Usina Coruripe
Usina Coruripe is the largest producer of sugar and ethanol in the North-Northeast of Brazil and one of the 10 largest producers of these products in Brazil. It has seven operating units: a main office, a logistics terminal and five industrial units: Iturama, Campo Florido, Limeira do Oeste, Carneirinho and Coruripe, employing around 9,200 employees. Together, its industrial plants have the capacity to process 14.4 million tons of sugarcane annually, resulting in 470 million liters of ethanol, 20 million bags of sugar, in addition to the generation of more than 680,000 MWh of energy and revenues of R$ 2.3 billion. Being one of the largest and most important agribusiness companies in Brazil, it has already been recognized by Época Negócios (2017), Mastercana Brazil Award (2017), Rural Money (2017 and 2015), IDEA Group (2015/16 and 2016/2017) and Safety Award (2015).
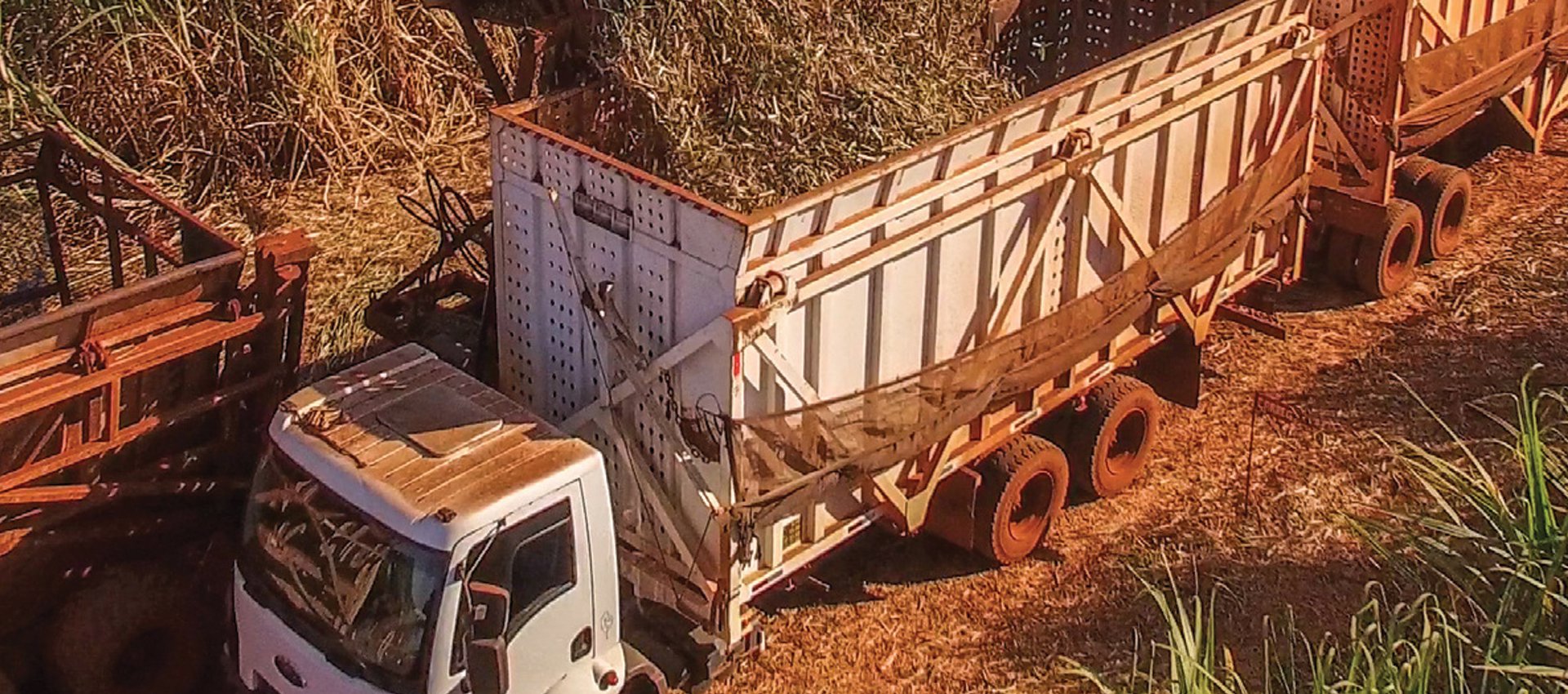
Usina Coruripe: Zero Accident Always
The partnership between Usina Coruripe and dss+ began in 2014 after the client had conducted an internal assessment which revealed that 85% of accidents were caused by unsafe behavior. As a result, it was necessary to take an aggressive measure so that everyone would work in a safer way, and to support this journey, dss+ created the program named "Zero Accident Always", based on the company's Safety Policy, to implement in every one of the client's 7 operating units.
This program focused on the implementation of the dss+ STOP® program, an award-winning, world-renowned behavioral observation program. In total, 21 STOP® groups were trained by dss+ consultants and plant trainers. To sustain the results, a STOP® Subcommittee was created for each operational unit, responsible for analyzing the program's monthly data and determining the necessary action plans. In addition, the practice of a Daily Safety Dialogue (DSD) was also instrumental in the dissemination of these results and action plans. Department meetings were also established with the operational staff and the Central Safety Committee Meeting held monthly with president and directors. Safety has become ingrained and valued by the organization.
The biggest challenge in the process was breaking down some old paradigms and concepts. It was necessary to align the role of the leader, who did not understand the safety dimension, and transferred responsibility to the occupational safety technicians. However, after much training and guidance, most leaders took a stand as an example of working safely. The first phase of the Zero Accident Always Program, between 2014 and 2016, stimulated important results: driving the dss+ STOP. program reduced safety deviations by 25%; there was a 55% decrease in accidents with withdrawal, as well as a 60% reduction in frequency and severity. In addition, a productivity increase of 17.4% over two years was experienced (comparison of 2015/16 and 2013/14 crops).
Second Phase
In 2017, Usina Coruripe once again sought dss+ to sustain Phase 1 results, improve its safety practices, and advance culturally to reduce risks and accidents. The new project developed by dss+ worked on two distinct working fronts to support the obtained safety results: on the one hand, the improvement of the process safety management system (PSM); on the other, the promotion of a safety culture.
The first front was concerned with the improvement of process risk management (PSM), as a assessment in 2016 identified that these practices had opportunity for improvement. Through the analysis of the procedures, the results of investigations and the statistics of the units, a review of critical safety processes was made, seeking to improve the technical model. In addition, new processes of process safety analysis (PSA), change management and investigation of deviations, accidents and incidents were implemented. In order to provide PSM tools to employees, several training sessions were conducted: risk analysis, change management, mechanical integrity, quality assurance, and emergency response and response plan.
The second working front dealt with the cultural evolution in the company. It was necessary to foster an interdependent safety culture in which all employees feel responsible for the safety of their colleagues as much as they feel responsible for their own safety.
Understanding that leaders and managers are the main moulders of corporate culture, several training sessions were conducted with dss+ consultants:
- Development of core competencies of supervisors and leaders (through the Supervisor on the Scene program);
- Improvement of the capacities of directors, managers and coordinators in relation to safety (DNA program);
- Greater comprehensiveness in behavioural observation practices with the formation of new dss+ STOP. for All multipliers, aiming to reach all levels of the company. Results With the activities performed in Phase 2 of the Zero Accident Always Program, the five units of the Coruripe Plant obtained improvements in their results.
Significant studies were made regarding the attitudes and behaviours of employees and leaders at all levels of the Coruripe Plant, who demonstrated their commitment to the Zero Accident Program and were committed to taking care of everyone’s safety, which was reflected in the indexes of obtained. “I believe that I have changed mainly in the matter of safety, taking a more clinical view of the consequences of my actions. I changed in the subject discipline, always looking for objectivity and punctuality, “says the Supervisor of Agricultural Planning of the Alagoas unit. “I also changed communication, being simple and direct, and mindful of my bodily languages.”
After four years of partnership with dss+, Coruripe Plant also saw substantial improvements in its safety ratings:
Future Vision
In view of the excellent results obtained with the partnership with dss+, Usina Coruripe intends to continue its journey towards operational excellence with the implementation of the third phase of the Zero Accident Always Program, with the objective of reinforcing the dss+ STOP. program (implemented in Phase 1) and include new risk awareness solutions, as well as enhancing PSM techniques in the operation.