Maintenance & Safety Practices at a Food Manufacturing Plant
In this case study, we describe how dss+ assessed the current level of maintenance and reliability maturity, and fostered safety leadership skills for a food manufacturing plant where maintenance performance was not adequately measured or benchmarked. Our consultants worked with the client to reduce their critical risk exposures significantly and increase work completion rate by optimizing shutdown operations.
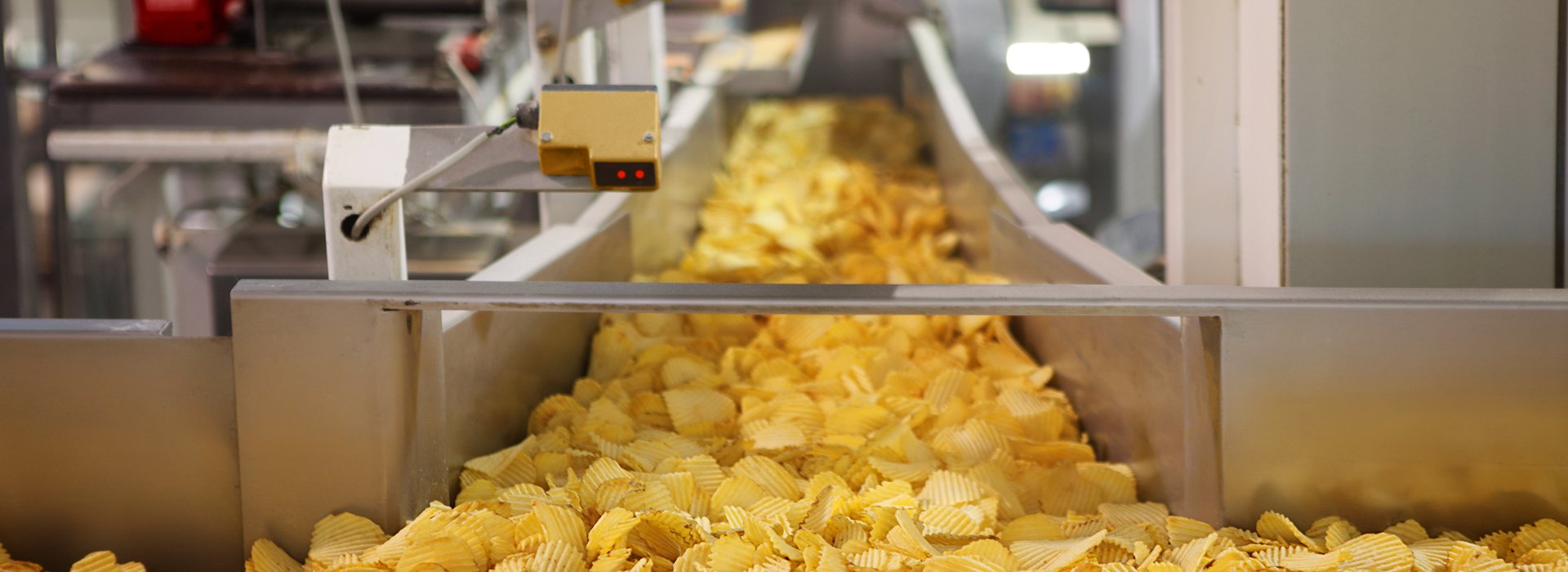
Challenge
Recent incident investigations as well as trends in key production metrics highlighted a lack of consistent maintenance and reliability practices in this food manufacturing plant.
It is worth noting that a large proportion of the maintenance and reliability team is new to both the industry and the business. Therefore, there was no shared vision of what good looks like.
Finally, maintenance performance was not adequately measured or benchmarked.
dss+ Approach
dss+ assessed the current level of maintenance and reliability maturity, and fostered safety leadership skills by:
- Establishing key metrices with our assessment tool and brown paper method
- Reviewing and improving of isolation procedures
- Standardizing key leadership and planning activities
- Documenting process and procedures
- Improving organizational structure & reporting: supervision ratio was reduced from 1/33 to 1/6
- Deploying FELT leadership
- Focusing on safety: identifying high-risk areas and implementing measures to mitigate risks during shutdowns
The assessment tool shows what good looks like (GTP), what is needed now (GTA) whilst benchmarking the current state.