Pınar Çağdaş Duran: Leading with Example, Emphasising the Importance of Safety
With a background in chemical engineering, Pınar Çağdaş Duran’s career has been shaped by a mission to raise the bar on safety. As Technical Safety Director at Tüpraş, she tells dss+ how a team approach and a focus on leadership qualities is the best platform for achieving higher safety standards.
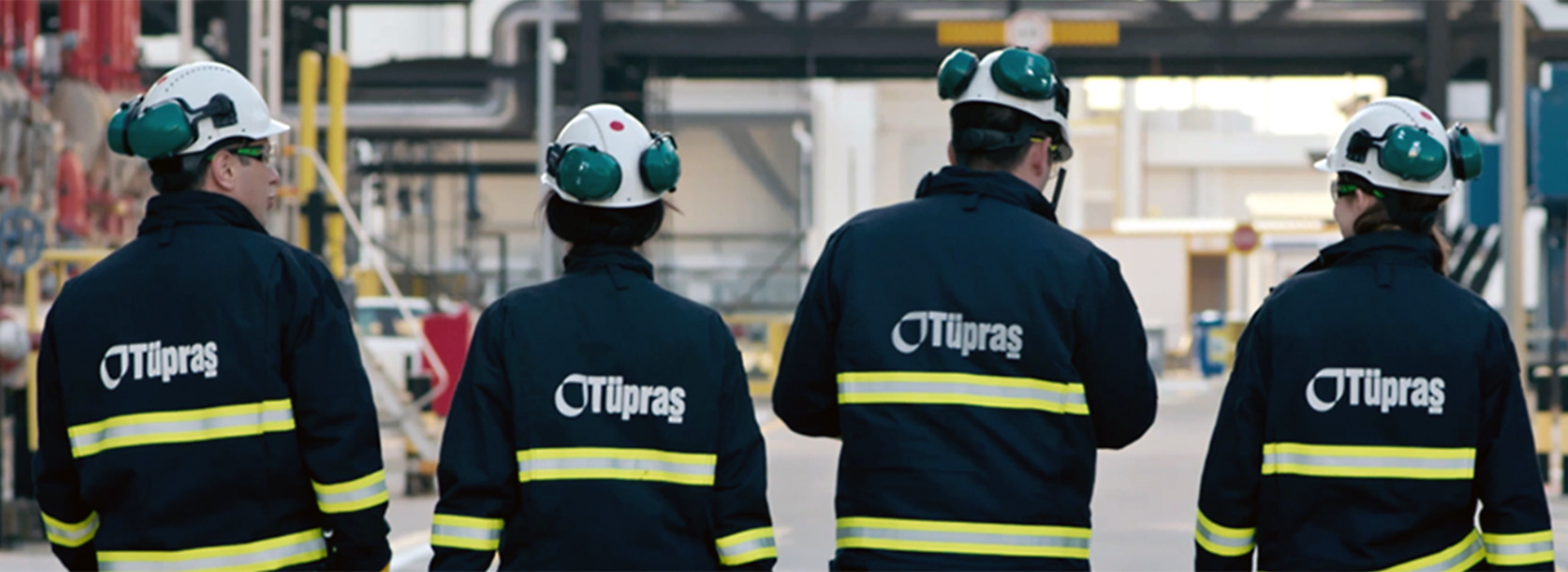
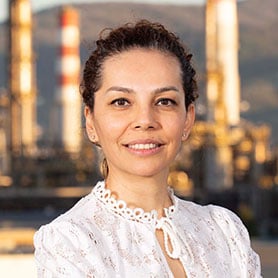
Pınar Çağdaş Duran
Technical Safety Director, Tüpraş
Q.
How did your career in health and safety begin and what milestones have shaped your journey? Tell us about your current role.
I completed my BA degree in Chemical Engineering in 2005. After my graduation, I started working at a power plant. My career in Tüpraş began at İzmir Refinery in 2007, and I have held various positions in production and process at different Tüpraş refineries. I saw that safety was an essential part of production and it significantly shaped my career and progress. Some of the most important milestones were the safety coaching I received and the safety culture project I worked on as a production superintendent. We developed this project with dss+ and continued with dss+ as our solution partner. Thanks to the experience I gained while on this project, my perspective on life changed, both personally and professionally. Safety became a priority and an indispensable part of my life. I assumed the role of Technical Safety Director at Tüpraş Headquarters in 2023. Since then, my colleagues and I have been working diligently to elevate Tüpraş’ safety culture to the highest level globally.
“A leader’s stance and attitude are the drivers of changing the safety culture and ensuring appropriate behaviours.”
–Pınar Çağdaş Duran, Technical Safety Director, Tüpraş
Q.
We often talk of changing mindsets and behaviours as an important driver of health and safety excellence. In what way can company culture and good leadership make a difference when creating a safe workplace? Any examples of how you have achieved this?
Company culture and effective leadership are equally critical in creating a safe work environment. Change starts with leaders who are the pioneers of change and lay down the basis of continuity. Good leaders act as role models and are followed by their teams. A leader’s stance and attitude are the drivers of changing the safety culture and ensuring appropriate behaviours. I had the opportunity to experience this while working in the production department. The more I cared about and emphasised the importance of safety, the more my team acted similarly and began to deem safety an integral part of their role.
At Tüpraş, we believe the concept of safety is not the duty of a single group but an obligation that everyone must comply with. We know the ten mandatory safety rules specific to Tüpraş; we implement them and act rapidly to correct unsafe situations. Top management’s commitment to safety can be noticed across the organisation. Importantly, they encourage a culture where everyone feels free to speak up on safety. They also recognise the resources required for safety and, as a result, the most advanced digital technologies are applied at our refinery sites. Our monthly safety meetings are seen as the most important meetings of our company. For me, this is a very valuable and powerful asset. It means there is no conflict in creating a safe working environment and initiating changes needed. Of course, safety isn’t a one-and-done deal. It’s an ongoing process and needs continuous improvement. At Tüpraş, the strong support of our leaders who have complete faith in us means we have a great driving force to make further progress in safety.
Q.
What examples can you give of how safety programmes benefit from innovation and technological change?
Tüpraş continues to prioritise operational safety while meeting our country’s energy needs. In 2023, we implemented the first e-Permit to Work (e-PTW) system at our refineries. This is an exciting first in both Turkey and the energy industry. The e-PTW System is an innovative digital application that supports our sustainable refinery operations, strengthens work safety in production processes, and ensures standardisation in all business processes.
Now that the e-PTW system has been deployed in all Tüpraş refineries, a new era has begun where we can ensure that control of work processes proceed safely and efficiently. We believe that we have adopted good practices in the sector with the electronic work permit, and that detecting unsafe situations has become easier. Another important benefit of this technology is the standardisation of electronic permits to work that eliminate differences and highlight unsafe situations. Workflows between disciplines are more transparent. Because of this, we are now able to instantly view and evaluate risk assessments made by approximately 8,000 refinery employees and contractor employees on site.
We also achieve energy efficiency in vehicles, labour, and transportation services used for permit approvals and paper-based work permits that require physical archives. Such innovations allow us to contribute to a more sustainable future and improve safety and efficiency by preventing possible work losses.
“Creating a safe working environment is vital for a sustainable business model. The safety perspective underpins fundamentals such as operational excellence, sustainability, and communication.”
–Pınar Çağdaş Duran, Technical Safety Director, Tüpraş
Q.
What impact do sustainability, communication, operational risk management and operations excellence have in helping to create a healthier and safer business environment that is better positioned to withstand industry volatility and succeed over the long term?
Creating a safe working environment is vital for a sustainable business model. The safety perspective underpins fundamentals such as operational excellence, sustainability, and communication. By creating healthier and safer working environments, we ensure our employees are cared about, feel better and increase their contribution to the company. Our greatest strength here is communication, an important element that helps cement our bond with employees.
The other important pillar is operational excellence. The best way to achieve operational excellence is through discipline. Achieving operational discipline means consistent adherence to established processes, procedures, and standards. It involves maintaining a high level of accountability across all operational phases. It allows us to minimise risks and exhibit the correct behaviour anytime and anywhere, which is fundamental to creating a safe and healthy work environment. We believe a system built on such solid fundamentals is the only way to achieve a long and sustainable future.
Q.
What are your top three tips for future leaders looking to build a health and safety programme?
As mentioned earlier, being a good role model is the first step. You should lead by example. A good leader needs to “walk the talk” when it comes to safety. They should also be accountable for their actions and learn from their mistakes. A leader’s ability to build a strong team with safety excellence, commitment and passion is essential. Effective safety leaders should promote cooperation, collaboration, and communication as a platform for building mutual trust within teams.
“A good leader needs to “walk the talk” when it comes to safety. They should also be accountable for their actions and learn from their mistakes.”
–Pınar Çağdaş Duran, Technical Safety Director, Tüpraş
Q.
Name the one health and safety initiative you are most proud of and why?
The operational discipline programme we launched last year is a stand-out initiative that is progressing well. First, we launched a study to improve our safety culture and raise the bar on safety levels globally. We conducted surveys and made assessments at our refineries with dss+. We then organised training and safety coaching programmes. As a result, we have renewed and updated our Tüpraş golden rules for safety. We re-launched our safety rules through a communication campaign where our employees’ children gave safety messages. To further strengthen active communication, we regularly organised workshops where we came together with our chief operators. We then updated and implemented our safe system of work campaigns. At the same time, we evaluated all our safety processes from start to finish, created a process safety road map, and started our follow-ups. To maximise employees’ safety awareness, we created a digital dashboard that can track safety performances on an individual basis. Finally, we added a plus to the 5S system (5S+) to emphasise our safer working environment.
Now that we have taken these steps with our operational discipline initiative, we are proceeding with confidence. A cultural change has begun, and it makes me very proud to be a part of this change. I will consider this initiative the proudest experience in my career when it enables us to provide a healthy and safe working environment for our employees that prevents all accidents from occurring.