Freyssinet
Bridges and civil structures, buildings and skyscrapers, industrial facilities and stadiums-these are the heart of the Freyssinet business. A leader in specialist civil engineering, the company is also recognized for its unwavering dedication to safety. Recently, however, its Thai subsidiary challenged itself to weave a stronger, consistent safety culture throughout its operations.
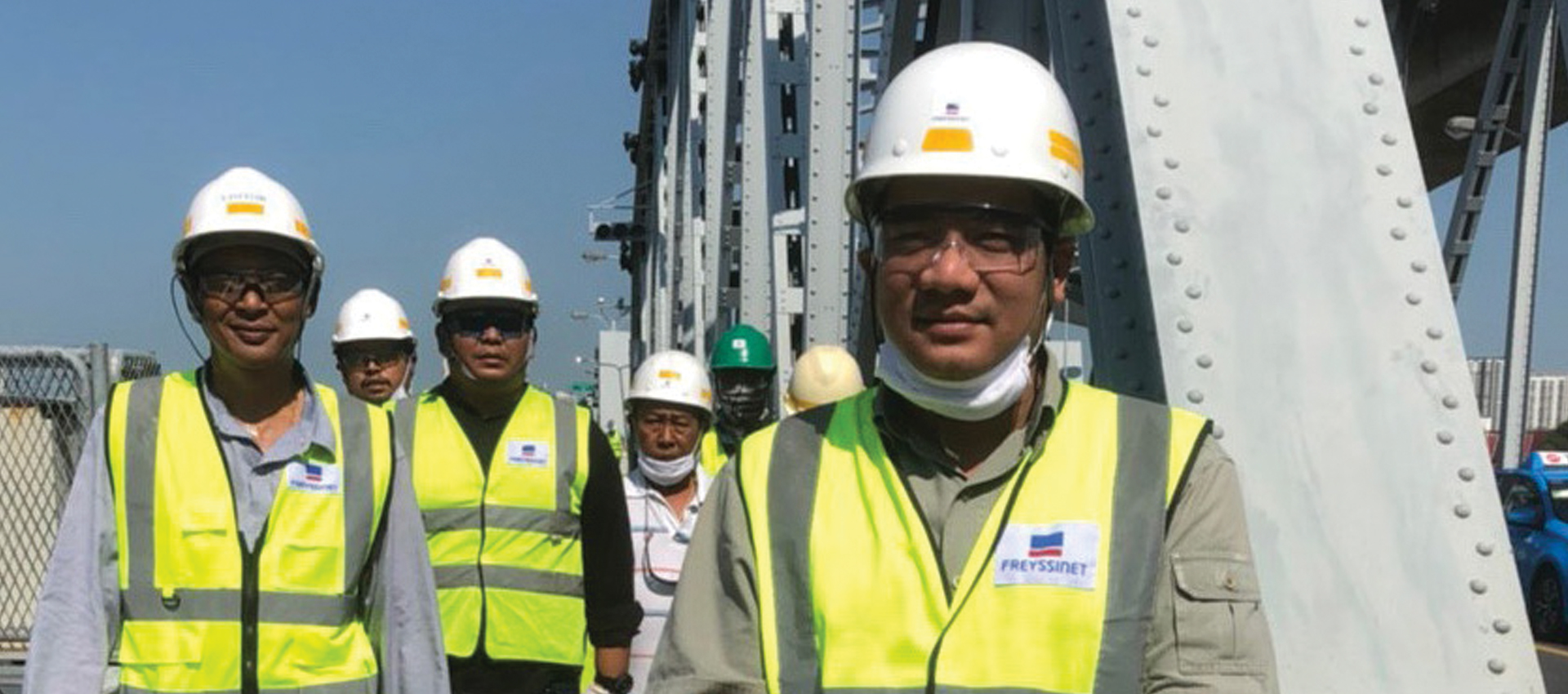
Beyond the Limitation: Freyssinet Thailand casts off doubts to embrace a safety culture change
Risk awareness campaigns and extensive communications were well established at Freyssinet Thailand, but attitudes around safety seemed to have reached a plateau.
An internal audit found an inconsistent safety culture-reporting and competency needed improvement and workers felt unable to challenge leaders on the balance between operations and safety. Managing director Dr. Borvornbhun Vonganan recognized, "It was as if unknown limits were holding us back," and set out to radically shift the organization’s thinking.
Over the months that followed, Freyssinet Thailand worked with dss+ to significantly alter the way leaders, teams and individual front-line workers viewed and talked about safety, building in a level of ownership, accountability and trust that elevates safety from "something we do" to "who we are."
Leaders adopt a new perspective
When Dr. Vonganan laid out his vision to management, not everyone was on board. Some struggled with why they were being brought in. Wasn't safety, after all, the job of the safety team? But Dr. Vonganan made it clear that he wasn't asking others to do anything he wouldn't do himself. He led by example, just as he would ask his managers to do in the days that followed.
Based on their roles and self-identified strengths, the company's nine managers selected individual areas to focus on. Through coaching and field practice, leaders f irst turned their attention inward, looking at how they value safety and their role in creating a safe environment. Without this critical first step, it would be impossible to demonstrate felt leadership and workers' behaviors would be unlikely to change. Only after working on their own beliefs and actions could managers begin to modify the way they engaged with teams and encourage individuals to take ownership of their decisions rather than simply follow directions. For many leaders, project managers and safety managers, a key milestone was discovering how to engage positively around safety—learning to ask questions, listen to front-line workers and think of safety observations as a way to demonstrate care for their coworkers rather than an opportunity to find fault.
Workers step outside their fears
Speaking out and challenging managers goes against these workers' deeply embedded cultural norms. The workforce had to see real change in management behavior before they trusted that they could speak freely. As they witnessed how safety discussions shifted away from negativity and toward protecting everyone's wellbeing, they felt the courage to give it a try.
Through the dss+ STOP.™ program, as well as other engagement tools and training, dss+ eased workers past their instinctive discomfort, helping them identify atrisk behaviors and unsafe conditions—even outside their own areas of responsibility. Team members learned to engage in more productive interactions, observations and discussions around the root causes of safe and unsafe situations. Conversations about rule breaking, for example, follow simple but effective guidelines to ensure that dialogue is free and open without blame attached. Discussions are approached from a positive perspective, everyone involved is asked to weigh in on solutions, participants agree to mutual commitments and the meeting ends with an expression of appreciation for one another's concern.
Front-line engagement was essential to this transformation, so every initiative at Freyssinet emphasized the importance of safety at a personal level. "dss+ helped us see the importance of the human factor," explained Dr. Vonganan. "We had to help people understand that we weren't trying to improve our safety statistics or put more burden on their shoulders. We wanted to do this because we didn't want them to get hurt—because we care."
From positive steps to sustainable change
As the new concepts began to find their way into everyday situations, workers gained confidence and leaders showed their support, creating a positive spiral.
In one case, an employee intervened when he noticed that work on a railway bridge was being performed without harnesses. Demonstrating care for his fellow employees ensured that the workers were properly secured and work quickly resumed without the risk of serious injury. On those occasions when teams couldn't solve problems themselves, such as at a site with missing handrails, they had a clear process for escalating issues to ensure prompt resolution. What's more, they knew they could take those steps without fear of reprisal. Ultimately, workers began to embrace personal accountability for safety, rather than trying to avoid it, knowing they were helping themselves and their coworkers get home safely every day.
The difference in employee behavior was unmistakable. Yves Barge, Freyssinet Regional Director, Asia, stated, "People have really started to understand that it's important to report unsafe acts and near misses, as it will improve our ability to find the causes and act before accidents. From the first meeting to nine months later, the change was tremendous. People were very open in discussing and exchanging together about improvements." The impact often extended beyond Freyssinet team members to other site contractors, helping instill the mindset that safety is truly every person's responsibility.
Clear governance instills good habits
Like any transformation, changing mindsets requires a systematic approach to driving and measuring improvements. Desired habits are entrenched through repetition and consistency, so dss+ encouraged Freyssinet to establish rituals for regular site visits and observations, monthly meetings, and strict KPI monitoring and reporting.
To roll out the new concepts across the operation, engineers were trained to supervise foremen in safety observations, hundreds of workers benefited from upskilling and a train-the-trainer program was established to ensure sustainability. Across 60 locations, more than 800 people were touched by the program.
Over time, meetings have taken on a new tone as they focus on recognizing achievements—sharing examples of successful teamwork and applauding in-the-field solutions to at-risk behaviors. Mr. Barge says the difference is evident. "Before, they were pushing against safety incidents and now they are really trying to be one step ahead, coming up with proposals to improve safety rather than waiting for incidents or accidents."
Benchmarking achievements
Unsafe acts reduced by 56%
After implementation, the frequency of accidents was reduced from 8.75% to 3.86%.
When Freyssinet embarked on this transformation, their aim was to establish safety not as a program, but as an integral part of their employees' mindsets. As observations turned people's attention to what is being done right (and not just what could be done better), reports of safe acts and conditions began to outstrip unsafe acts by wider and wider margins. And it's no surprise that embedding a consistent safety culture across the organization has led to significant reductions in the frequency and severity of incidents. "This change of mindset will, we hope, not only affect safety, but all matters," remarks Mr. Barge. "The site that is well prepared and well organized, where everybody knows what they have to do and how to do it in a safe way, is a site which will be successful.
Days off work reduced by 67%
The severity of incidents, measured in days off of work, was reduced from 0.24% to 0.08%. The company is careful, however, not to become complacent. "We have not had a serious incident or fatality in 2-1/2 years," notes Mr. Barge, "But we know we have to continue." Dr. Vonganan agrees, "It's a long journey. People may look at this as a success—they can see that we've improved. But we still have a lot to do. And we're doing it every time we visit a job site." "Working through this cultural transformation with dss+," adds Dr. Vonganan, "Didn't just make us safer. It helped us learn to work together better. What's really rewarding is to see the safety mindset spreading outside our company, as we care for people around us."