energy Transitions Commission, 2023, Material and Resource Requirements for the Energy Transition.
5. The Intelligent Miner
Embracing a Circular Economy in the Mining Industry
Embracing a circular economy in the mining industry is no longer just a forward-thinking sustainability initiative; it has become a crucial driver of competitive advantage and long-term viability. As mineral demand surges and geopolitical and security concerns around material supply intensify, the industry faces increasing pressure to adopt practices that enhance resource efficiency and ensure sustainability.
By focusing on circularity and recycling as key strategies, mining companies can tackle growing resource challenges while paving the way for decarbonisation through innovative solutions such as hydrogen technology. These approaches not only address environmental concerns but also open pathways to improved operational efficiencies, reduced waste, and long-term cost savings. However, recycling alone is not sufficient - companies must transition from linear processes to a circular approach, incorporating sustainability principles throughout their operations.
The dss+ circular economy (CE) framework offers an integrated, strategic approach tailored to the unique challenges of the mining sector. By fostering collaboration across sectors - uniting industry leaders, governments, and communities - this framework promotes the adoption of innovative practices and strengthens the industry’s ability to meet rising demands. At its core, the framework enables mining organisations to establish robust governance models that drive continuous improvement and position them as leaders in environmental stewardship.
As the mining industry undergoes a profound transformation, companies must align with circular economy principles to navigate the growing complexities of the resourceconscious global economy. With the right strategies in place, the sector can ensure its long-term survival by turning challenges into opportunities, creating a more sustainable and profitable future while meeting the world’s demand for critical minerals.
Industry leads
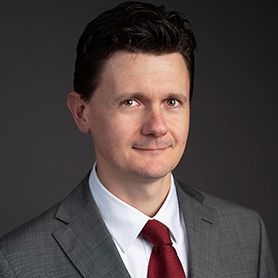
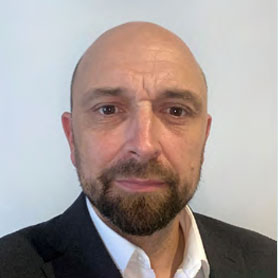
Robert Mell
Senior Manager - Sustainability and Business Transformation, dss+
