Why do fatal accidents still occur in the chemicals industry?
In Europe, the chemicals industry has a low average lost time injury frequency rate (LTIFR) compared with other manufacturing sector industries. However, the industry still records fatal accidents, and companies remain vulnerable to fatal incidents worldwide, despite the maturity of the industry. A catastrophic event involving fatalities can change the lives of families, colleagues, companies and whole communities from one moment to the next. Learning from the causes of these incidents in the chemicals sector in Europe, the industry can start to reckon with its Fatal Accident Rate and address challenges head-on.
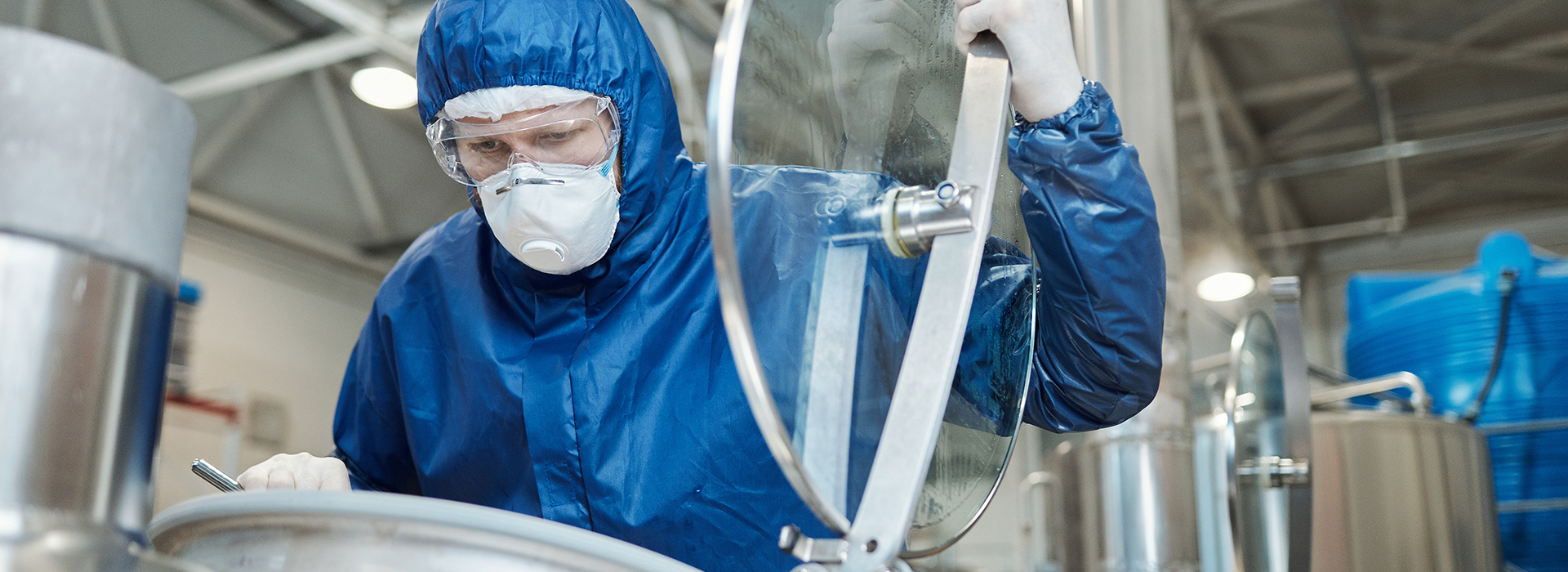
A catastrophic event involving fatalities can change the lives of families, colleagues, companies and whole communities from one moment to the next. From a business perspective, such a failure can also have immense costs and long-term implications for site operation, supply chains and reputation.
In Europe, the chemicals industry has a low average lost time injury frequency rate (LTIFR) compared with other manufacturing sector industries. However, the industry still records fatal accidents, and companies remain vulnerable to fatal incidents worldwide, despite the maturity of the industry. No company is immune to potential severe incidents.
The chemical industry has had to deal with numerous challenges and dynamic factors in recent years, including supply chain bottlenecks, higher energy prices, access to skilled personnel and the departure of experienced specialists and managers due to demographic change and company mergers. In this environment, the industry needs to reckon with its Fatal Accident Rate and address challenges head-on.
The state of the chemicals industry in Europe
The chemicals industry is mature with decades of experience and is a key contributor to the global economy. After China, the European Union (EU 27) chemicals industry ranked second in total sales, reaching the value of € 594 billion .
In addition, the EU chemicals industry represents ~7.5% of EU manufacturing turnover, one of the largest manufacturing sectors in Europe, supplying almost all sectors of the economy including industrial sectors like rubber & plastics, textiles, construction, computer production, pulp & paper and other branches of the economy such as health and social work, agriculture, and services. Due to its involvement in so many up- and downstream sectors, the actions taken within the sector have wide-reaching consequences.
And these consequences are clear. From 2016 – 2021, 44 fatal incidents in the European chemicals industry occurred, with 10 of these having multiple fatalities, and a total of 205 people were injured . Some events resulted in severe community damages like school closures, or the necessity for communities to drink bottled water. This is before considering the immense costs of such incidents, which can exceed € 800 M for a single incident, and can have long term reputational damages to companies, closing work facilities and causing job losses.
From 2015 to 2022, dss+ observed a series of common factors across more than 450 consulting engagements in the chemicals industry. The engagements included an assessment of relative cultural strength (RCS) measured against the dss+ Bradley Curve™. The dss+ Bradley Curve™ purports that as companies mature their safety culture, they move from reactive culture based on compliance to an interdependent culture, in which all stakeholders see themselves as key to both maintaining and encouraging a strong safety culture.
One of the key reasons that the chemicals industry in Europe could still be struggling in its prevention of fatalities is the common trend of a relatively complacent safety culture observed throughout the sector.
The results of the relative cultural strength of clients surveyed in the dss⁺ Safety Perception Survey ™ showed a median result (figure 1) in Europe, Middle East and Africa firmly in the range of a “dependent culture”, which is a culture of supervisor control. In general, the chemicals industry in Europe scored lower in comparison to other regions, who were rated within the “independent culture” range, embodying personal knowledge and commitment.
This trend is consistent with publicly available data on the frequency of lost-time accidents in the chemical industry.
Possible factors influencing safety performance in Europe
There are several factors that could explain why the chemicals industry in Europe still finds itself vulnerable to fatal incidents. Whilst there is certainly no single cause, there are a few commonalities in the European market that could be influencing this trend.
Firstly, the economic environment within Europe has recently had several challenges, resulting in the tightening of budgets, downsizing or acquisitions and divestitures to re-align business portfolios. Because safety is often considered a “cost”, firms can mistakenly cut corners when implementing safety initiatives whilst these transitions occur. As such, mergers and acquisitions can result in workplace cultures that are cobbled together and vulnerable to reactive or uncoordinated approaches to safety.
Secondly, the practical makeup of the workforce is one that can also stagnate safety culture. In Europe, in highly specialised technical industries such as chemicals, the workforce in middle management are highly educated individuals, often with master’s degrees or even doctorates. Whilst this ensures a great depth of technical knowledge at a managerial level, it can lead to a level of complacency towards safety incidents – a “won’t happen to us” mindset, and an undervaluing of rigour and routine on the shopfloor.
The complacency toward safety in Europe is highlighted in contrast to Asia, where the workforce in technical plants tend to do vocational, on-the-job training. Here, the workforce appears much more engaged and aware of typical safety concerns . This could indicate that practical, on-the-job learning can lead to more engaged safety cultures.
Finally, the phenomenon of an ageing workforce in Europe could be an influence for safety culture complacency that is related to, but distinct from, the skillset of the workforce. By 2050, Europe is likely to have at least 25% of its population over 65. For technical positions in industries like chemicals, it’s predicted that a large percentage of the workforce will leave over the next 5 years. Despite this, there is a lack of legacy planning and knowledge sharing that can result in a lost awareness around safety issues. In other spheres, such as digitisation, senior leaders can actively stifle progression through their unwillingness to act as coaches and training partners to younger members of staff.
SUCCESS CASE STUDY In 2019, DuBay Polymer GmbH in Germany challenged themselves by raising the question "how do we maintain risk awareness when safety performance is first-rate?" DuBay conducted a Risk Perception Survey to measure the attitude to risk by area, function, and tenure with the company. Based on the results, they implemented a programme for all employees and supervisors to help employees to decode their decision-making processes and trigger a change in awareness, thus helping them to reduce risky decisions and improve safety. Subsequently, these insights have been successfully integrated into safety routines such as audits, incident investigations and last-minute risk assessments, improving the overall safety management of the company. |
dss+ has identified common indicators of firms stuck in a “dependent” safety culture. These commonalities include:
- Risk evaluation: Risk is typically evaluated by experts with limited discussion and engagement across all roles and functions.
- Risk focus: Focus is placed on high frequency and low consequence situations such as typical workplace safety incidents, as opposed to process safety related incidents which are more likely of low frequency, but high consequence.
- Compliance oversubscription: A company’s High level of trust in compliance is good and a documented management system and standards are considered a guarantee for success. However, dss+ experience shows that a robust management system only exists when the defined standards are embodied by employees and managers and here there is often a gap.
- Institutional memory: Contractors have been found among the most knowledgeable employees as carve outs and ownership changes have led to enterprise know-how being outsourced and reduced.
- Limited codification of knowledge for future generations. Detailed operating procedures tend to be written by professionals and are not tailored to shopfloor employees in the working language of the company.
- Outdated data. Despite assets being constantly adjusted to changing client needs, lack of digital documentation leads to a discrepancy between as-built and as-documented and produces a major risk for proper HAZOP controls.
- Lack of continuous improvement mindset, as organisations over-estimate the longevity of past successes such as low incident scores.
- Deprioritising maintenance: There is frequently a lack of consistent preventive maintenance and operational knowledge of equipment’s mechanical integrity to avoid unexpected downtime of facilities.
How should the chemicals sector embed a continuous improvement culture?
Despite the fact that the chemicals sector in Europe may be vulnerable to reactive or dependent safety cultures, there are behaviours that can be fostered to improve the organisational attitudes toward safety and develop a continuous improvement mindset. These include:
- Inclusion and engagement in safety management: Discussions about prevailing risks in the company should belong on the day-to-day agenda of all employees in a company and should not be the sole preserve of experts. One of the most important tasks of managers and supervisors should be to regularly exchange ideas with employees, to develop them further and to jointly look for opportunities for improvement.
- Dynamic risk assessments: Constantly monitoring and questioning the robustness of risk barriers in the field reduces the likelihood of significant accidents and damaging events. The time spent on this is well invested, since it matures the organisation from a compliance-based approach to a more dynamic method of managing risk.
- Prioritising operational excellence: Ensuring that operating models are both adopted with discipline and are actively adapted to market conditions is an excellent way of balancing both risk and production priorities. In our experience, implementing a well-designed maintenance and reliability programme enables the operational resilience required to allow for agile responses to production needs.
- Transforming organisational culture: Addressing complacency through engagement, particularly through the right kind of explanations for functional experts that might be resistant to change, can have a substantial impact on the discipline of safety-critical tasks. Similarly, engaging the whole organisation in safety culture adoption and championing is essential, particularly if firms are undergoing mergers, outsourcing or downsizing, which can hinder cultural cohesion.
SUCCESS CASE STUDY A chemicals company in Pakistan that produces poly-vinyl chloride, caustic soda, sodium hypochlorite, hydrochloric acid and other chlorine by-products successfully focused on the operational implementation of a safety and process management system to improve safety performance, decreasing injury rates by 76% over three years. The success factors of the programme included:
|
Conclusion
Although the chemicals sector in Europe is a mature industry with resonating influence in downstream sectors, it can be more proactive in addressing its vulnerabilities to severe safety and fatal incidents. Moreover, the macroeconomic environment in Europe, the reduction of entry-level technical tradespeople and the ageing workforce and the re-alignment of business portfolios are all influences that make the chemicals sector in Europe especially susceptible to reactive safety cultures that lead to fatal accidents.
Whilst this situation is not solvable through a single approach, the experience of dss+ suggests that focusing on inclusion and engagement of all levels of the workforce, dynamic risk assessments, a robust and disciplined approach to operational excellence and a focus on establishing the right organisational culture, will establish a strong foundation for the reduction of operational risks and help the sector to protect lives.