McClarin Plastics
Discover how McClarin Plastics created a culture of safety through communication with the implementation of dss+ STOP® training programs.
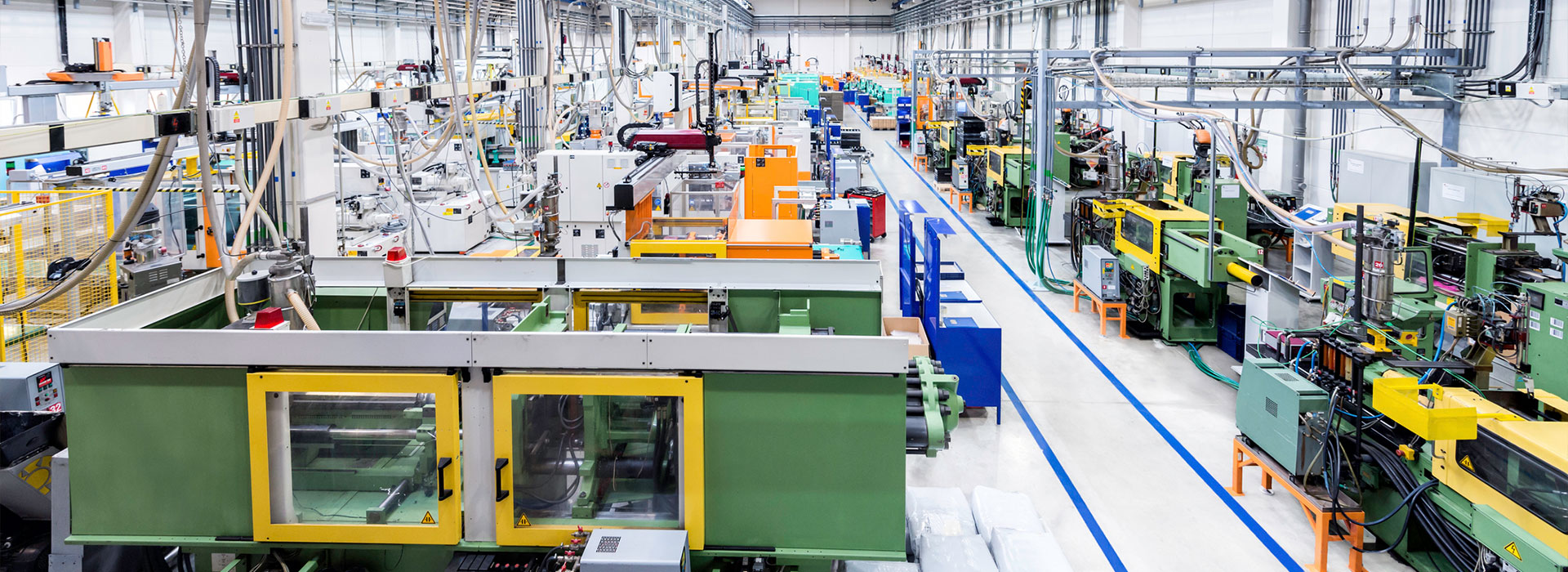
Challenge
The safety culture at McClarin Plastic’s Wapato, WA, plant suffered from a lack of engagement: employees were just doing what they needed to do to get the job done. Long-time workers were also stuck in their ways. Employees cared about keeping people safe in general but weren’t proactive about it.
Solution
McClarin implemented the STOP® for Supervision and STOP® for Each Other Safety Observation Training Programs.
Implementing a New Training Program Amidst a Pandemic
Taylor Wolfe, Environmental Health and Safety Specialist, was committed to training her workforce even while facing the difficulties and constraints of a pandemic. With full support from her plant manager, she began teaching small, in-person classes in September 2020. In the months since McClarin Plastics started the dss+ STOP® program, Wolfe has made significant strides toward reaching her goal of training the 160+ Wapato workforce.
One obstacle Wolfe discovered early on was that she needed to reach an audience comprised of a large percentage of native Spanish speakers. She tried translating some of the materials herself before finding out through her dss+ account manager that the dss+ STOP® program is available in multiple languages, including Spanish. The translated workbooks and videos have made a huge difference in employee comprehension. Now, each time Wolfe conducts training, two of the six classes are usually in Spanish.
Safety Program in Infancy Already Paying Off
The McClarin Plastics dss+ STOP® rollout is still in progress, but they can already point to successes with the program.
More Eyes, More Accountability
When Wolfe begins a dss+ STOP® training session, she asks employees who they think is responsible for safety. They point to her. By the end of the training, however, she finds that workers understand it’s not just the EHS, human resources or plant manager who’s accountable for safety; they realize that every employee plays an important role. Wolfe says she notices as training proceeds that employees begin to “bring up a lot of issues.” This valuable safety and production insight is passed on to the plant manager, and improvements are made to processes and protocol. Both Wolfe and her plant manager are encouraged that they now have “multiple eyes looking around.” Having more people aware of co-workers’ behaviour and the work environment means more people are taking responsibility for safety at the plant. This culture shift greatly improves incident prevention efforts. As Wolfe says, “We all need to look.” Wolfe has also noticed that supervisors are better able to enforce the rules now, since they discuss the “why” of working safely with employees during observations. This practice is creating a workplace where “everyone is looking out for everyone.”
Uncovering Root Causes, Finding Solutions
The conversations supervisors and employees are having during STOP® Safety Observations are bringing new light to old issues. Wolfe quickly reels off examples of safety concerns that are being resolved as a result of simply talking with workers. Wolfe noticed that workers weren’t wearing safety glasses when required. Often, noncompliance with PPE rules is chalked up to laziness. However, after discussions with employees, Wolfe discovered that the issue wasn’t the result of employees being lazy: workers’ glasses were fogging up due to wearing COVID-19 masks, compromising their vision.
Wolfe did research to come up with a solution that keeps glasses on and incidents down. Other workers were lifting their glasses in order to better inspect for damage on parts. After conversing with employees, Wolfe realized that lighting in the work area wasn’t sufficient for people to do their job properly. Wolfe states, “I wouldn’t have known if I didn’t talk to employees. It’s really important to ask those questions.” To uncover other trends and deficiencies, Wolfe pulls up data from dss+ STOP® observations in safety meetings using the STOP® DataPro® software, so the group can target safety issues and work at resolving them.
Improving Morale
McClarin Plastics has noticed a rise in employee morale now that workers can see that when they speak up, someone listens. Employees are witnessing improvements being made as a result of their contributions. They’re getting the message that management cares about them, which makes them more likely to keep speaking up about safety and production issues.
Having a Plan Matters
When asked what she would say to peers in the industry about the STOP® Safety Observation Training Program, Wolfe points to the organized curriculum. “There are not only discussion meetings and homework, but it ties in with videos, too.” She says “having structure and a plan for training keeps things going”—even during a pandemic. To put it simply, Wolfe states, “If you go in without a plan, it doesn’t usually go well.”
The Road Ahead Looks Bright In the few months after introducing dss+ STOP® training in the Wapato plant, McClarin Plastics saw the incident rate drop dramatically. They found further evidence that dss+ STOP® training was making a difference after a big hiring push saw a rise in incidents—the new workers had not received dss+ STOP® training yet. As the new employees began to go through the program, the incident rate started to fall again. The data encourages everyone that McClarin Plastics is on the right track with dss+ STOP® and headed for a bright future.
McClarin Plastics, LLC is a recognized leader in design, product development and manufacturing of highly engineered, molded plastic assemblies. For more than 60 years, they have been helping companies of all sizes find creative solutions using their various moulding processes to ensure proper material selection for customer applications.
www.mcclarinplastics.com