Teijin Films
DuPont Teijin Films (DTF), a joint venture between DowDuPont and Teijin Limited, is the world’s premier producer of polyester high-value-added film with unique functionalities and related services. The group specializes in film products for the specialty, industrial, packaging, automotive, advanced magnetic media, photo systems, electrical and electronics markets, and many more products that are essential in modern life. DTF is recognized for its market leadership and product innovation and is constantly inventing and developing new uses for its products, including MYLAR® brand, MELINEX® brand, and TEONEX® brand films.
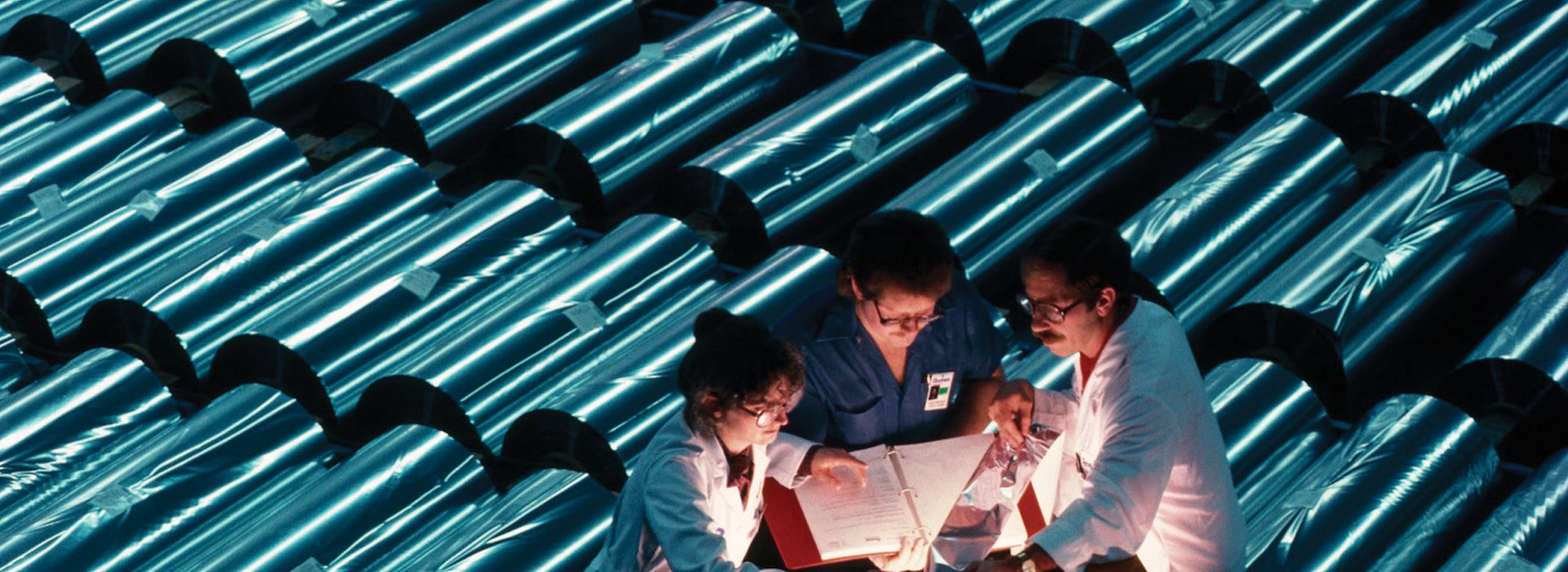
A renewed focus on risks, involving the people who do the work, stopped an increase in serious injuries at DuPont Teijin Films Hopewell plant.
Since its development by DuPont in 1952, polyester film has become part of everyday life. This heritage of innovative and high-quality films has been built through research, expertise, and true collaboration with customers. These brands comprise the broadest portfolio of any films supplier in the industry and have earned the trust of customers and consumers across the globe as the industry standard.
The innovation, performance, quality, and value of the brands of DuPont Teijin Films are also the result of the spirit of teamwork among employees as they continue to push the boundaries of science to help their partners and customers achieve remarkable success.
Hazards had become like wallpaper
DuPont Teijin Films has a long tradition of safety at work. However, in 2016, two lost time injuries occurred after years of zero incidents at the company’s Hopewell, Virginia plant site.
With the help of dss+, a customized approach was designed to first identify and understand the risks in the workplace, and then create solutions to mitigate those risks. But according to Mark Allen, the Hopewell plant manager, "The key to success was our site’s commitment to involve the people who do the work in the solution."
Allen and the Hopewell leadership team had observed that, "Many of our people have been here so long that hazards are like wallpaper to them… they’re not seeing things as they really are, or they have unconsciously developed habits which protect themselves, but may not be passed along to newer personnel." The manufacturing of polyester film includes extrusion, stretching, and winding processes that involve large drums, rollers, and other heavy automated and mechanical equipment. By not fully paying attention to the risks, employees can find themselves exposed to hazards that can result in not only numerous minor near misses but also serious injury.
According to Jeff Stanfield, DTF Global Manager of Human Resources, the sudden and quick succession of two work injuries prompted Hopewell management’s decision to seek an outside perspective to help them understand higher-level risks and get the tools to manage the risks safely.
They engaged dss+ not only for their extensive experience in assessing and improving workplace safety culture but for their success in assisting organizations worldwide in their safety journeys based on several proven principles, including :
- All injuries and occupational illnesses can be prevented.
- People are the most important element in an effective safety program.
- All employees are responsible for their own safety and for the safety of their colleagues
- The entire management team has special responsibility for preventing injuries.
A customized and proactive design for sustainable risk mitigation
Following initial discussions with plant leadership, the dss+ team developed a customized design for the Hopewell site with four objectives:
- Involve workers to create awareness of hazards.
- Identify as many hazards as possible.
- Create meaningful risk reductions that last.
- Create a process that is sustainable.
The team of dss+ consultants implemented their approach by first conducting a series of workshops with a cross-section of the 400 workers at the site. Conducted over three months, the workshops were designed to build risk sensitivity by first identifying hazards and quantifying risks, then prioritizing the risks and determining how to reduce them, and finally on how to best track progress. The dss+ team also used the dss+ Safety Perception Survey™ to gain insights into the culture of the facility.
According to Jeff Stanfield, "With dss+ coaching and leading the facilitation of our workshops, we used a diverse cross-section of our organization to include multiple perspectives and make a deliberate effort to get the key nuggets out of our Safety Perception Survey. We spent a lot of time with the workshop groups to pull out themes and focus on our safety culture, first as leadership, and then on the entire employee group."
"The key to success was our site’s commitment to involve the people who do the work in the solution."
Mark Allen, Manager, DTF Hopewell Plant
Workshops opened our eyes to where we fall short
Marcus Eaton, a slitting operator at Hopewell, participated in the workshops and shared, "It was hard work opening our eyes to where we fall short and how to fix it. After our second day of workshops, it became apparent that people didn’t understand the full flow of our work process. dss+ brought fresh eyes to our operation because we had become set in our ways and we were taking shortcuts in our danger zones."
Eaton added, "dss+ helped call out to the rest of the plant what the risks were and identified what’s missing. They were fun and efficient to work with… they invited us to speak our minds and to highlight what is wrong. The best part of the workshops was that participants were from every different part of the plant and they shared what goes on in other parts of the plant. So we all gained a better appreciation and understanding of where and how we work. People are now really more aware of the goal of keeping everyone safe."
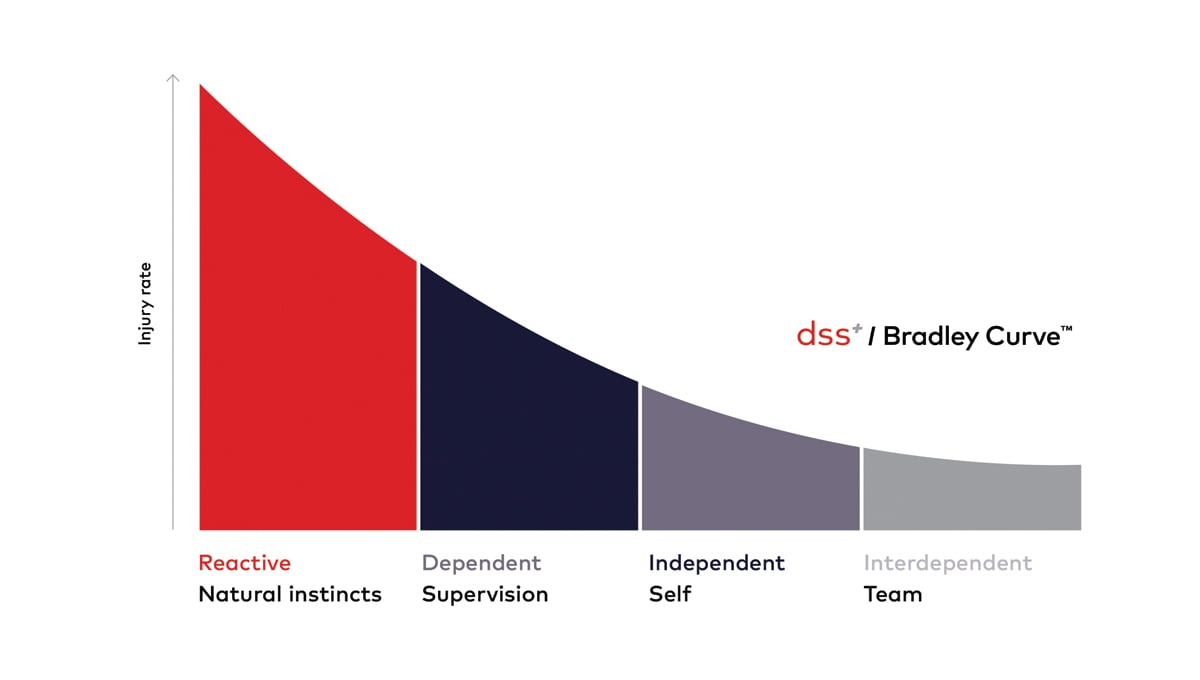
Moving from a dependent to an interdependent safety culture
In the past, the safety culture at Hopewell was one that relied on individuals to perform safely. According to Alice McClure, the Safety & Environmental Health Manager at the Hopewell site, "We were a very dependent culture. By using the data from the dss+ Safety Perception Survey™ and input from our workshops, we realized we weren’t involving the right people to drive the culture to become interdependent."
dss+ Bradley Curve™
Jeff Stanfield added, "The key has been to ‘involve the people who do the work’. We identified several clear principles to help drive our culture to an interdependent culture. One is, ‘We Understand Why’. The power of understanding is apparent when we see our teams working together to make things safer… to understand and then change the process that caused an accident."
Stanfield believes, "At the end of the day it is all about employee beliefs. What we believe is what we do. Smaller groups of employees and individuals are responding very favorably to the changes. As a result, we have reduced our levels of risk. Finally, we are all recognizing that there is a level of risk in everything we do."
Value of dss+ to DTF
The team at Hopewell turned their findings into eight site principles or safety values that are posted everywhere. Alice McClure, the Hopewell site SHE Manager, shared, "We are finding full engagement of all employees more difficult than anticipated. We can engage people who work the day shift, but we need to refine our approach, so this occurs on second and third shift as well. Site leaders are really beginning to prioritize talking about risk reduction with their employees."
According to McClure, some of the key deliverables of the dss+ engagement included:
- A comprehensive database of hazards and risks developed for DTF
- Safety goals and results articulated for 2017
- Risk reductions status reporting established
- Risk Reduction training module created for the site
McClure also shared, "dss+ gave us options for their support as we continue our safety journey. We are embarking on a huge cultural shift in how we work together. Results indicate there are pockets of behavior where we are working really well."
Jeff Stanfield added, "We would not have made these strides without dss+. They were more than just an objective set of eyes. Their level of coaching was fantastic, even on phone calls. The power of someone asking you the right questions and then turning it into concrete actions is so valuable to us."
Sustainable performance was a key design objective
dss+ worked with the Hopewell team to not only create the right tools for immediate risk reduction at the plant, but to also integrate and embed a sustainable process into the organization for the long term. The engagement was designed from the beginning to deliver sustainability by:
1. Building Risk Reduction Capabilities
dss+ trained the DTF workers on how to use the tools, and worked with them as they undertook their first risk reduction projects. The site team is working on further developing their internal capabilities to continue training and supporting workers going forward.
2. Adjusting Organizational Structures to Support Risk Reduction
Eighteen organizational Risk Teams were chartered in early 2017, and they established Risk Reduction goals for the year. The year-end data in the nearby chart demonstrates that Hopewell has been successful in sustaining its risk reduction efforts.
3. Changing the Culture of the Organization
Deep seated tendencies and work habits are hard to change. But site leaders understand that the workers must be involved, so the plant management team is learning how to create opportunities to not only engage, but fully involve the workers.
The eight Hopewell site principles are a foundation to help guide the organization to improve its safety culture.
2017 plan for risk reduction efforts at Hopewell site
- The site set a goal of having 175 risk reduction controls or mitigations in place. They beat that goal installing 187 in 2017.
- The average risk reduction obtained on risks where all of the control or mitigations are in place was about 75%.
- Another site wide goal was to analyze 229 risks in 2017. The site fell just short, completing 195 risk analysis. There was a conscious effort to emphasize quality of analysis over just "checking the box".
- Teams completed risk reduction work on 60 of the highest risks on site. New or improved controls or mitigations are in place for dozens of other risks, which have additional controls yet to be implemented.
Recently, the site has been working on a new 2018+ Risk Reduction Vision to define what they want to do even better. Teams will be re-chartered, and 2018 goals will be set. Next steps include addressing several of the remaining high risks that have not yet been reduced. Efforts are also underway to drive to completion specific high-risk projects as an improvement goal for 2018. As Alice McClure observed, "We took what we learned in 2017, and involved a cross- functional team to define what worked and what we need to do better. The Vision fell out of that effort and shaped the direction for 2018."
Stopping a trend with a new way of thinking – Safety vs Risk
In the 15 months since dss+ began working with DTF, the Hopewell site has not experienced any Lost Time injuries. While the site worked hard to minimize the chances of additional serious injuries on their own, plant manager Mark Allen believes that the dss+ engagement helped in two key ways. First, according to Allen, "Risk reduction efforts are selectively focused on higher risk activities.
When employees focused their efforts on reducing the risk of a task, the risk reduction has been significant." Second, he added, "Risk reduction efforts have also generated greater risk awareness of key hazards on an ongoing basis, and those hazards are not ‘wallpaper’ anymore."
Changing the existing behavior to focus more on anticipating risks rather than just working safely requires workers, managers and executives to each adopt a new way of thinking. Fundamental to this change is adopting the mindset that risk can never totally be eliminated. By understanding that risk of an incident is always present, workers are more likely to anticipate situations that present the potential for an incident to occur and to act more safely.
Furthermore, risk management requires the continuous involvement of employees who actually do the work. Employees operating equipment and machinery know where hazards and risks exist, and are therefore in the best position to identify them to managers and executives.
Those companies that truly want to improve their safety performance should focus on reducing risk, not merely operating safely. By measuring and quantifying the many risks that exist throughout the organization, companies are better able to anticipate, prioritize and mitigate those opportunities that are most likely to lead to an incident. It requires that everyone in the company change their outlook to be aware that risk is always present and to be alert to situations that could lead to a potential incident occurring. By endeavoring to manage risk, companies will in turn find they operate even more safely.