Doris Horvath: Creating an open and engaging safety culture
With a wealth of safety management experience, Doris Horvath is passionate about managers investing time in face-to-face safety management to create an open and engaging safety culture.
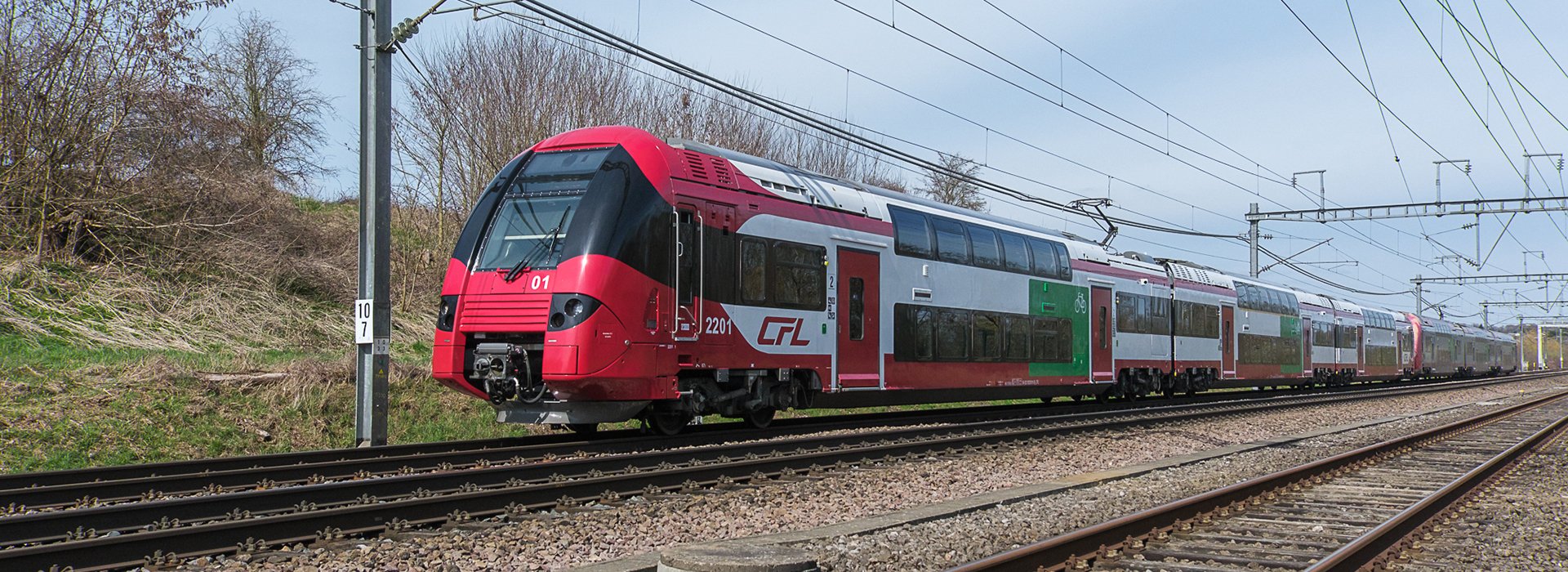
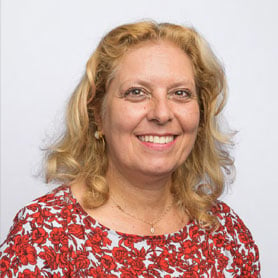
Doris Horvath
Head of the Safety, Security and Environment, Luxembourg National Railway Company, CFL
Q.
How did your journey in safety begin, and how has your interest in safety influenced your career choices?
After studying chemistry at university, I worked as a scientific advisor at the EU Parliament, where I evaluated and pursued scientific projects in the environmental sector. I remember a worker from Chernobyl gave a testimony about his radiation damage. This really moved me; it angered me that someone could be irreversibly harmed by their working environment. I wanted to move away from research and joined a small consulting office which offered expertise in the areas of safety and environment. I was becoming increasingly interested in safety and at the time, companies were more willing to improve safety than to invest in environmental protection. I then joined a larger safety company in Luxembourg that offered advice in the areas of safety and the environment as well as compliance testing. During this time, I completed additional safety training with the German safety inspector TÜV Rhineland in Cologne. I also gained a lot of experience as an approved quality and environmental auditor. This gave exposure to many different companies across a variety of sectors and developed my passion for the safety sector. In 2001 I joined Luxembourg Railways where I now lead a network of around 40 safety experts, reinforcing a safety culture to avoid work and industrial accidents on the railway network. I’m a very curious person and think my scientific background helps me daily to structure my work.
“As managers, we create a rule, explain it, and then assume workers will implement it. This is theory and is not enough.”
– Doris Horvath, Head of the Safety, Security and Environment, Luxembourg National Railway Company, CFL
Q.
You mentioned reinforcing company culture, what does good leadership look like and how does it help when creating safety in the workplace?
Good leadership is key to changing mindsets and behaviours, but this requires the support and willingness of senior management to prioritise safety. When it comes to the implementation onsite, I think this is only possible if employees understand why they must carry out the work in a certain way. As managers, we create a rule, explain it, and then assume workers will implement it. This is theory and is not enough, especially when carrying out the work, as unforeseen difficulties often arise that we as managers have not always adequately planned for. This means employees onsite sometimes have to make difficult decisions about whether they can carry out the work without risking their own safety and that of their colleagues and customers. When you give employees attention and support, employees will show their commitment to safety. By being present you can feel the safety culture that’s in place, see if every employee works as specified and if every employee wears the same personal protective clothing for the same work, is the workplace secure, clean, and tidy? You can see that onsite and if you have been able as a manager to create in your teams a respectful atmosphere of trust, then the employees will also communicate unsafe conditions and actions. Then as a manager and good leader, you must engage yourself to fix these unsafe working conditions.
Q.
What impact have disruptive events over the last few years had on the way you manage safety and the overall wellbeing of employees?
Safety culture is highly influenced by external circumstances. Life has become more difficult and complicated, highlighted by the pandemic, wars, and terrorist attacks. I think that people recognise that life can change very quickly, especially when lives and safety are at daily risk. As a manager, it is therefore important to remember that employees have a lot of worries and that their thoughts are not always focused on the job. This leads to a lack of concentration and an increased risk of accidents. As a manager, you have to be more responsive to your employees in these uncertain times and being physically present is a way to gauge and assess the impact of individual concerns. I think it’s important for managers and colleagues to recognise the psychological state of their employee or colleague, and developing the soft skills of managers is key to this.
“I think it’s important for managers and colleagues to recognise the psychological state of their employee or colleague, and developing the soft skills of managers is key to this.”
– Doris Horvath, Head of the Safety, Security and Environment, Luxembourg National Railway Company, CFL
Q.
In what ways do innovation and technological advancements affect the day-to-day management of safety and training? What role does communication play?
It’s important to be innovative to remain competitive, increase efficiency and to attract young talent, but when it comes to safety we must constantly adapt to innovations as innovations ultimately change our activities. It is therefore important to reassess risks when introducing new technologies. It involves risks that potentially we cannot see from the outside and we have to increasingly support our employees and be open to their criticisms and demands. Therefore, communication between employees is important when we introduce a new technology, because they can tell us where there about hidden risks. Managers may think the process will be simplified, but that may not be the case for the employees faced with the new technology. As well as accompanying and listening, we need to benchmark the risks, this may involve collaboration – asking who else has implemented this technology, what was their experience?
Q.
How do you see other practice areas, such as sustainability and operational excellence help to create a safer business that is resilient and better positioned to withstand industry volatility?
There’s no doubt that the railway industry has a huge opportunity to have an impact on environmental sustainability by reducing carbon emissions. Operational excellence, risk management and safety all need to be sustainable. When it comes to the physical environmental factors, safety and the environment are firmly linked together and businesses that have successfully implemented safety can utilise the framework and transferable skills to manage sustainability. It’s a journey focused on analysing, understanding, and taking people with you - it’s the same principles, but the theme is different. A sustainable model for safety needs to be inherent within businesses and includes the ability of colleagues to look out for each other and demonstrate safe practices, or alternatively speak up when something isn’t safe, that way you create a continuous safety culture.
“A sustainable model for safety needs to be inherent within businesses and includes the ability of colleagues to look out for each other and demonstrate safe practices.”
–Doris Horvath, Head of the Safety, Security and Environment, Luxembourg National Railway Company, CFL
Q.
Based on your own experience, what would you say are the top three best practices when building a safety programme in your industry?
I know I have said this before, but I truly believe it is so important for managers to be physically present, to go onsite, see how work is being carried out, listen to the workers and the difficulties they are facing. Is it scalable? It simply has to be, and managers must buy into this and manage their time accordingly. It’s easy to say ‘I don’t have the time’ or ‘I’m too busy’ - but managers need to prioritise and invest time so that they can be present. It takes discipline to respect time, but what’s more important - doing admin or helping your colleagues to stay safe. Yes, it’s a big investment of time but the return is high. Secondly, it’s important to engage with safety by taking steps to make things happen. Sometimes there’s no quick fixes, things like budget approval or further analysis can take time but communicate the process and show engagement. Alternatively, this may also involve being visibly proactive and visibly removing a hazard yourself whilst onsite - just do it! And finally, never give up and always remember that it is worth working for safety and health - the employees need the support, and they give it back with respect and commitment to their work and the company.