Mitigating Pipeline Operational Risks
Mention safety during pipeline construction and thoughts will most likely turn to preventing worker injuries and damage to equipment, but the risks involved go much further. Errors at the design and construction stage may only manifest themselves later during operation but have the potential for significant subsequent harm to people, assets and the environment. When preparing for pipeline construction, companies also occasionally overlook the risk of project time and cost overruns. So what should companies bear in mind when planning “safe” pipeline construction?
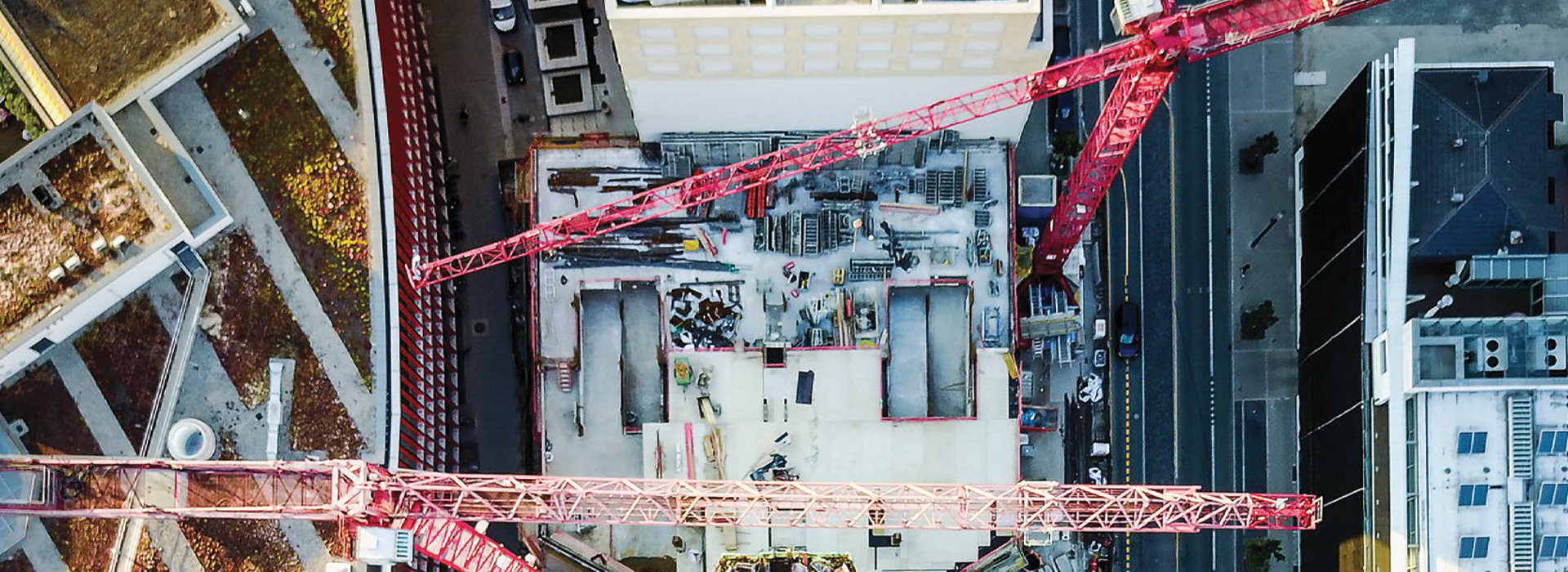
Pipeline life cycle risks
At dss+ we define as risks everything that threatens to compromise business objectives along the entire life cycle of an asset. For a pipeline, that life cycle can be said to consist of the following stages:
The business objective in this context may be described as guaranteeing the reliable and safe transport of a product from the source point to the final receivers in a manner that is safe and profitable. That requires the prevention of all potential social, health, safety and environmental (HSE) and process safety impacts as well as project time and cost overruns. Typically, a pipeline system will also include pump stations and terminals for liquid pipelines, as well as gas compressor stations for gas pipelines, measuring facilities and other ancillary systems. Threat identification and risk assessments should be undertaken for all these facilities as every stage of the life cycle can affect the successful achievement of these business objectives and requires careful advance planning.
Unless process safety is integrated into pipeline projects from the beginning, it is difficult to assure the transition of effective process safety standards from the start-up team to the operating team and, eventually, to the decommissioning team. Adequate safety management however begins with the planning, design and construction stages, the phases on which this article focuses.
The all-crucial design phase
Most process safety risks which materialise during the operation phase of a pipeline can be anticipated and contained at the design stage. But lack of understanding and inadequate control of risks at this stage of the pipeline life cycle threaten subsequent safe pipeline operation and may also result in project time and cost overruns. The most frequent omissions we have seen during assessments at pipeline operator sites include a lack of defined safe pressure and temperature operating limits, insufficient clarity on the type of material that is to be transported, the selection of inappropriate pipeline material for the liquid transported, the failure to consider critical external factors that can affect pipeline integrity, insufficiently developed operating, maintenance and emergency procedures, no quantified safety risk assessment, and the list goes on. Such omissions at this key planning stage of pipeline construction and operation leave the pipeline exposed to future risks, which can be aggravated if the pipeline changes ownership or operator. If no information on pressure and temperature operating limits, for instance, is readily at hand in such a scenario, there is a chance that the pipeline will be run beyond its design limits resulting in loss of integrity. Similarly, if the design phase does not take account of external conditions such as seismically sensitive or environmentally vulnerable areas, the risk for negative ecological outcomes is higher. Spills and leakages during pipeline operation can often also be traced back to design errors, e.g. the lack of an adequate number of remote-operated shut down or non-return valves at key locations.
Beyond the more obvious process safety management oversights, quite a number of pipeline operators also do not conduct adequate environmental and social impact studies before commencing construction.
Common construction phase omissions
Inherent to any construction project are risks to the health and safety of the workers involved, which can result in immediate injuries and fatalities. The most common accident causes – slips, trips, falls, work at height, etc. – are not limited to pipeline construction. But there are other risks that are particular to the industry which are often unwittingly increased by lapses in behavioural safety. These range from dangerous handling of the pipe during transport, stockpiling and unloading to poor management of open trenches, work in the proximity of overhead power lines or incorrect storage, handling and disposal of explosives with potentially fatal consequences for the workers involved. These may all seem like obvious activities requiring careful safety management but are nonetheless areas of weakness we frequently see during visits to pipeline operators. Less obvious, perhaps, is the control of risks arising from contractor selection. Experienced contractors may be difficult to secure if there are several concurrent projects. As such, it is critical to conduct an early assessment of the contractor construction market to ensure not only adequate contractor capacity for the pipeline construction in the planned timescale, but also good safety capabilities. If inexperienced contractors are hired that is likely to have significant implications not only for safety, but also for the completion of the pipeline construction on time and on budget.
Added to these behavioural safety management issues during construction are process safety risks that can later seriously affect the integrity of pipeline operations and may also lead to project delays. Frequent issues we come across are ineffective pipe inspections and certification of pressure testing during manufacture, a lack of independent third party inspections of welding and radiography of welding, as well as of pipeline lowering in and backfilling - if the pipeline is unknowingly damaged during this delicate stage, defects will stay for the rest of the pipeline life. We have also seen wall instability and soil collapse during trench excavation lead to injuries and fatalities. Then there is interference with other buried services, e.g. other pipelines, utilities, etc. that can lead to loss of containment, fires and explosion - e.g. when hitting pipelines containing flammable material or electrocution when hitting power cables. Again, the list of common process safety failings is long and probably familiar to many readers.
Holistic process safety management
Rather than addressing these issues piecemeal, however, the key to ensuring safety at all stages of the pipeline lifecycle at the same time as efficient operations is a systematic and holistic risk management approach.
Every operator will have their own business objectives. If these are considered in conjunction with clearly defined life cycle steps, it is possible to identify and prioritise hazards or threats that prevent the fulfilment of defined objectives and put lives at risk. To assess and balance operational risks and process safety requirements accurately, pipeline operators should conduct a comprehensive Process Hazards Analysis (PHA). Its results should drive the design and implementation of process safety requirements, from standard operating procedure and safe work practices to mechanical integrity and quality assurance; training of personnel including contractors; incident management, changes in technology, equipment and personnel; and emergency management. Over the years, dss+ has realised the importance of engaging people down the line, including operators/technicians, in the PHA, to establish a better understanding and appreciation of risks, so they understand “why” they are expected to perform their actions in a particular way.
Recognising potential risks requires an understanding of the hazards of the material transported, the pipeline equipment design and the environment. This understanding provides the fundamental basis for differentiating risks according to their level of severity and likelihood of occurrence. The next step is to allocate resources accordingly. If the risk is higher, then there is an obvious need to have more layers of protection and detailed plans in place. A proper risk assessment helps to ensure that time, money and resources are spent based on the level of risk and that the appropriate return on investment is realised.
On completion of this threat identification, a risk register should be compiled which, at a minimum, should identify and classify hazards and associated risks, designate risk owners, set out prevention and mitigation policies and actions (with well-defined roles, responsibilities, timing, etc.) and include mechanisms for monitoring and auditing the continuous effectiveness of prevention and mitigation actions. It is important that this risk register is a “live document”. That means it needs to be reviewed and updated regularly as new threats can arise during any stage of the pipeline life cycle and certain already identified risks might become more significant. For example, if a new residential development is built close to the pipeline this may have an impact on pipeline integrity and loss of containment.
Managing the transition from pre start-up to operations
Process safety management is critical to help ensure not only safe design and construction of pipelines but mitigation of risk throughout their life cycle (see Figure 1). Information on process safety is necessary for the PHA teams at all stages so they understand the impact of proposed changes and can perform cyclical reviews. Aside from training the operations team and involving them in the project team from the outset, pipeline operators should also require the project team to prepare a process safety information package for the operations team. This is the foundation for identifying and understanding the hazards involved, the first step in any PSM effort. The package should consist of the following: hazards of materials, process design, pipeline design. As this information is very costly to reproduce if lost a permanent storage system should be put in place. It is essential that the process safety information requirements are built into design and procurement packages.
Conclusion
The vast majority of operators of pipelines take process safety very seriously and invest significant manpower and resources into establishing effective systems and protocols. Nonetheless, accidents keep occurring. A cradle to grave risk and impact assessment for the entire life cycle of the pipeline including the consequences of decommissioning can be helpful to plan and manage risk containment. At the end of the day, effective and adequate risk prevention as well as on-time and on-budget construction and improved operation all depend on how business objectives are set and the scope of risk analysis is formulated.
In mature companies, risk management is built into operations management – i.e. appropriate risk management is seen as an essential feature of smooth, safe and profitable operations. Risks, risk controls, health of critical risk controls are regularly reviewed and discussed at all levels of the organisation and made visible (e.g. through dashboards, visual aids, etc.), at an appropriate level of detail. The key threat to effective process safety, however, is behaviour. Process safety systems can be thoroughly planned, equipment highly sophisticated, procedures clearly outlined, but if an operator does not adhere to the rules, checks are not carried out thoroughly and the wrong lessons are learnt from incident investigations, then even good process safety systems will fail.
The benefits of a holistic operational risk management approach have been tried and tested by pipeline operators who have worked in conjunction with dss+ on improving their safety management strategies.