Harness Technology to Improve Risk Management Performance
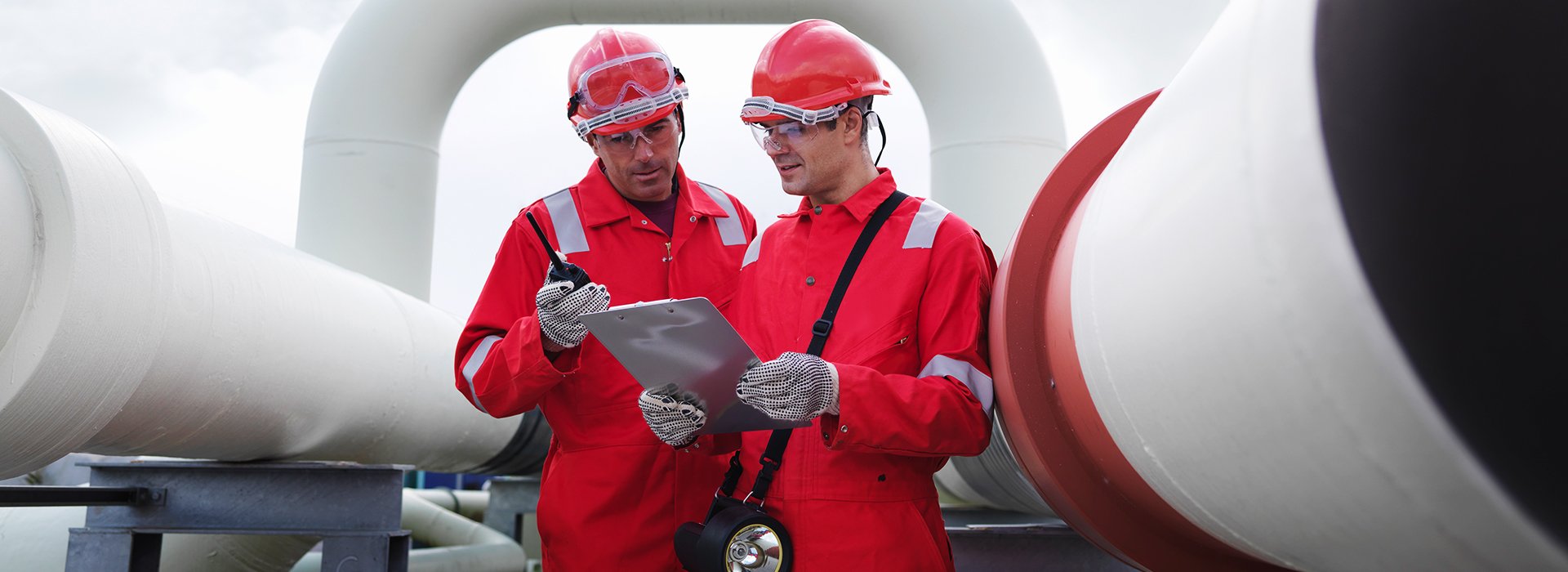
The implementation of management systems has been a common approach over the past 30 years to improve performance in areas such as quality, safety and environmental management. In many regions and industries these management systems are now in place and it is time to move to the next level to further improve performance. That opportunity for improvement lies in the effective use of technology and data analysis.
The prevalence of technology in today’s business environment dramatically increases opportunities for organizations to capitalize on new data streams to improve performance and outcomes. Today, it is estimated there are roughly 10 billion connected devices sharing 4 trillion gigabytes of data, and by 2020 those numbers are expected to surge to 50 billion connected devices sharing 40 trillion gigabytes of data. (Cisco, “Internet of Everything” and Oxford Economics, “The New Digital Economy.”)
Never have businesses been able to leverage so much data to improve their processes. Those companies that effectively harness this data to reduce incidents and increase safety compliance, increase productivity and efficiency, and achieve sustainable growth through new and improved products are in a unique position to increase their overall business performance.
With so much technology available to companies today, it can be easy for its use in the business environment to become an example of “the tail wagging the dog,” in which companies deploy various well-intentioned technologies, but are unable to fully harness them and maximize the benefits. They are unable to capture all of the benefits because they do not have a strategy that ensures the integration with the existing management systems. This particularly has the potential to occur in the area of operational risk management, where there has been a proliferation of technologies related to improving a company’s health, environment, and safety (HSE) systems.
To be sure, these technologies have the capability to reduce an organization’s exposure to risk and increase its ability to develop predictive solutions to anticipate risk. But, how do companies know which technology solutions are ideal to enable them to improve their HSE performance, achieve desired outcomes without creating unnecessary work across the organization, and effectively integrate them into their processes and culture to increase productivity and efficiency?
To successfully leverage technology within an organization, there are three things companies should do:
- Demonstrate the value of the technology to the end user.
Here, “end user” is defined as the individual operator or floor employee, not the C-suite executive. While making clear the business advantages and return on investment of technology to corporate leaders is important to secure the funding, the successful integration of technology requires that employees who use the technology understand how it will improve safety and efficiency outcomes for them directly. Whether technology is used for training, such as virtual reality and simulators, or for real-time data collection, such as drones and wearable devices, workers must acknowledge how technology benefits them directly before successfully adopted and integrated into a company's safety processes.
In doing so, there are two noteworthy hurdles that often must be overcome. First, some workers could be reluctant to use certain technology, particularly wearable devices, due to privacy concerns. It is important that companies clearly develop and communicate how data will be gathered and used from such technology and that the intent of the monitoring is solely to promote worker safety and increase work quality. Devices that simply track an individual’s movement throughout the workday are not necessarily useful in providing data that improves worker safety, but those that track their movements in high-risk areas or localize people during an emergency certainly are. So, too, are wearable devices that collect data from employees to predict how long they can be in a work situation, especially those that are high-stress, before becoming fatigued and increasing the risk of a safety incident. In cases such as these when these devices can provide beneficial data to reduce risk, an independent third party may be able to anonymously collect and aggregate the data on behalf of the company, extract learning and enable predictive actions. The new technology can also increase the level of engagement with the worker and lead to increased risk awareness at the worker level.
Also, cultural issues relating to the age of workers within a company can impact how quickly technology is accepted and utilized. Workers who are older tend to be less familiar with the latest technology, while younger “Millennials” are quite accustomed to recent digital trends and more comfortable with using newer technologies. (PD Quarterly, “Millennials and Technology in Today’s Workplace,” Lauren Stiller Rikleen, February 2014) Companies should take this into consideration when selecting and deploying technology, and prepare an adoption plan that is customized to the digital skills of their particular workforce. - Don’t deploy a new technology system within an already flawed process – it won’t work.
Don’t count on a new technology to yield improvements in an already broken process. All you can expect to achieve is a higher volume of data that does little to actually reduce risk. Before selecting and implementing any new technology, companies should conduct a thorough review of their processes to ensure their operational risk management system is robust so any new technology can leverage data to yield noticeable improvements.
The ability to understand which data sets are truly relevant and to select the information based on its value in supporting decision-making is another key requirement. Hence, a focused audit of the available data and their quality can help in improving the process.
For example, over time companies may add to their processes various HSE systems designed to address specific compliance obligations that may arise. These new systems can eventually result in a burdensome and bureaucratic conglomeration of systems in which workers spend more time completing checklists than necessary. The goal should be to streamline the process by identifying technology that can ensure compliance while also increasing worker efficiency.
Also, companies need to start with the basics before deploying new technology: Ensuring that risk management processes are in place, an organizational structure is in place to support the processes, the process aligns with the business strategy, and metrics are established to monitor the performance of the risk management system. By starting with a strong, effective base, technology will be more effective. - Ensure any new technology is fully integrated with operations.
An increasing amount of available technology is effectively creating separate “silos” between safety and operations. This can not only weaken a company’s safety culture but also reduce the value and effectiveness of the technology itself. The ideal solution should integrate with all the critical business processes of an organization to yield measurable improvement that contributes to creating a culture committed to safety, motivating employees, changing behaviors, and encouraging individual ownership of results through the active participation of corporate leadership, from C-suite executives to the critical level of first-line management.
An example of this is the use of monitoring equipment in the trucking industry. One major firm installed this equipment throughout its fleet and was not prepared for the information that it would provide about the performance of its drivers. They had to develop new processes to modify driving habits rather than being focused on disciplining mistakes.
A new technology solution that aims at producing predictive and prescriptive analysis from data coming from the field operations, the manufacturing environment or just feeding reporting requirements, should be designed around platforms that connect to the existing enterprise IT systems (e.g. SAP). For example, access to the human resource database will allow organizations to correlate incidents to the company demographics to understand potential patterns leading to re-occurring events; connectivity with a vendor and contractor database will not only assure compliance, but also help to understand who are the contractors with the best safety performance and the ones who represent a potential risk, and so on.
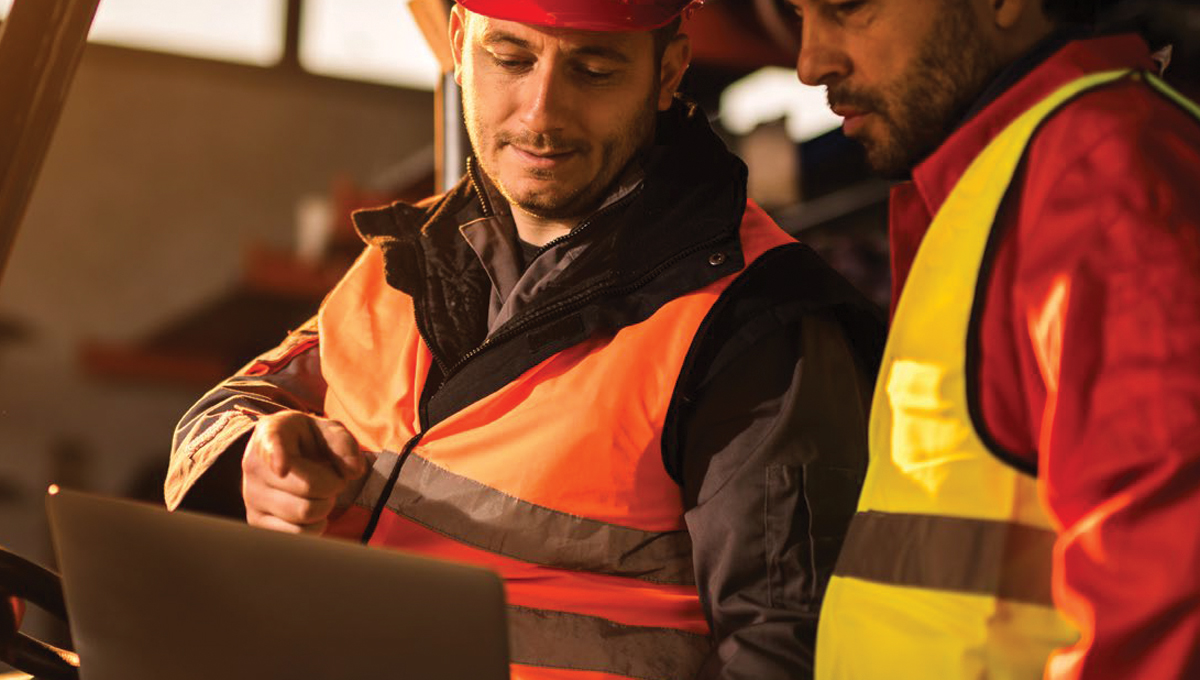
We need to shift the mindset of many leaders who view mobile devices as a workplace distraction. They need to see these devices as a strategic tool that can provide meaningful information in a timely manner and increase employee engagement. To enable mobile solutions which leverage the native technology of tablets and smartphones to collect incident data, report near misses, and report audit findings, we need to ensure they properly communicate to the other systems to define the context of observation and to report it at the right company level.
While the three points above are essential to successfully utilizing technology to improve efficiency and reduce risk, it can also be beneficial to apply existing relevant data gathered from other companies. This supplemental data can provide companies a sense of “business reality” and help them gain additional insights, enabling them to make more informed, real-world decisions to improve performance.
Using technology effectively can enable companies to develop solutions and make sound decisions that can improve business performance. But, simply deploying new technology for technology’s sake is not sufficient to make sense of available data to improve operations, manage organizational risks, and achieve strategic goals. Companies that take the time to evaluate whether processes are effective before adding new technologies, make clear the benefits of technology to workers, and ensure technology integrates fully with safety and operations will increase their ability to make the right business decisions that will improve their performance.
dss⁺ has used its experience advising companies on operational risk management to assist the Saudi Arabia Basic Industries Corporation (SABIC), a chemical manufacturing company headquartered in Riyadh with operations in the Americas, Europe, Middle East, and Asia Pacific. dss⁺ is designing a system to consolidate and integrate data among its various locations using its subject matter expertise and data obtained from its proprietary dss⁺ Safety Perception Survey™, which has collected millions of responses to safety- and risk-related questions from companies across dozens of industries. dss⁺ has designed a comprehensive risk profiling tool to enable leaders to make better risk-based decisions. dss⁺ provides a web-based platform suitable for mobile applications, accessible by any business leader seeking to manage operational risk across a complex business portfolio.