Pragmatic Pathways to Achieving Zero Harm
Driving the Future of Mining Safety: Insights from the dss+ Workshop at Indaba 2025
As Africa’s mining industry undergoes rapid transformation-driven by M&A, technological advancements, and evolving workforce dynamics-companies must adopt forward-thinking strategies to ensure the safety of their workforce. While significant progress has been made in reducing injuries and fatalities, achieving Zero Harm remains an ongoing challenge requiring continuous innovation and leadership.
At the Mining Indaba 2025, dss+ convened senior executives and industry leaders for an exclusive workshop, "Pragmatic Pathways to Achieving Zero Harm." This high-level discussion explored the shifting dynamics of mining safety, the role of digital transformation, and the critical need to embed a strong safety culture across mining organisations and their value chains.
Read the full article for key insights and expert perspectives on pragmatic pathways to achieving Zero Harm in mining.
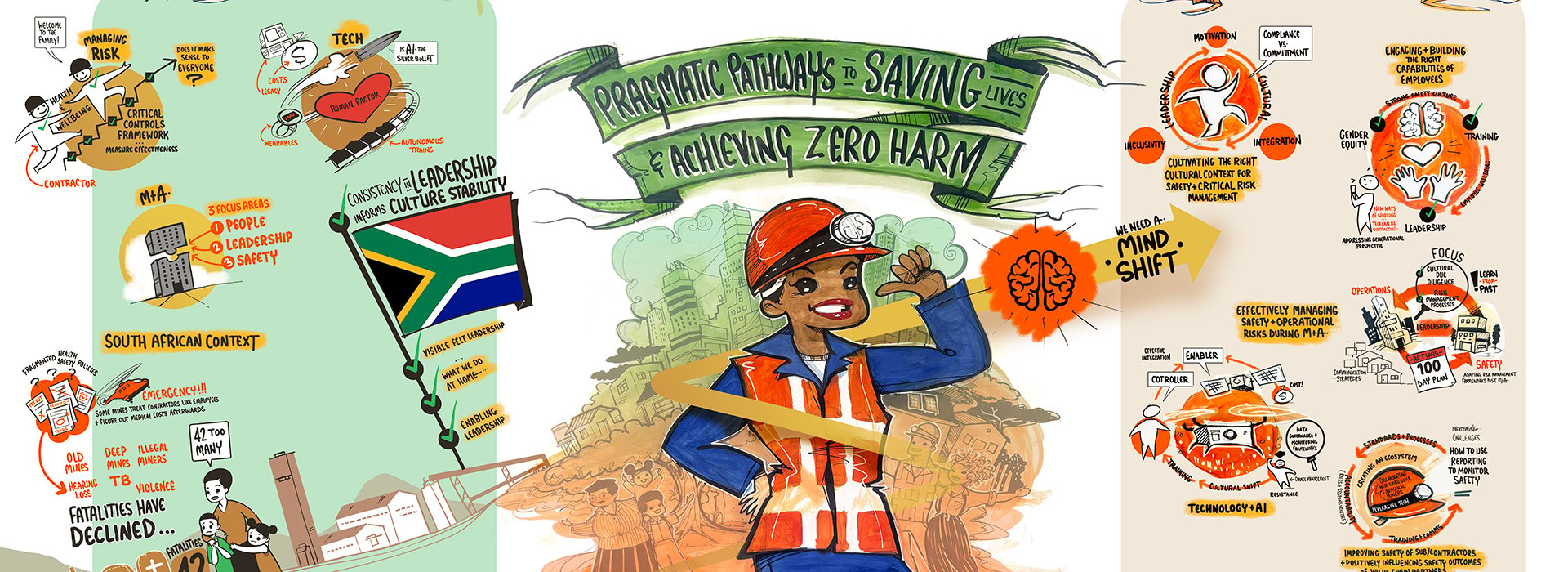
As the mining industry in Africa navigates rapid change – from consolidation through M&A to increasing reliance on contractors and new technologies – the risks to worker safety are evolving in complex ways. Traditional safety approaches are no longer sufficient; companies must now address emerging challenges such as integrating safety cultures post-M&A, ensuring contractor and value chain safety, and harnessing AI and digital tools effectively. At the same time, fostering truly inclusive and psychologically safe workplaces is becoming a business imperative, not just a moral one.
There is no doubt that in the last decade, key players in the African mining sector have been able to show significant progress in curbing injuries through a wide range of initiatives. Indeed, in 2024, South Africa recorded its lowest-ever number of mining fatalities (42 total), alongside a 16% decline in injuries - a milestone that is worth celebrating. Nevertheless, workplace fatalities and incidents persist, mirroring global trends.
Within this context, dss+ convened senior executives from across the industry on 4 February 2025 in Cape Town for an interactive workshop entitled “Pragmatic Pathways to Achieving Zero Harm”, co-organised with African Mining Indaba 2025. The goal of the workshop was to discuss how mining operations are evolving, how this has augmented risk, as well as the challenges and opportunities that companies have in improving their health and safety systems and practices. The workshop featured a panel of distinguished experts and mining executives, covered the latest best practices, and included roundtable discussions on key emerging topics that offered fresh perspectives on how mining companies can stay ahead of the curve in safeguarding their workforce.
Challenges companies face
During the discussion, participants reported a number of cultural, leadership, operational, and financial barriers that hinder progress on workplace safety. Reactive, compliance-driven safety cultures, coupled with a culture of fear and fear of reprisal, were seen as major obstacles to open reporting and proactive risk management. Participants noted that safety was not consistently embedded into organisational culture, and leadership accountability and commitment were often lacking, with safety not always driven from the top. They also highlighted that “zero harm” goals sometimes drove the wrong behaviours, encouraging underreporting rather than meaningful improvements, while productivity-driven targets increased risk by prioritising efficiency over safety.
Operational challenges were also discussed, including poorly integrated safety systems and a lack of risk-based decision-making, which led to inconsistencies in hazard management. Participants observed that competing priorities and the outsourcing of core functions introduced variability in safety performance, while ineffective communication tools hindered the sharing of safety updates and lessons learned. Financial constraints were another key concern, as commodity cycle pressures often led to fluctuating safety investments, and limited capital availability restricted the implementation of stronger safety controls. Additionally, skill retention challenges contributed to the loss of institutional safety knowledge, and some participants pointed to societal attitudes toward the value of life as a factor influencing workplace behaviours.
To address these issues, participants emphasised the need for a proactive, risk-based approach to safety, driven by strong leadership commitment and cultural transformation. They stressed the importance of transparent communication, realistic safety targets, and better system integration. Ultimately, they concluded that sustained investment in workforce development, leadership engagement, and risk-based safety strategies would be critical to achieving long-term improvements in workplace safety.
Panel discussion
The expert panel sets the stage for deeper discussion on how to achieve zero harm in Africa’s mining sector.
Reflections on the state of safety in South Africa
“The mining industry in South Africa has made significant progress, yet lives are still being lost. And, compared to other high-risk sectors like oil and gas, mining lags behind in safety maturity and risk management culture. Achieving Zero Harm requires more than incremental improvements – it demands a fundamental shift in how organisations approach safety.”
- Jaco Pieterse
“Within South Africa, we are on a journey to get to zero harm. We are not there yet, but in 2024, we have achieved the best safety performance on record. One good example is our target on silica dust, exposure to which can increase risk of developing tuberculosis – making it an occupational disease in South Africa. We have reduced exposures by over 80% through strong leadership on a tripartite level and by promoting leading practices among all companies.”
- Dr. Thuthula Balfour
Safety in M&A
“One of the emerging issues that we are increasingly seeing across the mining industry is related to the substantial increase in safety risks during M&A. Differences in safety culture, unfamiliar sites and operations, and misalignment of risk appetite and safety procedures can create confusion. Uncertainty among workers, leadership transitions, and disruptions to established safety systems further elevate risk. That’s why it’s critical to proactively manage safety integration from the very beginning of the integration process, ensuring that a shared culture and clear protocols are established to protect people.”
- Helder Santos
Contractors
“In the mining industry, contractors experience a higher rates of injuries and fatalities compared to regular employees. To improve outcomes, we must ensure that contractors follow the same rigorous safety standards, receive site-specific risk training, and are fully integrated into safety programmes. Regular audits, clear accountability, and strong leadership engagement help reinforce a culture where safety is non-negotiable. This will help to foster collaboration and proactive hazard management, and therefore help to create safer working environments for everyone on site.”
- Helder Santos
“Access to healthcare for contractors remains a challenge. In South Africa this is compounded by fragmentation of compensation systems that can lead to life and death situations. Permanent employees are mostly covered by a private entity, Rand Mutual Assurance, while contractors are covered by the publicly run Compensation Fund. Due to inefficiencies at the CF, some service providers do not accept patients covered by the CF. Injured employees covered by RMA can thus be flown by helicopter to the appropriate private facility, while employees covered by the CF land in the overburdened public service facilities.”
- Dr. Thuthula Balfour
Technology
“At Rio Tinto, we have had much success in introducing new technologies to improve productivity and safety performance. We’ve deployed autonomous trains in Australia, drones that monitor equipment performance and watches that detect fatigue of employees, for example. But new technologies often come with high capital costs, and can be challenging to integrate into existing systems and data monitoring frameworks. And most importantly, you must take a people-centric approach to introduction the new technology.”
- Thabile Makgala
“With both operational efficiency and safety, we see that companies are able to benefit from the introduction of new technologies and AI when they improve the skill sets of front-line supervisors and middle management to interpret the actionable data that such technologies provide, and use it to make the right decisions.”
- Helder Santos
Creating a safe, inclusive working environment
“Creating a safe, inclusive working environment requires real leaders who set the right example, consistently, on a day-to-day basis.”
- Thabile Makgala
“A psychologically safe working environment starts with respecting people and taking away the blame culture. All workers should be empowered to voice when something goes wrong, and to contribute solutions that draw on their day-to-day experience as operators in the mine. It should not be just the supervisor that has a voice.”
- Dr. Thuthula Balfour
How dss+ can help
- At dss+, we are the trusted operational transformation partner for complex and high-hazard industries, committed to safeguarding lives and fostering long-term value release through comprehensive Health and Safety solutions.
- Our integrated value protection and long-term value release strategies empower mining organisations to enhance resilience by securing critical assets through robust risk management frameworks and building trust within the workforce. This foundational approach not only mitigates risks but also drives innovation and growth, ensuring a safer, more sustainable future for the mining industry.
- dss+ employs a risk-based approach specifically designed for the mining sector to identify and mitigate operational risks. We help mining companies prioritise safety and compliance, ensuring the highest standards are maintained while enhancing overall business performance. By safeguarding the most valuable assets— employees and equipment—we build a culture of safety that permeates the entire mining value chain.
- We integrate advanced risk management systems and safety frameworks that promote continuous improvement and enable companies to stay ahead of industry risks. Through our tailored approach, we enhance safety performance across all levels, ensuring that safety protocols are not only adhered to but actively embraced by employees. This proactive approach to incident management and investigation helps companies learn from past challenges and continuously evolve.
- We focus on optimising operational efficiency through cutting-edge digital tools and data-driven insights. By leveraging predictive analytics and real-time monitoring, we help mining companies enhance resource exploration, streamline project execution, and improve decision-making. This results in increased productivity, improved profitability, and the ability to meet delivery timelines and budgetary constraints—all while ensuring that safety remains at the core of operations.
- dss+ also supports mining companies in building capabilities across diverse demographics, ensuring that all employees, regardless of gender, age, or background, feel empowered and psychologically safe to contribute to safety initiatives. We tailor our training programmes to engage employees at all levels, fostering an inclusive and resilient culture that is crucial for sustainable performance.
- Our mission is clear: to save lives and create a more sustainable future for the mining sector. Through strategic partnerships, advanced technologies, and a relentless focus on Health and Safety, we make a meaningful difference across organisational, national, and global levels. By prioritising both value protection and value release, dss+ is leading the way in creating safer, more resilient mining operations that are primed for sustainable growth.
Authors
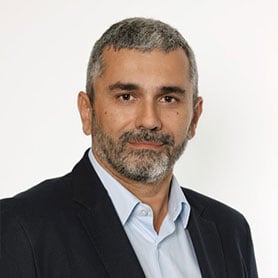
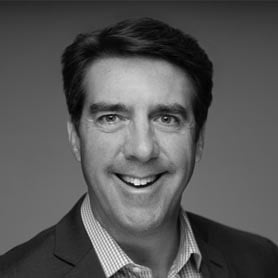
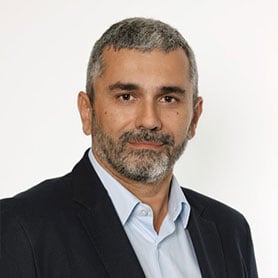
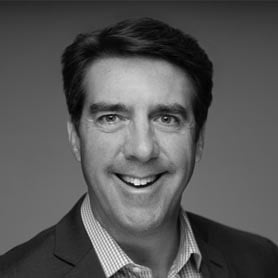