Productivity Gains through Digital Turnaround Management
Turnarounds are regarded as a necessary evil by most of the hydrocarbon processing industry. They are costly, time-consuming, and complex, yet unavoidable if the maintenance and reliability of a plant are to be guaranteed. Everyday operations are shut down means a loss in revenue. Despite such high stakes, turnarounds regularly overrun both schedules and budgets. While a typical turnaround window ranges from 24 – 36 days, the reality is closer to 40+ days. Tens of millions of dollars or an entire year’s maintenance budget can be eaten up in a matter of weeks.
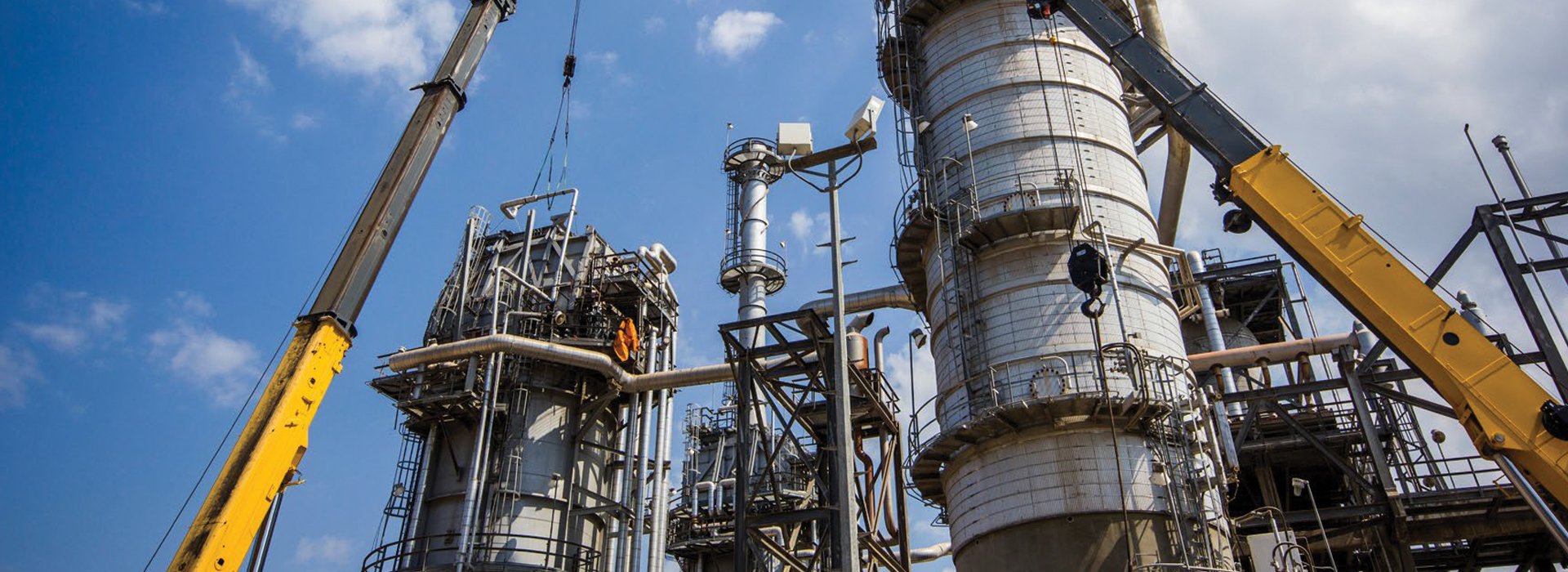
There are many familiar reasons for poor turnaround outcomes from inadequate preparation to lack of execution oversight, unreliable asset data, delayed inspection reports, missing materials, and extensive contractor involvement. The number of on-site personnel during a turnaround can triple or even quadruple. If turnaround managers do not have a good overview and access to reliable information, it is easy to lose control.
Digitizing the turnaround process allows plant operators to keep a tighter grip on the project, facilitates the management of large numbers of people unused to the site and way of operating, and significantly improves performance and therefore productivity.
On average, the implementation of digital turnaround management saves:
- 20-40% in cost and
- 15-25% in schedule reductions1.
There are several elements to digital turnarounds that account for these optimisations:
- Enhanced performance monitoring, e.g. through real-time mobile dashboards, mobile web-based interfaces to report hours, HSE, and progress;
- Predictive modelling using field data to more accurately define scope;
- More accurate scheduling through Wi-Fi or LTE-linked tracking of people, materials, and equipment;
- Integration of project systems with emergency response plans;
- Greater asset security through improved monitoring of equipment, contractors, and sub-contractors;
- Foundational data management that hones in on key facts and extracts value from the floods of data generated by smart technology;
- Improved knowledge retention through gamification, AR/VR, and over-the-shoulder coaching via video stream.
In this paper, we discuss the benefits and pitfalls of digital turnarounds that have resulted in optimal turnaround planning and execution.
Digital planning tools for optimised turnarounds
Turnarounds are planned shutdowns scheduled to allow plants to maintain, revamp or replace equipment or entire process units. The aim is to ensure the reliability and performance of plant assets in order to avoid costlier unplanned shutdowns due to equipment failure. Considering the complexity of the work involved, the tight time frame, the number of interfaces, and the substantial manpower, largely made up of contractors unfamiliar with the assets, the amount of information that has to be digested, analysed, and acted on is vast. This is where many turnarounds fall down. It is not deficient technical knowledge, will, or effort that leads to projects overshooting schedules and budgets. And in most cases, it is not extreme weather events or unexpected disasters either. It is a lack of control, often due to missing, timely, reliable information be it about the condition of equipment, the status of work completion, or the actual location of material or people.
“Lack of control, often due to missing, timely, reliable information, is the most common cause of turnaround project overruns.”
While the hydrocarbon processing industries today employ a wide range of operative digital tools from sensors to historians, distribution control systems (DCS), computerised maintenance management systems (CMMS), PIMS software, LIMS as well as smart PPE, few use digital planning tools that allow them to capture, interpret and benefit from the data these systems generate. Digital has the ability to change that and give turnaround managers the information they need when they need it, from readiness to progress dashboards, per day margin savings or loss analyses, and information on actual rental equipment needs.
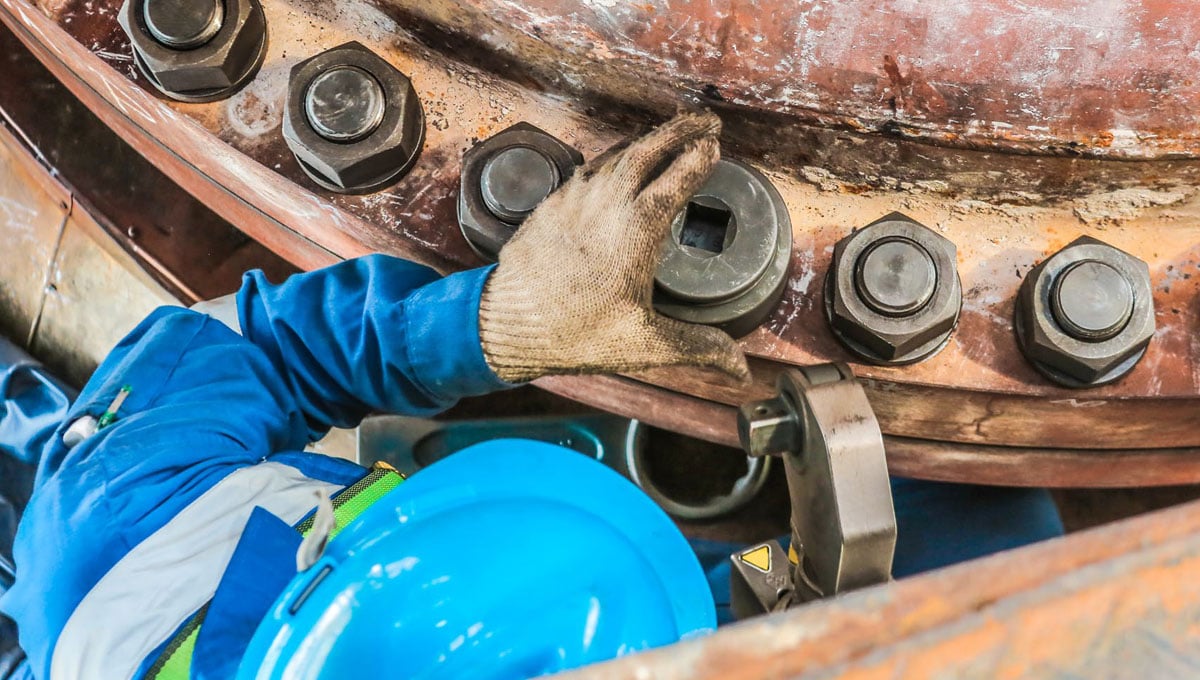
Digital already provides support for the front-end of the planning process in the form of work pack development, and round-the-clock remote schedule programming based on data and images captured from mobile devices. Cloud-based and open-source predictive data management platforms collate and analyse data collected from a wide range of sources including inspection reports, AI, robotics, smart PPE, sensors, digitized permits to work, and maintenance logs. This information feeds into predictive models, which can provide a more accurate picture of the true scope of a turnaround.
At the same time, digital allows for monitoring of productivity in the field and permits fast intervention. Mobile devices are used to capture field data, produce real-time progress dashboards and enable remote support in the field, thus making it possible to reduce unproductive times when workers have to wait or search for equipment or information. Contractors who do not know where to find answers to their questions about how to perform a task or who do not want to ask for help because they want to avoid waiting can be supported by remote experts or digital standard operation procedures (SOPs). While this may seem an inconsequential issue, the cumulative loss of time, procedure compliance, and quality control is significant. And instant support of contractors also cuts down on potential damage to equipment due to incorrect use. With the vast number of subcontractors on site, asset integrity can easily suffer resulting in fires, leaks, spills, etc. Instant capture and reaction to field data not only ensures no time or information is lost during long and sometimes tiring shifts but contributes to improved project outcomes.
Another area where digital planning supports faster and more cost-effective turnarounds is by integrating the vast array of commonly used systems into a single platform. Permits, maintenance histories, inspection logs, repair sheets, off-site repairs, spare part inventory, material procurement information, and schedules can generally not be viewed in a single system. Buried in a blizzard of paperwork, spreadsheets and databases is critical information that is difficult to identify and retrieve. When reported, there is often no guarantee that the information is up-to-date or accurate. By contrast, digital, cloud-based platforms can provide an integrated, low-cost overview of up-to-the-minute records, allowing for informed, timely decision-making.
“Instant support of contractors cuts down on potential damage to equipment due to incorrect use.”
Simplified, reliable turnaround execution
But the benefits of digital turnaround are not limited to the planning stage. Digital can also completely transform turnaround execution. Most turnaround managers currently have to deal with out-of-date, unreliable information. If they have to wait until the next morning’s shift to find out what has happened to equipment, materials, and contractors the day before, they are already behind. Take headcount and compliance, for example. Generally, available data is a day old and hard to verify. Wireless track and trace solutions can address this. They allow for monitoring of equipment and workforce location at any given time and are easy to introduce on mobile phones using GPS or Bluetooth, in the form of an ID chip on employee or contractor identity cards or as an RFID tag on material or equipment. That can be handy when managers want to assess the actual need for rental equipment, for example, and allows them to cut costs if equipment such as bundle pullers or cranes, for example, are not in fact being used or needed. At the same time, wireless tracking of material can reduce turnaround delays by 2-3 days. Imagine no longer having to phone through long lists of the material required by vendors or being able to follow the status of equipment returned to the OEM for repair simply by logging onto a website. Employed for these types of tasks, digital tracking can save 35-50% on time caused by delays in equipment repairs.
Track and trace solutions also provide real-time data on how many contractors and employees are listed on the workforce reports, and who is on-site, and can display that information by qualification, contractor company, total hours worked, break times, etc. An analysis of mass employee movement in comparison to the shift pattern makes it possible to identify and eliminate process inefficiencies. Turnaround managers are able to identify and address patterns that cause delays using simple visual analytics dashboards.
Digital turnarounds are also set to change daily progress and vendor meetings. With progress information based on digital reporting calculated using permit issue times, location data of contractors, and equipment cross-referenced with the turnaround schedule, turnaround managers will have progress information at their fingertips and will also be able to analyse contractor and vendor performance in real-time in all areas. Operators who have introduced forms of digital progress reporting cut times pend by an average of 40-50 minutes per worker per 12-hour shift, while the introduction of e-permits to work can save 20-30 minutes per employee per 12-hour shift.
“Digital turnarounds can significantly reduce inefficiencies, as well as cut turnaround time and cost by more than a third if tools are matched to site-specific needs.”
Conclusion
On-time, on-budget turnarounds are rare and usually only achieved if operators have all the necessary information, the required equipment, materials, and manpower on hand at the right time. In the hydrocarbon processing industries, 90% of turnarounds are routinely over budget, over time, or do not achieve their quality target. Labor productivity of 40% is commonly tolerated and considered hard to improve. That is largely because the root cause is a lack of control due to inaccurate or missing information. Digital turnarounds can significantly reduce these inefficiencies, as well as cut time spend and cost by more than a third. A note of caution though: digitizing turnarounds is only effective if the tools employed fit the status quo and match site-specific needs. They are enablers for process optimisation, not an automatic fix in themselves. There are many solutions on the market. Operators, therefore, need to be clear about what they want to achieve and need to build an integrated, holistic system instead of being tempted into buying individual gadgets or technology solutions that do not work together. An assessment of needs can highlight focus areas where digital solutions can offer fast, cost-effective support and be integrated into existing management systems to create substantial added value.
“Digitising turnarounds is only effective if the tools employed fit the status quo and match site-specific needs. They are enablers for process optimisation, not an automatic fix in themselves.”