Linde Group
The Linde Group engages the global organisation of their Gases and Engineering Divisions in safety and process safety improvements
Managing the safety of 65,000 employees and contractors that work in gases & engineering businesses, in more than 100 countries worldwide, is a challenging task. Even if company policy says that safety is the Number One priority, how can you be sure that everyone has the same understanding of and attitude to safe behaviour? This was something that concerned new Linde Group CEO Dr. Wolfgang Büchele during his appointment in May 2014. "Although the Lost Time Injury Rate (LTIR) in the gases and engineering businesses had halved over the previous five years to 0.2 (per 200,000 hrs) this reduction was not large enough or fast enough for the senior leadership team. A step-change was needed," he says.
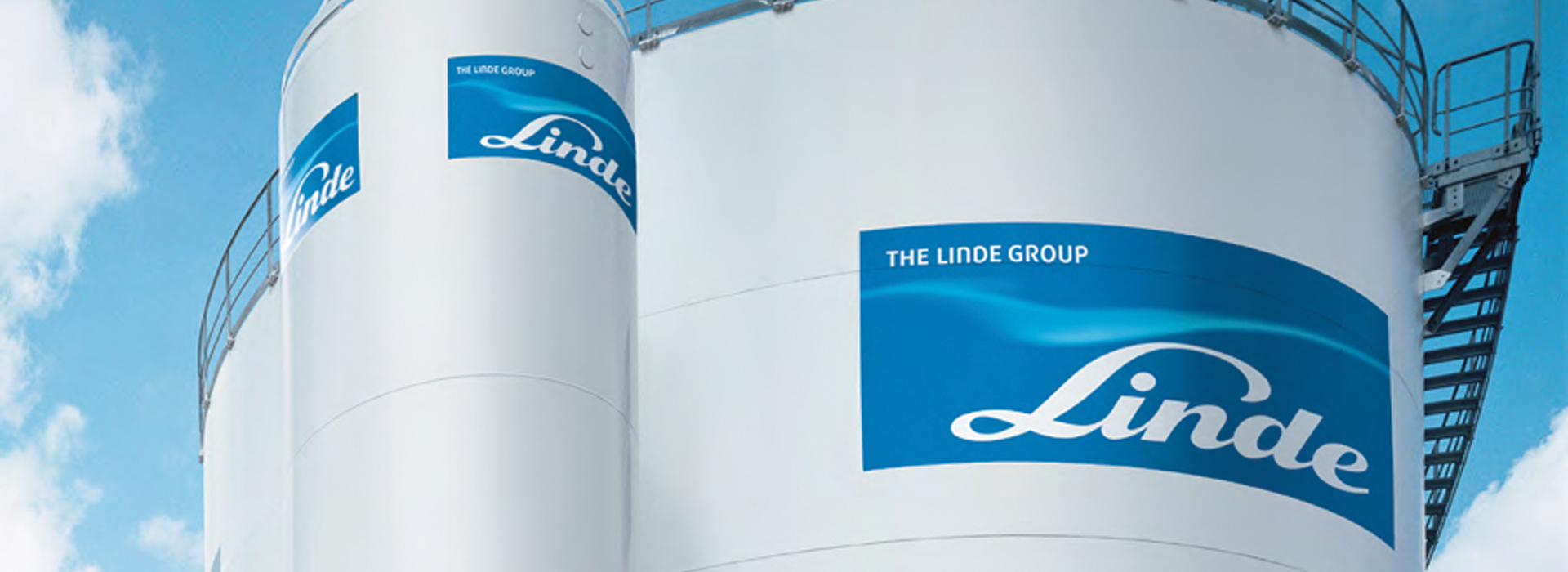
Extracting Superior Value from Assessing Management Systems, Leadership, Culture and Behaviours in Safety and Process Safety
The Linde Group is one of the world's largest suppliers of industrial, healthcare and speciality gases, and a multinational engineering company. The organisation has grown rapidly, partly through acquisition, since its beginnings in Germany in 1879. It now consists of ten separate business units with over a thousand manufacturing, filling and distribution sites. Phil Graham, based in the UK, has global responsibility for HSE and Quality. His focus is on eliminating severe injuries and fatalities, as well as achieving a step-change improvement in recordable injury and process safety performance.
Although most performance indicators had been showing a significantly improving trend in safety performance from 2007, progress was not rapid enough to satisfy The Linde Group's senior leadership. Towards the end of 2014, the decision was taken to arrange an external assessment of the company's approach to managing safety and process safety. The intention was to review not only management systems but also, leadership, culture and behaviours.
We chose dss+ because of their track record as an owner-operator, their experience with consulting with clients globally on behaviour and process safety, and their analytical tool set.
Phil Graham, Group Head of SHEQ at The Linde Group
"Our aim was to understand our current safety maturity and to identify key actions that would allow The Linde Group to become a true leader in safety." dss+ was briefed to evaluate the entire Linde Group"s global operating businesses from industrial gases to engineering. The assessment was also to include all central functions from the executive board level right through to the front line.
Understanding guides cultural transformation
dss+ developed an assessment process tailored to The Linde Group's requirements and deployed multiple tools and processes in order to gain insights into the effectiveness of existing management systems and strategic programmes. It included a survey and assessment of the values, attitudes and beliefs (VABs) of The Linde Group's 40 senior managers, "field" visits to representative Linde Group operating sites around the globe, and a safety perception survey in 42 languages in which 45,000 employees and contractors participated. dss+ set out to provide The Linde Group with customised data and information rather than a reference model so that the company would gain a clear understanding of the context for its current performance and would be able to use that data to address targeted improvements at a systemic level.
Our aim was to understand our current safety maturity and to identify key actions that would allow The Linde Group to become a true leader in safety.
Phil Graham
The VAB survey was conducted online. Results were initially discussed individually with all senior leaders. This helped to uncover deeply-held beliefs about the importance of and the approach to achieving world-class performance in safety. The VAB survey also highlighted how these beliefs were driving behaviours that were supportive of or detrimental to the execution of the strategy. By examining such questions as what it takes to make safety work and why safety is currently not working as well as Linde hoped, dss+ was able both to measure the extent to which individual attitudes and beliefs were influencing and affecting safety and assess the intrinsic motivation and competency of individual managers and groups of managers (operations and functions). The survey also gave the consultants a very good overview of the extent to which safety was embedded in the line organisation.
Director of Operations dss+ EMEA and Engagement Leader for the work with The Linde Group Armand Klein explains: "By challenging senior business leaders to reflect on the priority they give to safety and on their role-modelling of safety, we kick-started a process of engagement with the topic. The survey and its results also reinforced The Linde Group's key leaders understanding that it takes their visible commitment and behaviour to communicate the importance of safety and to set consistent standards for performance."
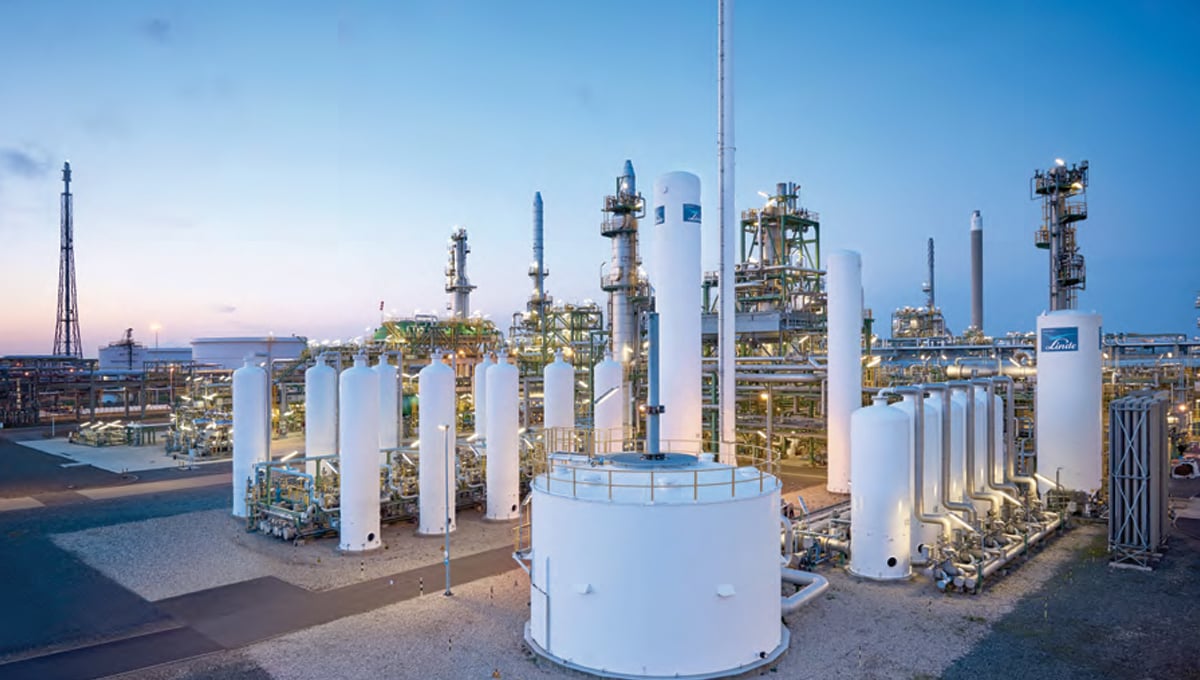
Changing attitudes
In parallel to the VAB process, dss+ carried out a survey of employees' and contractors' perceptions of how safety was being managed throughout The Linde Group. Almost 70 percent of all employees and long-term contractors took part, providing a highly representative picture of attitudes and beliefs. This perception survey is a useful benchmarking process for corporate safety culture and provides key insights into the current level of safety maturity within a company compared to world-class safety cultures.
Armand Klein says, "early on in the process, it became clear that very different perceptions of safety existed across the organisation. The management and employee surveys helped The Linde Group to see how people at different levels and sites viewed safety. It also showed them why safety was not working in the way the organisation wanted it to."
Backed by a very well-orchestrated and intense communication campaign, the survey allowed the company to begin engaging with employees and discuss safety more in-depth. It showed employees how much The Linde Group values safety as well as employee feedback and input. And that was appreciated by many employees. As one respondent to the survey from East Asia said: "It shows the company is listening to employee concerns and making positive strides toward improving employee satisfaction and customer service by allowing so much input from staff regarding all aspects of employment and safety."
The honest answers given by employees show that many think about safety and how it should be viewed by the Linde Group. The answers given in the survey ranged from small issues to large, raising good points and feeding back that many see the relevance of safety rules to the world outside of work as well. A German employee working at the RBU Europe Central commented: "I think it's very good that Linde places great value on safety and sets high standards in this regard. Most of the safety rules also apply to everyday life and should be taught not only by companies like Linde."
A similar comment came from an operative in South East Asia who said: "We are more concerned about the safety at our place of work. Yet after finishing work we go back home. How many of us follow safety behaviour at home? Safety should be made a practice of common behaviour, not as a part of a job but as a part of life. Our organisation is trying."
"I feel the safety culture within my workplace takes precedence over and above anything else and there is a very strong awareness of the safety culture. It is the first thing mentioned at any meeting."
Over at the Cryro AB site, a French employee has seen the changes the company has made in safety and says: "Everything can't be perfect all the time. There will always be things that can be improved. However, our company and our staff are very involved in safety. I have worked here for more than 25 years and have seen how things have evolved."
An employee at Linde Process Plant in the USA commented on the larger picture and sees The Linde Group as having "in place a solid, integrated safety system that is (in my opinion) set to a higher level than many if not all companies I have seen. Job safety here is the best of the best."
This sentiment was echoed by an employee at RBU South Pacific who says: "I feel the safety culture within my workplace takes precedence over and above anything else and there is a very strong awareness of the safety culture. It is the first thing mentioned at any meeting."
Many employees said they liked the survey and wanted it to be repeated on a regular basis.
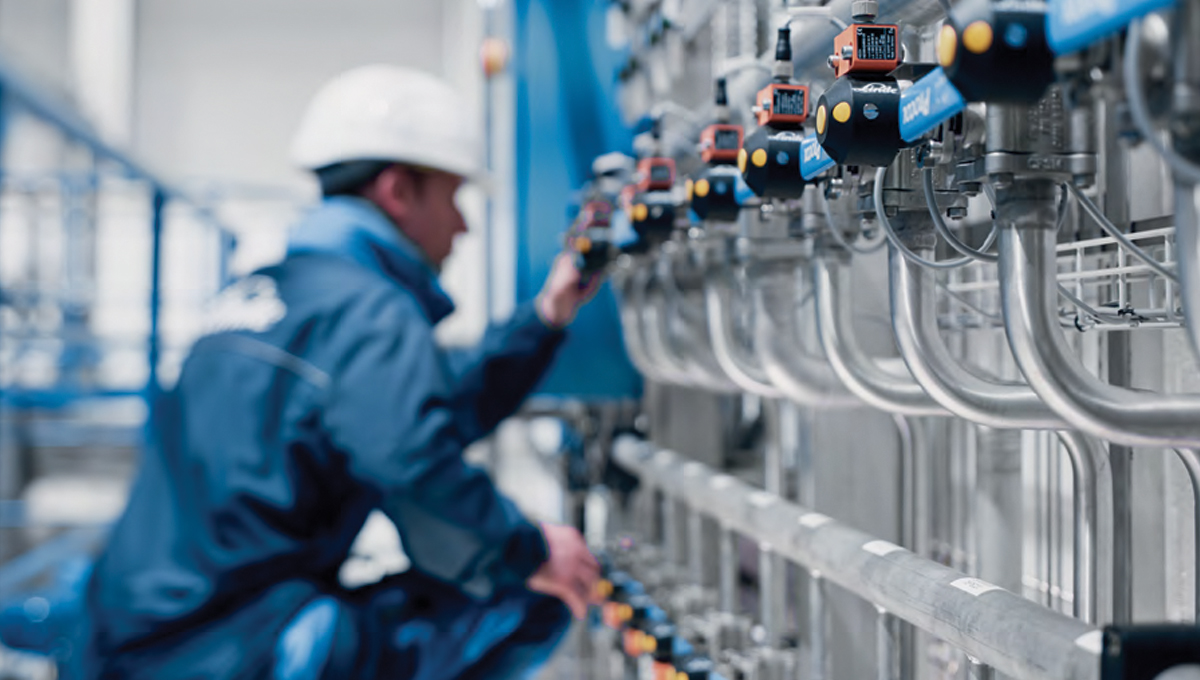
Operational site assessments
As a part of its evaluation, dss+ visited 24 operating sites representing all ten business units of The Linde Group. This took the involvement of 24 consultants working across Europe, North and Latin America, Asia, and Australia. The objective of the field assessments was to validate the hypotheses developed on the basis of the survey results and the review of management systems in practice. The aim was also to assess the effectiveness of The Linde Group's approach to managing and improving performance in safety and process safety. "The key question for any assessment of this kind is how the strategy translates into actions in the field and whether these actions will ultimately deliver the desired performance, or not," Armand Klein says. "Field observations are essential to drawing conclusions that are insightful enough to help initiate real change."
The Linde Group derived superior value from this assessment work because they committed some of their best people to support the effort and they accompanied it all along with a powerful communication campaign. This significantly increased awareness of safety and created renewed momentum to engage the whole organisation.
Armand Klein, Director of Operations dss+ EMEA
The results from the surveys and the field assessments were compiled to allow both dss+ and The Linde Group to identify the systemic issues at the root of the organisation's current performance. Subsequent key recommendations from dss+ focused on aligning The Linde Group organisation around a set of shared beliefs, empowering and engaging people at all levels in the improvement process, strengthening the effectiveness of current processes, building competencies, and increasing operational discipline to achieve sustainable systemic improvements.
The results and dss+ recommendations were analysed in two preparatory workshops, that involved both the client's and the dss+ project teams as well as a cross-section of senior business and functional leaders. This analysis led to the formulation of a strategic roadmap for improvement which was, reviewed, discussed, and prioritised with The Linde Group's Executive Board who appointed a task team of senior leaders to execute the roadmap.
Phil Graham summarises the effect of the dss+ assessment, "The assessment was very valuable to us in that it provided us with deep insights into what was preventing us from delivering world-class performance, and also included the data to credibly support the conclusions. It was a very powerful method of engaging our leadership and employees at all levels."
Workshops with each of the business unit management teams were conducted to identify the focus areas for improvement and develop both short and long-term action plans. This final part was critical to the overall success as it ensured a high level of engagement and ultimately ownership for future improvements.
Armand Klein concludes, "The Linde Group derived superior value from this assessment work, because they committed some of their best people to support the effort and because they accompanied it all along with a powerful communication campaign. This significantly increased awareness of safety and created renewed momentum to engage the whole organisation".