VELUX Group
In a far-reaching programme, the VELUX Group has revitalised safety at its more than 20 global production and warehouse sites with the help of work safety consultant dss+.

VELUX Group: Shedding Light on Work Safety
The VELUX brand is a name that is known throughout the building industry for its roof windows, skylights and blinds. What is less well known is that the VELUX Group runs its business on the Model Company Objective defined as a company working with products which are useful to society, and that treats its customers, suppliers, employees of all categories and shareholders better than most other companies. Another characteristic of the VELUX Group is the corporate value it places on local initiative, creating flexibility for their manufacturing sites in more than 11 countries.
In 2009, Kim Jonas, VELUX Health, Safety and Environment Manager, found that work safety performance across the group was plateauing. "We had a decent safety performance, had worked with the OHSAS safety system at our sites, and used lagging indicators and Key Performance Indicators (KPIs) for years at a corporate level to set requirements. We don't work in a hazardous industry like chemicals. Our safety risks come mainly from cutting, working at height, maintenance, forklifts, cleaning and transport. So, you would think the risks aren't that great. But every year, we still had employees losing fingers in wood-cutting machinery."
As the VELUX Group aspires to treat its employees better than other companies, the group wanted to find a solution to this stagnation and decided to call in a work safety expert. "We needed a consultant who was capable of providing both corporate level strategy and programme development, as well as local level implementation support at all our sites in the national language from France to Hungary, Denmark to America or Russia," Mr. Jonas says. The VELUX Group turned to dss+ a leading operations management consulting company.
dss+ began by carrying out work safety assessments at four pilot sites in 2010. This included a perception survey of the employees, which found that too many of them regularly took safety shortcuts. They were operating in a "dependent" work safety culture. In other words, employees followed safety rules, but did so without thinking work processes through for themselves. The group was focused on technical safety and lagging indicators. Safety was often driven by safety professionals rather than line management and this was reflected in the VELUX safety organisation.
Once dss+ had shared its findings of the pilot site assessments with the VELUX Group, the company realised it needed a global programme to reach out to all of its sites.
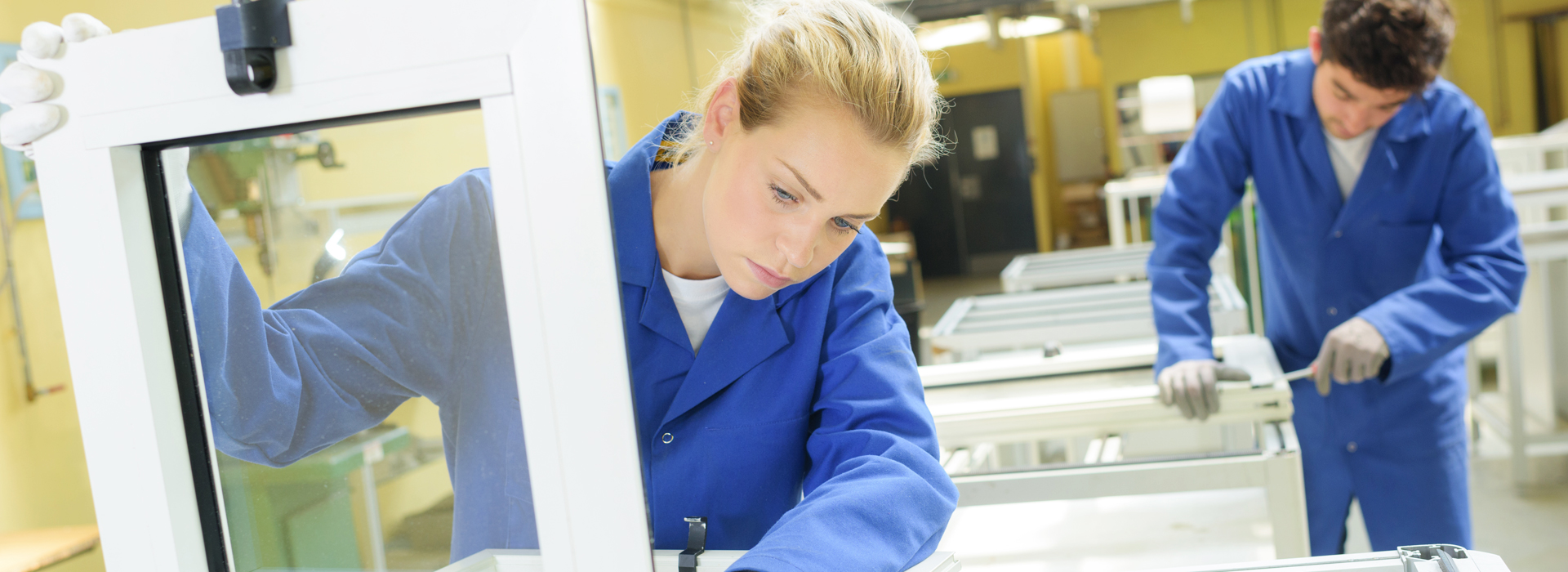
Gaining a management perspective on safety
Even though VELUX began work at a corporate level to develop company-wide safety standards, the sites were very much involved in defining these common standards. In parallel, dss+ designed roll-out of the programme to local sites in waves. VELUX sites differ enormously in size. Although the average number of employees at a VELUX production company is around 300, some are much larger with over a thousand employees while the smallest site only numbers 60.
dss+ programme manager Esat Birgen admits "it was a mammoth project. Sites were all at different safety levels. We had to develop and introduce a corporate programme to sites that were normally driven locally. It was vital to get the balance between corporate and local right, yet still ensure that, at the end, everyone would be able to speak and understand the same safety language."
Over the lifetime of the project, dss+ had a team of 15 different consultants working in nine different languages to assist local sites. Each production plant was helped in carrying out a gap assessment to establish the current safety culture status quo and check the relevance of planned activities. dss+ trained managers and supervisors, and supported the setting up of a local integrated safety organisation consisting of a project leader, safety committee, sub-committees and local trainers. The consultants also carried out progress evaluations after 12 months to check on improvements.
As Kim Jonas explains, "many of our sites had the feeling that they were already doing well, but the Key Performance Indicators (KPIs) from the top were getting tougher and tougher. They did not have the resources locally to make the safety cultural step-change improvement needed. The new Safety Excellence programme has given them a management perspective on safety that they didn't have before. With this project, we have helped lift local competencies, something that would have been difficult for them to achieve on their own."
It was always very important for VELUX that the safety changes they made would be sustainable. They wanted to ensure that the project results are not a one-time success, but a lasting improvement. Esat Birgen says: "Our approach is to coach local teams so they can themselves develop and implement local procedures based on corporate standards, and we train up internal trainers who are then in charge of instructing employees."
Meanwhile, VELUX and dss+ partnered with the management of the Safety Excellence Programme at the Østbirk site in Denmark, developing training programmes for managers, supervisors, employees and safety professionals; running workshops in waves for all sites; following up with local activities; coaching senior leaders; setting up a safety culture assessment methodology and training internal assessors to work with it.
A shift in safety attitudes
Senior leaders at the VELUX production companies have undergone a marked change in attitude to safety as a result of all these activities. They have become very engaged in all safety efforts and now regularly take part in Safety Walks, which connect executives with local staff. As George Walker, general manager of the VELUX site in Rostov, Russia puts it: "We now have a common understanding of safety. It is not just something official and formal on a spreadsheet – more a part of our everyday work life – with safety discussions as a natural part of meetings and activities throughout the factory."
A similar shift in behaviour was noted by Zoltán Vincze, general manager at the LKR Hungary factory, the largest production site of the VELUX Group. "Traditionally, Hungarians don't pay very much attention to their health and safety, so they were quite sceptical and there was a lot of 'I've been doing it like this for 20 years and so far, it has worked out fine'," he says. "The tipping point was the training of the employees. Since then, their behaviour has changed remarkably and they are asking for more information and want to be more involved and make a contribution themselves."
This is borne out by Rozsits Gábor, an employee at the same site. "The training video about the man who lost his sight because of an accident at work really made me think. Because he wasn't wearing safety goggles, he lost his sight. It was quite a shock to see that a single little mistake can have disastrous consequences for the lives of yourself and your workmates. I think the way to achieve zero industrial accidents is for the staff to talk about specific safety issues all the time, come up with suggestions for necessary measures and training, and then discuss them with management. In that way, we become part of the solution."
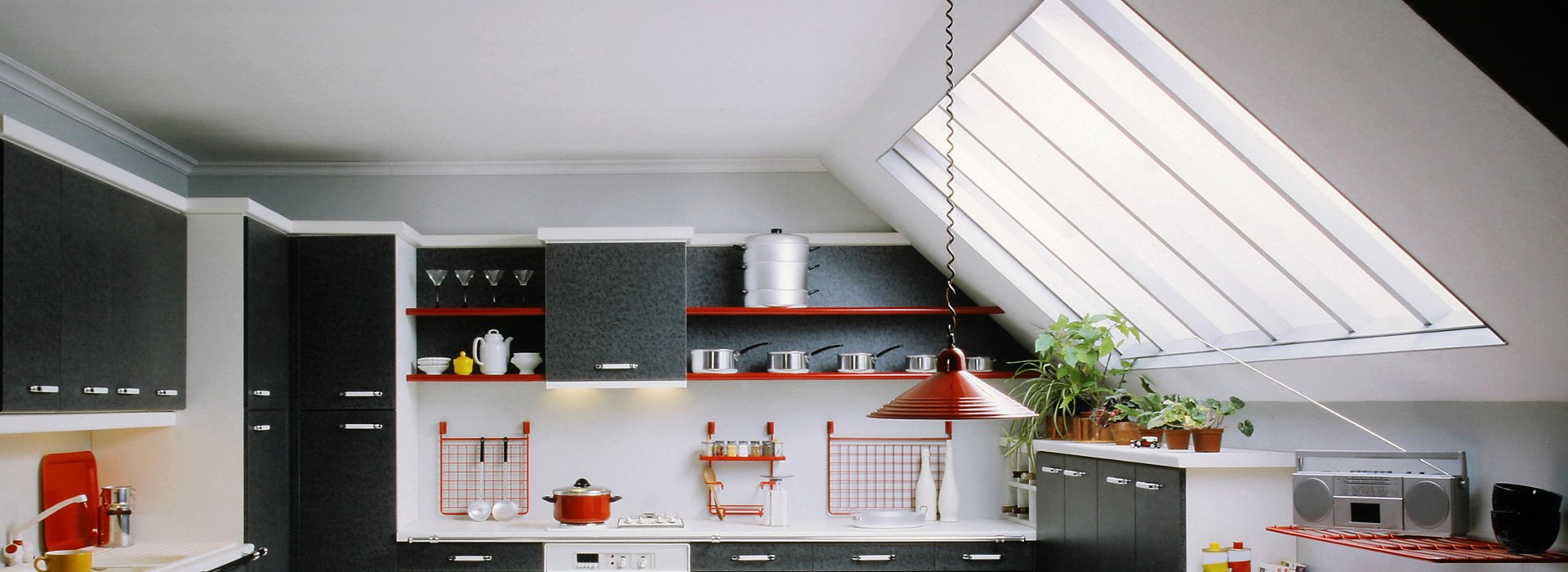
Seeing improvements
The VELUX Group encourages employee involvement by rewarding reporting of near-misses and safety improvements, and ensuring managers follow these reports up. Employees know they are taken seriously and that has also helped to improve the safety mind-set throughout the company. This change in attitude translates into different behaviour, which in turn has an effect on incident rates.
Kim Jonas is keen to point out that there now is a real company pride. "Employees are proud of working for the VELUX Group. They are proud of their safety achievements and that has produced a lot of positive energy. 'Sensibilisation' for safety has really happened. I often hear people saying they take safety home with them. I am the same. I am suddenly noticing unsafe behaviour in areas I had not thought of before. This change in safety behaviour has also had a beneficial effect on productivity, we believe, as the operational discipline we have gained in safety will reflect in our other operational activities as well."
More tangible results can be seen from the safety statistics. Some of the first sites that introduced the Safety Excellence programme have now gone more than five years without a single Lost Workday Case. Since the start of the programme in 2010, the VELUX Group has seen a drop in overall first-aid cases from a range of 5,000 in the 2008-2010 time period to about 2,500 in 2013. The accident frequency (Lost Workday Cases per million working hours) has decreased from a baseline before the programme of seven to a current April 2014 level of one. Kim Jonas is clear about the cause. "Our safety culture has definitely improved – and we can now also track it by our safety assessments. We've reduced unsafe conditions and unsafe behaviour. And the reduction in accidents and incidents has allowed us to save hidden costs. We estimate that the cost of introducing this safety programme at all our sites will pay for itself in five to six years although we never started the programme to gain any savings, but to protect our employees even better."
The VELUX Group has carried out its first group of own assessments of site performance looking at management commitment, incident investigation, effective communication, observations and audits, line management responsibility and many other issues. Throughout, the sites have performed better than during their initial assessment by dss+. The VELUX site at Langfang City in China was also ranked as the most advanced in safety excellence in the Hebei province by the local safety authorities.
Søren Chr. Dahl, head of VELUX Production says: "I'm very happy about the positive development in our safety performance. Our founder formulated the ambition to be a model company that treats its employees better than most other companies. It is therefore natural for us to have safety as a focus area. I would like to stress that even though good safety performance is good business, safety is important to us because of our employees. I can see an improvement in our safety culture, but we have not reached our target yet, so our safety journey towards the goal of zero accidents will continue."
Sustaining the safety performance
The VELUX Group will complete the implementation of the Safety Excellence programme developed together with dss+ in 2014.
Kim Jonas concludes by saying, "When we started the programme we were very ambitious. We wanted to be able to carry out our own assessments, like dss+. dss+ trained co-assessors during workshops so that we can do that. We now have 20 trained VELUX safety assessors, all from local sites, who are becoming extremely accomplished in making safety assessments. In addition, they also act as skilled local change agents. And we now speak the same safety language throughout the company. We can talk to and understand each other from Denmark to Poland, Russia, China and the USA. We know exactly what is meant by a 'safety walk' and "safety contact" wherever that may be in the world. With the Safety Excellence Programme the VELUX Group has a common system to deal with common issues. This gives us the confidence that safety improvements will be sustainable – across the board."