What's Happened to LOTO?
Since OSHA first issued a standard procedure for Lockout/Tagout (LOTO) to control energy-related risks back in 19891, industry and operating procedures have moved on. The digital age has arrived. Locking out and tagging out should, in theory, be more straightforward and quicker than ever before.
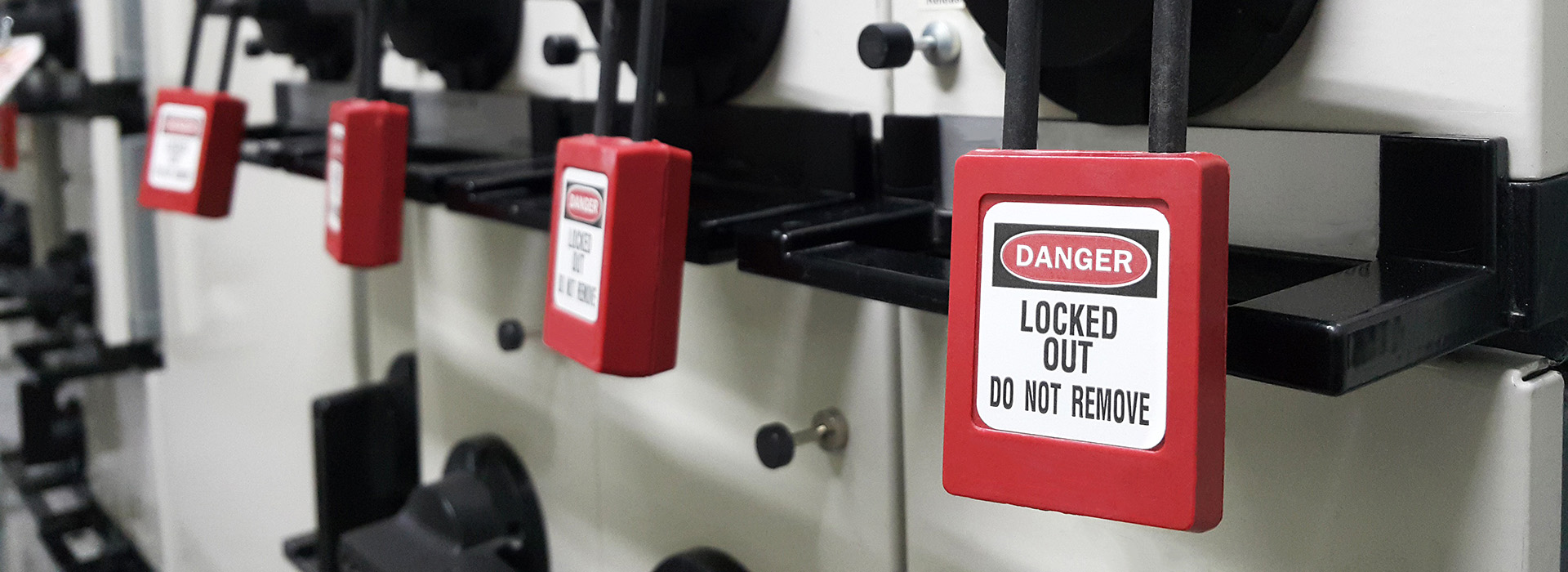
And yet, energy-release incidents persistently keep occurring, most with serious, often fatal consequences. Lockout/Tagout violations continue to be cited as one of the top 10 OSHA violations every year. The Italian cable car disaster in May 2021 is just one example. And it is not an isolated incident. The number of LOTO-related accidents appear to be on the rise across Europe. Our team in Belgium, for instance, estimates the number of LOTO breaches to be 4.5 times higher in the first half of 2021 than in the same period last year. What is going on?
The obvious explanation is that the pandemic artificially depressed the number of safety incidents in 2020 in general, including LOTO, so that it seems only natural for occurrences to shoot up once operations resumed. But that justification falls flat when you examine the figures more closely. LOTO violations are not only up on 2020 but on pre-pandemic levels. This is most likely due to the increase in non-standard restart activities in 2021 as employees carried out unfamiliar processes.
Some risks, however, can have more severe outcomes than others. LOTO failures (see Figure 1) typically lead to such high-potential events. So LOTO near misses should be taken seriously by incident investigators to understand potential consequences in order to prevent future incidents.
Figure 1: LOTO incident = energy + accidental equipment restart
Figure 2: LOTO hierarchy of controls
It is worth examining what makes LOTO such an important and highly effective procedure that offers significant protection against high-potential risks. LOTO is, in fact, an implementation of a certain set of controls. It is so powerful because it combines employee-focused controls with exposure-related controls (see Figure 2). This means that it builds employee capability and risk awareness at the same time as considering how to remove the source of risk entirely. Coming up with and implementing effective LOTO procedures therefore requires a solid understanding of the hierarchy of controls and how they interact.
Many organisations are now starting to introduce a Lockout/Tagout/Try-out (LOTOTO) process as part of their safety management system to strengthen the procedure in itself. That is all well and good, but how do you ensure LOTO or LOTOTO procedures are actually followed?
Effective LOTO or LOTOTO implementation needs to be anchored in Processes, Technology, Governance and even more importantly, people's Mindset, Behaviours and Capabilities. They need to be supported by the safety culture of the organisation. They have to become second nature and employees need to understand the benefit to themselves. This is as true of LOTO as it is of any other safety policy or aspect of safety culture.
Beyond applying the same fundamentals to LOTO as to any other key safety area, what more can you do to reinforce LOTO specifically?
5 Critical actions to improve the effectiveness of LOTO procedure
Don't neglect the learnings from near misses
If a normal LOTO task takes three hours and someone has done it in two, do you say, "great job" or ask, "how did you do that"? Always investigate LOTO near misses as the potential consequences are so severe and learn to ask the right questions.
Critically & regularly review the hierarchy of controls
It is every employee's responsibility to identify risks, but it is management's responsibility to figure out how to take action at the highest level in the hierarchy of controls (see Figure 2). Any procedure depends on being implemented. Instead of simply issuing more PPE, management should look at whether it is possible to eliminate a risk. If not, can it be mitigated, is there an alternative solution, is it possible to put a barrier in place?
Implement life-saving rules & corresponding consequence management
Life-saving rules need to be clearly communicated and backed by a fair and consistent consequence management system. One thing is having clear rules, another is acting on their violations. Herein, we recommend a thorough investigation as to why the rule was ignored or broken, and to act fairly but decisively in line with the investigation's findings. As a senior manager at one of our clients recently put it: "I would rather send someone home without a job, than to not be able to send him home at all". However, we also recommend very explicitly building in reward and recognition. That can be as simple as naming someone as employee of the month or citing an action taken by employee in a positive way.
"Always investigate LOTO near misses as the potential consequences are so severe and learn to ask the right questions."
Develop capabilities and risk awareness at the shopfloor level
Employees at the shopfloor level are the first to deal with LOTO(TO) risks as they arise. It is therefore crucial that they have the job-specific capabilities and risk awareness to deal with these risks. Spend sufficient time on onboarding training and on regular refreshers. Have a Management of Change process in place to ensure that your employees are aware of any changes in procedures or production processes. And finally, don't rely solely on formal rules and procedures, but think about how to build your shopfloor teams' risk awareness. This will strengthen their ability to deal with unexpected situations as they arise.
Elevate LOTO to leadership
Most LOTO procedures have a highly operational, often technical, component to them which can make them less intuitive for managers without a technical background. We recommend elevating LOTO and its importance to the highest levels of leadership in any organisation, even if this might require some education on the technical details of the relevant production processes. Making leadership more aware of how important these procedures are will help them send the right signals to the shopfloor about the critical role of LOTO.
"We recommend elevating LOTO and its importance to the highest levels of leadership in any organisation."
Conclusion
LOTO procedures are not silver bullets. Even if you have solid procedures in place and people adhere to them, that does not mean the risk is solved. LOTO is not just important in a factory setting or to control electrical or mechanical risks. It is important in any setting where maintenance is carried out on a machine and where human lives are impacted by the movement of a machine. The onus is on us to continuously look through the hierarchy of controls and find better ways to mitigate the risks we face.
Business leaders
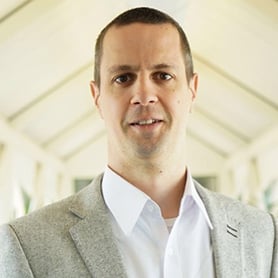
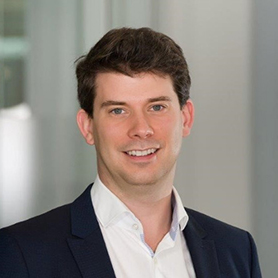
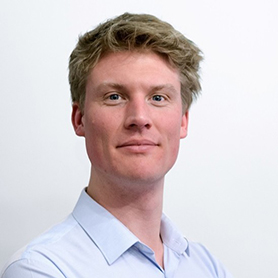
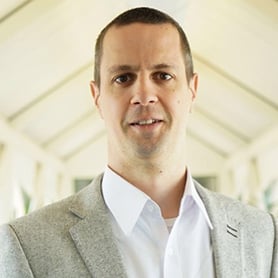
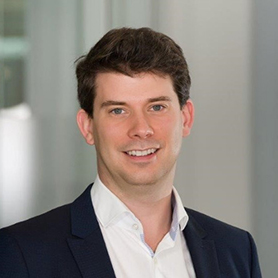
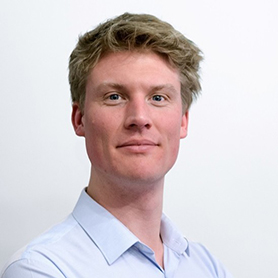