Pirelli
Pirelli began working with dss+ in 2009 at its tyre production site near Turin in Italy. The 2020 target of the Industrial Plan was for a reduction by 2020 in the Frequency Index of 90% in 2009. In 2016, Pirelli reached an injury Frequency Index (FI) of 0.36 with a reduction of 15% compared to 2015 and 80% compared to 2009.
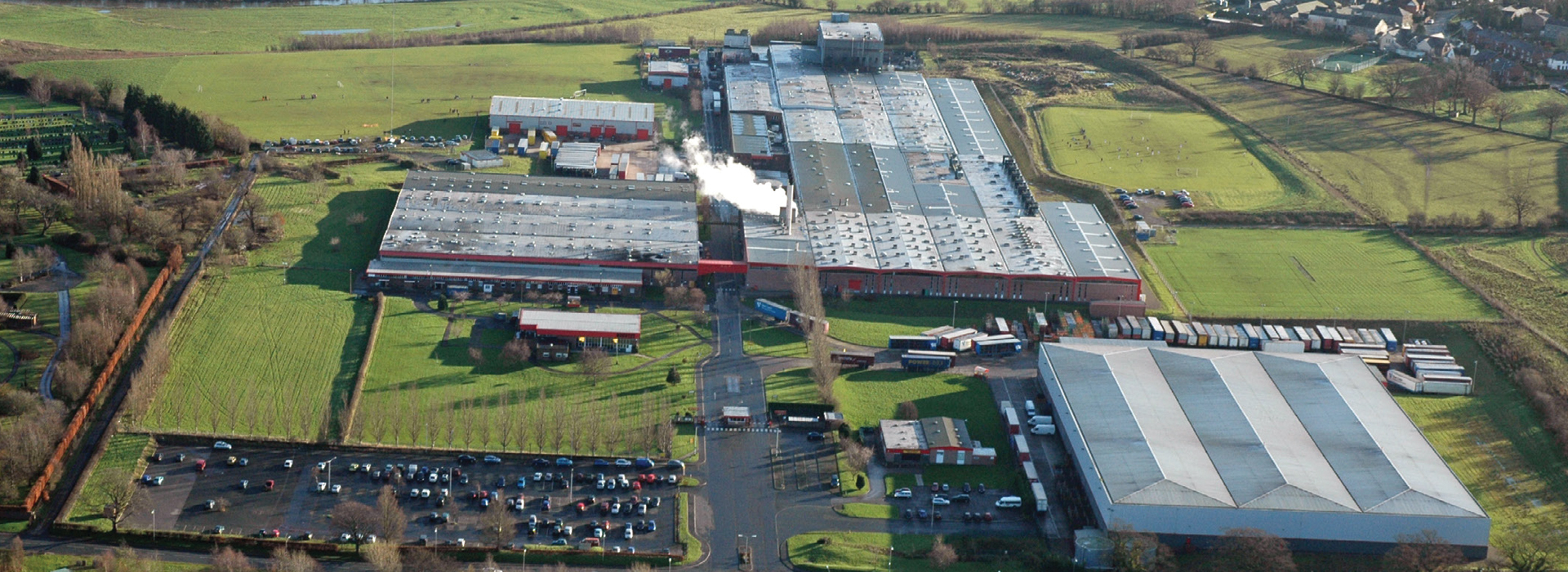
Pirelli in the UK sees benefits of improved safety
A global safety programme with dss+ has led to improvements within Pirelli's UK Industrial System
Between the start of the programme in January 2014 and 2016, Pirelli has:
- Cut lost time injuries by 71%
- Slashed total days lost by 74%
- Reduced the incident frequency by 73%
A programme to tackle safety - globally
Aiming to replicate the Turin site improvements in injury frequency index reduction at its other manufacturing sites, Pirelli contracted dss+ in 2013 to develop a safety cultural change programme - Excellence in Safety - for 13 of its 19 factories worldwide.
From a traditional approach …
Pirelli recognised at an early point the need to focus on safety culture, considering a human approach to safety as a key element to further improve its safety performance in the UK.
As Graham Faulkner, the project manager at Pirelli UK for the Excellence in Safety Programme, says, "We had a traditional approach to safety management, based on standard rule setting and the respect of these to prevent incidents. Yet we clearly realised that most incidents were not caused by machines, but by the behaviour of people. To build on a substantial safety culture then, we had to ensure that accident prevention was a behaviour adopted by all in order for us to improve."
In a first step, dss+ consultants spent a week in January 2014 at the two Pirelli UK plants, located in Burton and Carlisle, interviewing operators, site managers, unions and contractors to get a picture of the safety status quo and identify opportunities for improvement.
There were ways that communications could be improved between the people on the shopfloor and senior management, as well as opportunities to impact on incident prevention focusing on our culture aligned to safety rules.
… to a transformation of mindset
To ensure the new Excellence in Safety programme would not become just another initiative, but a permanent core value, Pirelli spent three years working with dss+ on three key drivers: governance set-up, tools and education to change mindsets and behaviour.
This involved changing the safety management system at Pirelli's UK locations. The new system and structures – such as a central safety committee overseeing all functions in Pirelli UK, task teams that work on specific issues, safety training for employees and safety champions among the workforce – had a significant impact. As Faulkner points out: "We now have a 10-minute safety brief once a week for every shift. That way everybody knows what is going on: how many occasions we had when safety could have been better, what the reason for them was, what action we took. This approach gets safety at the forefront of people's minds and demonstrates that Pirelli management is willing to invest production time in safety."
Changing behaviour
In addition to changing the safety management system, dss+ also provided coaching for Pirelli line management, from senior managers right through to first line supervisors. The aim was to help them be more visible, role model safety and engage with employees on safety through regular visits to the shopfloor, conversations with operatives, audits and recognition of achievements. dss+ believes it is vital for managers to be visible, to establish a dialogue with the people doing the work and to thank them for their contribution.
Pirelli took this on board and changed the way in which it gets people involved. Supervisors are taking the initiative, developing and instigating new ways of working. As a result, shifts are coming up with large numbers of suggestions, which have resulted in significant improvements.
Pirelli's UK Industrial System has also introduced a process for regular behaviour-based safety assessments. The expectation is that everyone – senior management included – carries these out on a regular basis and uses them as an opportunity to talk to employees about safety.
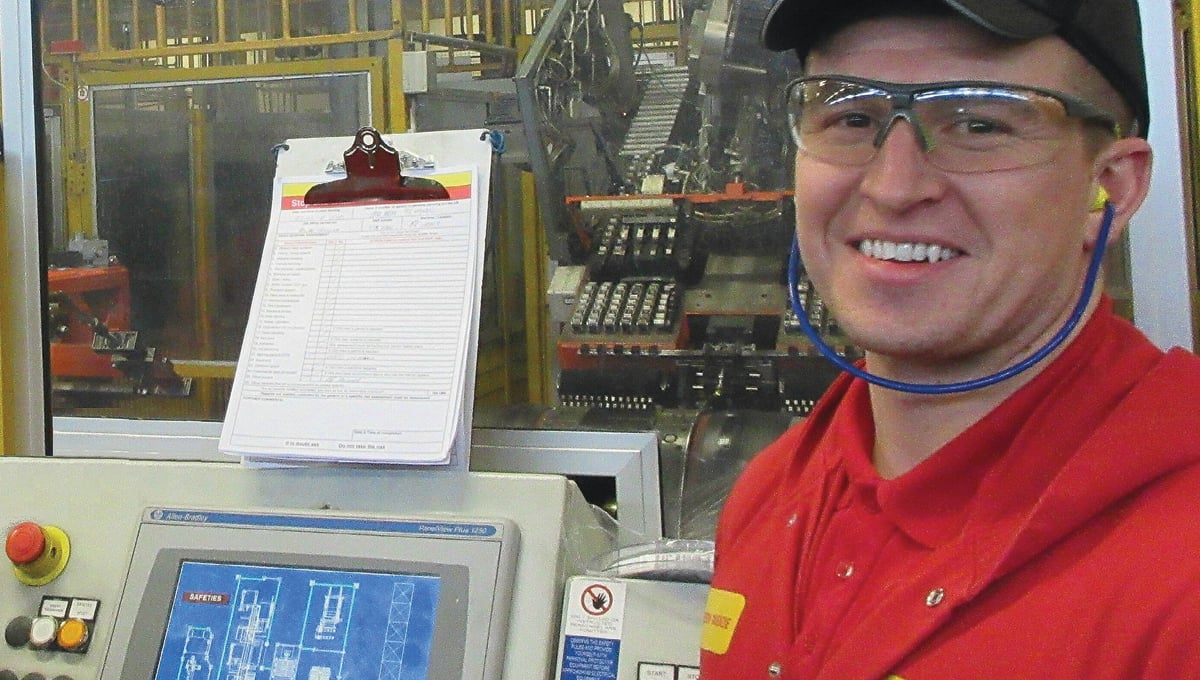
Line management accountability is key
This new approach has resulted in a much faster response to issues. Faulkner can cite some examples that just required small changes to make a big difference, from the installation of guide rails in a palletising area so a machine would stop jamming to the purchase of a knife sharpening device for use in the mixing area so that operatives no longer sharpen their knives individually. "If small, niggling issues are left, they fester and eventually bubble up. It's important to tackle them quickly," he says.
Darren Irving, one of the safety champions who has worked within the Pirelli UK Industrial system for 21 years says, "Safety is like wearing a seatbelt. It has to become automatic."
"We have noticed that at the same time safety has improved, so has efficiency and output."
Ashley Thomson, head of maintenance for Pirelli UK
Seeing the results
Mario Apollonio, UK Industrial Director, confirms that alongside other quality and efficiency programmes, "Our expectation of the Excellence in Safety programme was that it would also improve other indicators such as quality, efficiency and output. The baseline we wanted to achieve was cultural change. We are now, three years into the programme, seeing a shift from a reactive to a more proactive, preventive culture."
Safety is a shared responsibility and Pirelli UK will continue working in this manner towards a goal of zero accidents.