Successful Integrated Operations: Mining + Smelting
dss+ has identified the top five challenges facing integrated mining operators in Indonesia, offering insights on addressing them for sustainable and resilient operations.
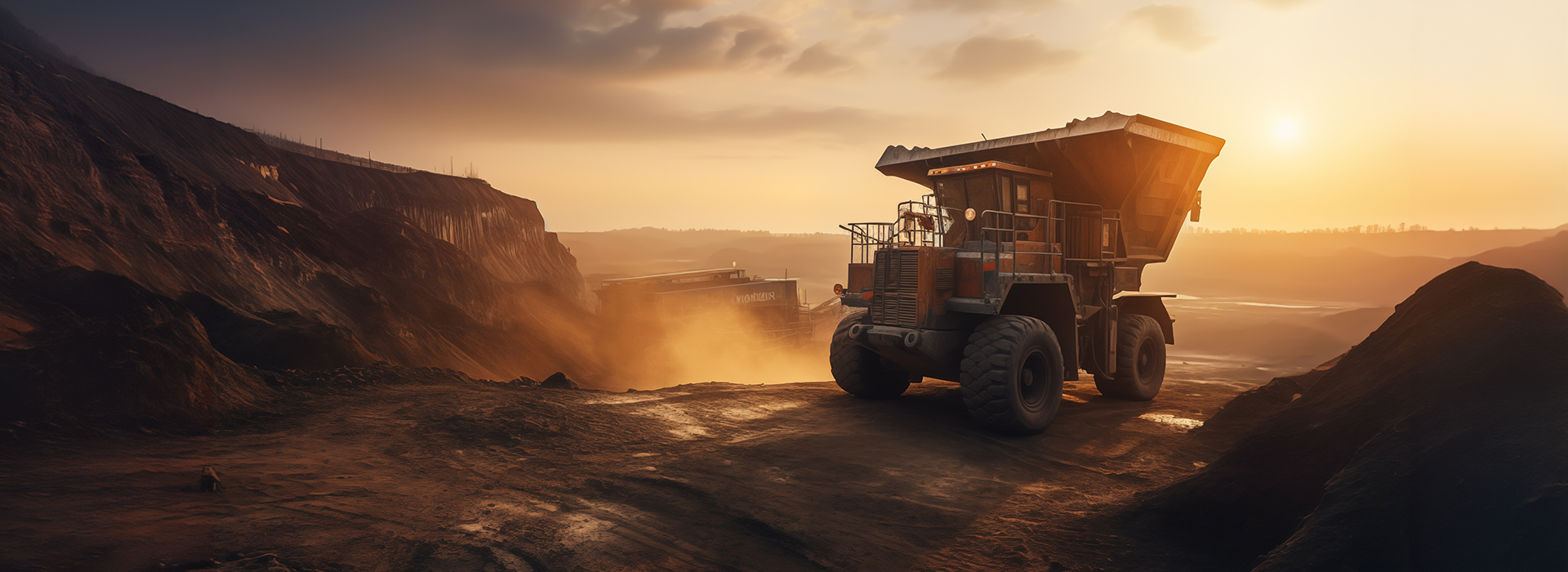
Context
Indonesia’s decision to ban export of mineral ores has resulted in a rapid influx of investment. In 2012, Indonesia had 3 smelting facilities. By the end of 2023, this has grown to 54 units, with the majority coming online within the past 3 years. In 2024, 16 additional smelters are expected to be completed, for a total investment of US$11.6bn.
For companies with core operations in mining, the addition of smelting facilities represents a major shift. This involves approximately 30% of smelters in Indonesia. This transition requires an overhaul of both operating and business models. Early identification and effective resolution of challenges is crucial to avoid delays in time-to-market and ensure full value realization. Companies that successfully execute this overhaul will be better positioned to seize further opportunities downstream in the industry.
Leveraging its global experience and local presence, dss+ has identified the top five challenges for Indonesian’s integrated mining operators. These are discussed below along with dss+ perspectives on how they could be addressed to ensure sustainable and resilient operations.
Challenges
More Complex Commissioning Process
Smelting operations are significantly more complex than standard ore processing due to strict operating conditions, the required quality of raw materials, and molten metal management for safety and efficiency. The use of imported technology requires a skilled workforce, extensive knowledge transfer, and continuous training. Additionally, a reliable power supply and effective energy management are essential to support the energy-intensive nature of smelting and ensure successful commissioning.
Broader Operational Risk Profile
Operational risks in mining are typically related to activities and equipment. Adding a smelter introduces complex process risks. For example, furnace rupture can cause catastrophic damage, including multiple fatalities and significant operational disruptions. Given the potentially severe consequences, and despite their low frequency, managing these new risks requires strict safety protocols and vigilant oversight.
Limited Supply of Skilled Labour
With the increased complexity that comes with the introduction of smelting operations, there is an increased need for operational personnel that have the skills and education to manage these facilities. With a mean year of schooling at 8.8 and less than half of the working age population having upper secondary education or higher (compared to an OECD average of 80%), Indonesia faces a limited supply of skilled labour to build, operate, manage and maintain integrated mining and smelting facilities. This shortage is exacerbated by the rapid growth of the smelting industry. For organizations operating integrated operations, the challenge lies in developing strategies to upskill and retain talent effectively.
Integrating smelting operations with mining
The introduction of smelting operations into existing mining activities introduces critical integration points that impact the overall value chain. For example, at the interface between mining and smelting, quality and specifications of blended ore that feeds the furnaces become crucial parameters for maintaining productivity. A robust Sales and Operations Planning (S&OP) process is essential to manage these and other critical points effectively, and to coordinate resource allocation and production scheduling to ensure smooth integration. Additionally, distinctly different operational cultures within smelting facilities and existing mining operations add complexity and potential for conflict. Strategic coordination and consideration of workforce cultural barriers and differences is vital to navigate challenges and maintain productivity.
Greater Sustainability Impact
Energy-intensive smelting operations not only result in higher emissions but also demand comprehensive energy management and monitoring strategies. Beyond routine sustainability reporting, operators may face environmental taxes and stringent emission reduction mandates. Additionally, the increased use and variety in raw materials, additives, by-products and processing wastes contribute to operational complexity, intensifying the challenges of sustainable practices. Consideration of the integrated upstream and downstream Scope 3 emissions impacts is also important, as the climate considerations that were once left to third-parties and customers becomes the responsibility of the integrated mining and smelting organization.
Ensuring Successful Integrated Operations
Proactive Planning and Risk Management:
Initiate comprehensive planning to manage the risks and challenges associated with integrating smelting operations into the existing mining operations. Perform an early Operational Risk Analysis to identify and mitigate points of potential disruption, particularly those related to critical integration points, such as ore blending, climate impacts, and differences in operating culture.
Readiness-to-Operate (RTO) Process:
Develop a robust RTO process that extends beyond technical equipment readiness to include full operational preparedness. This should cover verifying readiness of the facility across the complete asset lifecycle from construction to operations to maintenance and even decommissioning and disposal. Readiness-to-Operate considerations should include institution of energy management processes and governance, resilience procedures and mitigation measures to manage climate change, and management of changes introduced through new technologies and equipment.
Infrastructure and Organizational Support:
Assess and prepare the infrastructure and organizational structures to support the integrated operations. This includes setting up systems that align with environmental, safety, and governance (ESG) standards and ensuring the organization is structured to support the new operational demands.
Workforce Development and Knowledge Transfer:
Address the challenge of a limited supply of skilled labor by focusing on intensive training programs and knowledge transfer from international experts to local staff. This ensures the workforce is quickly brought up to speed with the new technologies and processes introduced in the smelting operations.
Cultural Integration and Engagement:
Cultivate a cohesive and interdependent operating culture between existing mining operations and new smelting facilities. Engage the workforce early in the integration process to foster this culture, focusing on risk management and leadership development to support the high-risk environment.
Operational Excellence and Quality Control:
Implement a Management Operating System (MOS) and establish Service Level Agreements (SLAs) to ensure consistent quality of input materials like ore concentrates and maintain high operational standards. These agreements help manage expectations and quality across the value chain from mining to smelting.
Safety and Compliance Systems:
Conduct Process Hazard Analysis (PHA) and establish a comprehensive Process Safety Management system tailored to the unique risks of smelting operations. Ensure that Environmental Management Systems, recording and reporting processes are in place to enable corporate, regulatory and local compliance. These systems should integrate all occupational and process-based safety and environmental risks to comprehensively enable management of all potential risks.
Take Aways:
- Identify potential challenges early for proactive planning and risk management.
- Conduct comprehensive RTO assessment, including evaluating supporting infrastructure and organizational readiness.
- Involve operations in turnover early, preferably before construction completion.
- Engage the workforce and leadership to foster a cohesive operating culture.
- Focus on managing process-based risks to ensure operational safety.
- Plan strategic workforce upskilling to address skill shortages.
dss+ contact:
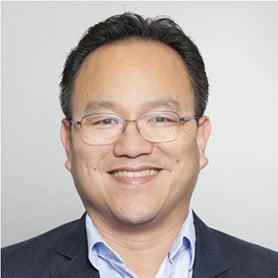
Alfonsius Ariawan
Mining & Metals Lead – Indonesia
+62.821.1205.0945