Prioritising Maintenance and Reliability in India's Chemical Industry
As the chemical industry in India emerges as one of the competitive and high-quality manufacturing destinations globally, growing to about USD300 billion by 2025, the significance of maintenance and reliability (M&R) cannot be overstated. M&R are not merely operational necessities; they are foundational pillars that determine an organization’s resilience, reputation and sustainability.
This article was originally published in Chemical Industry Digest. For the full feature, visit their website: ChemicalIndustry Digest.
Introduction
As the chemical industry in India emerges as one of the competitive and high-quality manufacturing destinations globally, growing to about USD300 billion by 2025, the significance of maintenance and reliability (M&R) cannot be overstated. M&R are not merely operational necessities; they are foundational pillars that determine an organisation’s resilience, reputation and sustainability.
Statistics reveal that unplanned downtime costs Indian industrial businesses approximately INR 7 million per hour. While this is lower than the global average of INR 10.3 million per hour, the frequency of such incidents in India is alarmingly high. The ABB survey indicated that 88% of Indian businesses experience unplanned outages at least once a month, compared to 69% globally, highlighting the financial burdenof inadequate maintenance strategies.
Furthermore, insufficient maintenance can result in a 25% loss in production capacity, leading to inefficient resource utilisation and increased waste generation. Companies must recognise that their maintenance practices influence not only their strategic advantages but also their environmental responsibilities.
The situation worsens when reduced maintenance budgets further compromise safety. Over 30% of industrial accidents are attributed to inadequate maintenance, while the trend of outsourcing maintenance work leads to a loss of ownership, knowledge and skills.
This raises a critical question: Are we genuinely prioritising safety, reliability, and sustainability, or merely offering lip service to compliance for short-term gains?
A paradigm shift in M&R practices is essential. Transitioning from a “run-to-fail” approach to an outcome-based maintenance model is crucial. This shift not only addresses the industry’s growing skills gap, operational efficiency but also reduce environmental impact and meet regulatory requirement.
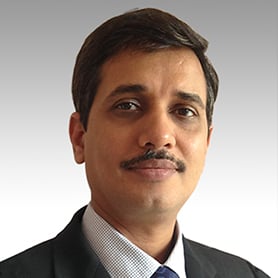
Hitesh Thaker
Principal at dss+ India has over 29 years, including 17 years in the petrochemical industry and 12 years as a consultant and project manager. Hitesh's expertise lies in operational risk management, process safety, and cultural transformation. He is a certified trainer in behavioural safety and process safety management systems.
Shifting Mindsets: From Reactive to Proactive
A prevalent issue within the chemical industry is starkly illustrated by widespread maintenance deficiencies observed across multiple organisations. The fundamental absence of basic Preventive Maintenance (PM) or Predictive Maintenance (PdM) approach reflects a deeply entrenched tendency to prioritise production over maintenance, resulting in increased safety risks and equipment degradation.
At dss+, our philosophy firmly asserts that all injuries and incidents can be prevented through proactive measures and robust maintenance practices. However, we observed that the lack of systemic approach, leading to unreliable operations, creates a challenging environment for establishing and maintaining this core belief.
Here are some of the gaps and challenges seen:
- Systemic Maintenance Challenges: While leading firms have embraced predictive maintenance through advanced analytics and IoT technologies, many facilities operate with minimal attention to M&R, focusing solely on meeting statutory requirements. This disparity is particularly concerning when business-critical equipment operates without proactive risk management or Failure Mode and Effects Analysis (FMEA), leading to unscientifically defined spare inventories and inspection protocols.
- Cultural and Operational Gaps:The pervasive “firefighting” mentality generally observed highlights a critical need for cultural transformation. Organisations often under cost pressures, reduce the maintenance budgets and treat inspections as mere formalities. Outsourcing of maintenance activities to contractors may have helped organisation in short term, however the quality of assets upkeep and overall cost of operations generally is seen to go up with time as contractor move their skilled labours to other clients. This reactive approach undermines the potential for genuine improvement and continuous enhancement.
Successful leadership support in executing risk-based M&R programs often faces challenges due to low confidence in the program’s design. Doubts can hinder the execution of M&R priorities even when identified as critical. To overcome this challenge, a twofold leadership strategy is required: building confidence in the M&R program and ensuring full leadership commitment behind it. Leaders must acknowledge the need for robust risk-based M&R programs and challenge any doubts about their technical justification during the design phase to increase confidence and commitment.
Skill Gaps
A significant challenge facing the industry is the skill gap among professionals trained in maintenance and process safety practices. As technology progresses, workforce capabilities must evolve accordingly. Outdated training methods and insufficient investment in human capital leave organisations vulnerable to operational failures.
Quality and Safety Integration
Quality assurance processes, vital for maintaining product integrity and safety, are compromised by these systemic maintenance issues. The lack of proactive risk management and structured maintenance systems indicates that organisations are merely meeting minimum standards rather than fostering a culture of excellence. This approach creates a dangerous cycle where maintenance deficiencies directly impact product quality and safety standards.
To break this cycle, the industry must embrace a critical mindset shift. This transformation involves addressing the above gaps and recognising that reliable operations and comprehensive maintenance strategies are not obstacles to productivity, but rather essential foundations for sustainable, safe, and efficient operations.
Organisations must move beyond compliance-focused approaches to embrace comprehensive maintenance strategies that integrate safety, quality, and operational efficiency.The gap between industry leaders and laggards needs to be reduced by further collaboration.
Strategic Imperatives: A Risk-Based Approach
Adopting a risk-based approach to M&R is crucial for balancing safety, operational, and reliability objectives. This strategy protects operational assets and personnel from safety/process safety risks while ensuring that equipment meets or exceeds its nameplate production performance during its operating life.This approach aligns with the dual goals: “Minimisation and management of risks” and “Maximise Value Creation.”
Processes and systems are developed to integrate key monitoring elements through KPIs for barrier health, effectiveness tracking, and red flag monitoring, ensuring systematic performance evaluation at all organisational levels.
The framework is supported by three crucial pillars:
- The Technical Model establishes standard tools and practices driving focused operational risk reduction, answering the critical question “Where’s the$$?” through systematic evaluation of maintenance functions, downtime prioritisation, and implementation of Root Cause Failure Analysis, and Failure Mode and Effects Analysis methodologies.
- The Capabilities Engine ensures the right skills and effective coaching on operational risks, emphasising teamwork, problem-solving capabilities, and robust training programs for frontline capability building.
- The final pillar addresses mindsetsand behaviours, aligning the organisation with operational risk reduction objectives through sustained leadership rituals, reliability focus, and cultural transformation.
- This holistic approach balances the dual objectives of risk minimisation and value creation, ensuring that processes, technical capabilities, and organisational culture work in harmony to not only ensures safe and reliable operations but also optimises resources and maximises return on investment.
A Clarion Call to Action
A holistic approach to maintenance and reliability by fostering a culture that prioritises these elements are key for organisations to redefine operational standards within this vital sector.
By adopting risk-based maintenance and reliability (M&R) programs that balance safety with operational objectives, leaders can navigate risks effectively while driving sustainable business performance improvements. These programs enable companies to optimise resource utilisation, minimise waste generation, and reduce energy losses - all of which are crucial for meeting sustainability targets.
As we transition into 2025, let us challenge ourselves to bring a step change in our approach to maintenance in order to attain sustainable growth— an ethos that must resonate throughout every level of operation within India’s chemical industry as we navigate increasing global competition and scrutiny. Beyond compliance, it is for genuine transformation-a chance to build an industry where safety is paramount and both operational excellence and sustainability are integral to everyday practices.
Source
- chemicals market: India’s chemicals market to hit $29.7 bn in 2024, set for steady growth with 3.26% CAGR through 2029 - The Economic Times
- India’s Booming Chemical And Petrochemical Industry-Understanding Industry Landscape | Department of Chemicals and Petrochemicals
- ABB survey reveals unplanned downtime costs INR 7 million per hour
- Industrial Accidents: Rise in industrial accidents in Vizag a cause for concern | Visakhapatnam News - Times of India